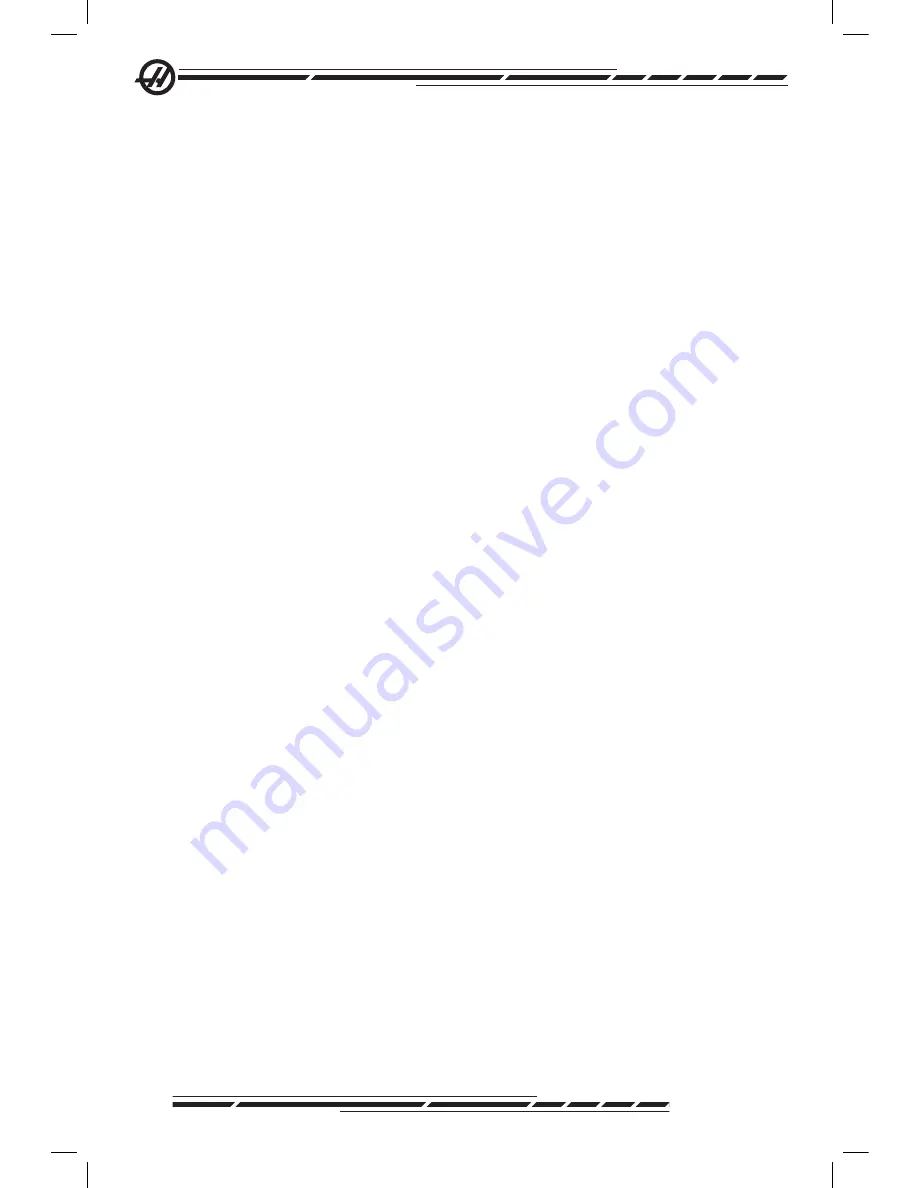
146
96-8000 Rev AC
May 2010
position.
If an
I
,
J
, or
K
is specified, the appropriate axis work offset is shifted by the
amount in the
I
,
J
, or
K
command. This allows the work offset to be shifted
away from where the probe actually contacts the part.
Notes:
The points probed are offset by the values in Settings 59 through 62.
Use G91 incremental moves when using a G36.
Use the assigned M-codes (for example M53 and M63) with a dwell to turn the
spindle probe on or off.
Example:
M53
G04 P100
M63
Program Example
O1234 (G36)
M53
G04 P100
M63
G00 G90 G54 X1. Y0
Z-18.
G91 G01 Z-1. F20.
G36 X-1. F10.
G90 G01 X1.
M53
G04 P100
M63
G00 G90 G53 Z0
M30
G37 Automatic Tool Offset Measurement (Group 00)
(This G-code is optional and requires a probe)
F
Feedrate in inches (mm) per minute
H
Tool offset number
Z
Required Z-axis offset
Automatic Tool Length Offset Measurement (G37) is used to command a probe
to set tool length offsets. A G37 will feed the Z-axis in an effort to probe a tool
with a table mounted probe. The Z-axis will move until a signal from the probe
is received, or the travel limit is reached. A non-zero H code and either G43 or
G44 must be active. When the signal from the probe is received (skip signal)
the Z position is used to set the specified tool offset (Hnnn). The resulting tool
offset is the offset between the work zero point and the point where the probe
is touched.
The coordinate system (G54-G59, G110-G129) and the tool length offsets
(H01-H200) may be selected in this block or the previous block.
Summary of Contents for 96-8000
Page 15: ...6 96 8000 Rev AC May 2010 Mill Warning Decals ...
Page 16: ...7 96 8000 Rev AC May 2010 Safety Lathe Warning Decals ...
Page 41: ...32 96 8000 Rev AC May 2010 ...
Page 93: ...84 96 8000 Rev AC May 2010 ...
Page 129: ...120 96 8000 Rev AC May 2010 ...
Page 133: ...124 96 8000 Rev AC May 2010 ...
Page 268: ......
Page 269: ......