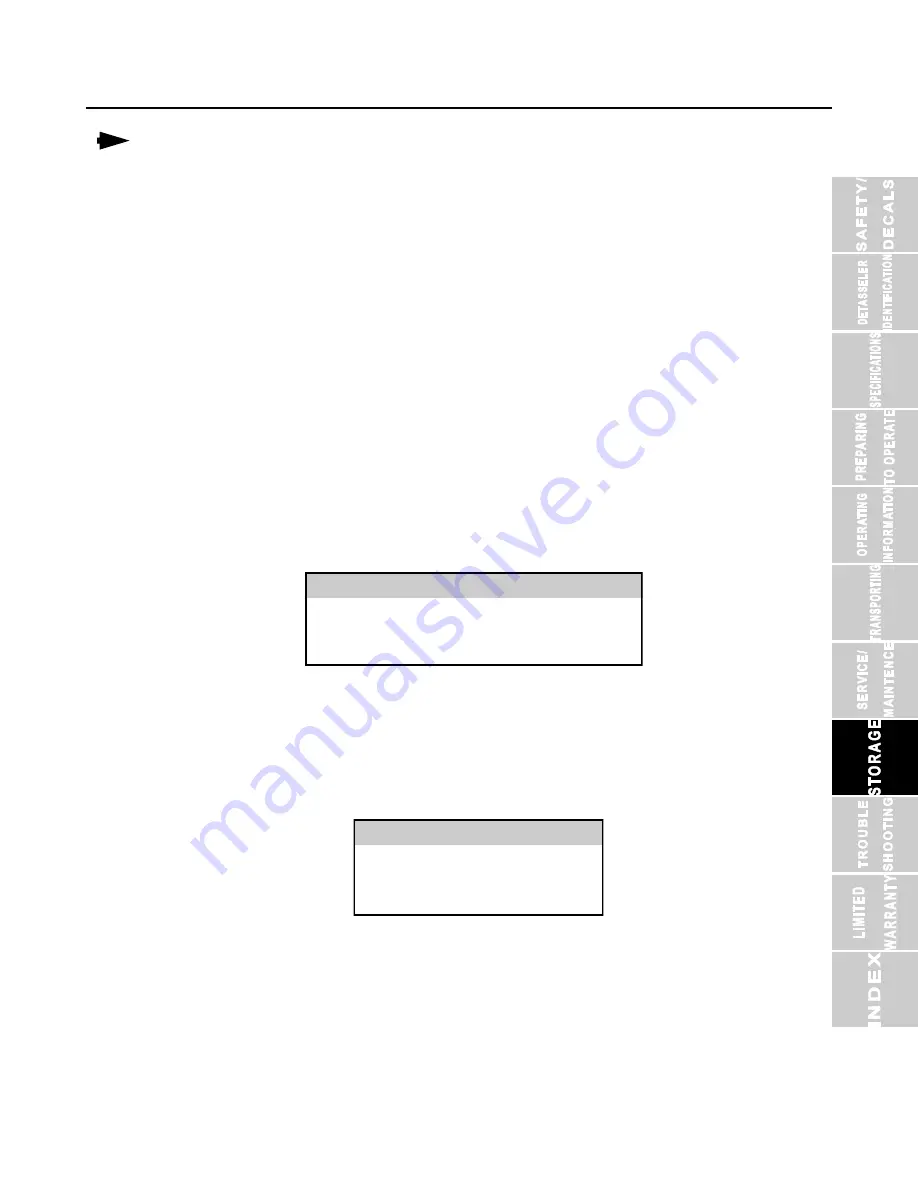
IX.
STORAGE
x
NOTE:
Protective compounds such as grease can
harden under exposure to weather condi-
6. Completely clean the detasseler.
7. Review section seven on maintenance (pages XXX-XXX), and perform all needed
services as instructed.
8. For starting instructions, see pages XX-XX in section five on operating
information.
11. Use a multi-purpose grease to coat exposed hydraulic cylinder rods to prevent
rusting which could result in cylinder damage.
12. If the sprayer must be stored outside, cover it with a waterproof cover.
1. Inspect the condition, and test the air pressure, of all tires. Please see page XX
for information regarding proper tire maintenance.
2. Carefully unseal all openings that were sealed in the storage process.
3. Clean and reinstall the battery. Be sure to attach the battery cables to the proper
terminals.
4. Tighten all belts. Inspect and replace any worn belts. For information on belts, see
page XXX or XXX.
5. Check engine oil, hydraulic oil, and engine coolant levels; add, if necessary. A
mixture of 50/50 antifreeze and water will cool adequately in summer as well as
protect in winter.
B. Removing the detasseler from storage.
NOTE:
See Warranty on page XXX
concerning
improper storage
.
STORAGE CONTINUED
Summary of Contents for 204
Page 133: ...x IX TROUBLE SHOOTING TASSELTROL LS SYSTEM ELECTRICAL CONTINUED FIG 9 1 1 2...
Page 134: ...x IX TROUBLE SHOOTING NOTES...
Page 140: ...138 NOTES...
Page 141: ...x...