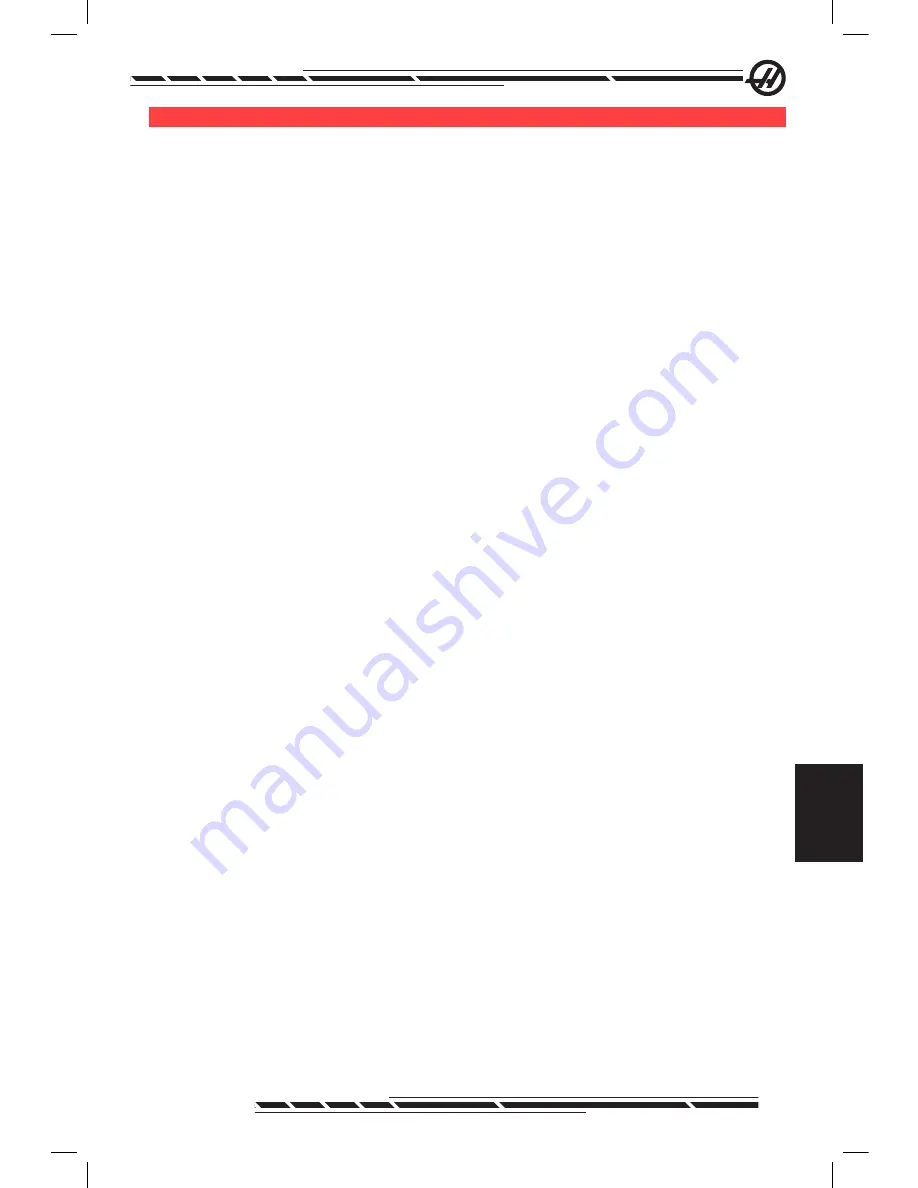
133
96-8000 Rev AC
May 2010
G
&
M
Codes
Settings
G c
odeS
(P
reParatory
f
UnctionS
)
G00 Rapid Motion Positioning (Group 01)
X
Optional X-axis motion command
Y
Optional Y-axis motion command
Z
Optional Z-axis motion command
A
Optional A-axis motion command
G00 is used to move the machines axis at the maximum speed. It is primarily
used to quickly position the machine to a given point before each feed (cutting)
command (All moves are done at full rapid speed). This G code is modal, so
a block with G00 causes all following blocks to be rapid motion until another
Group 01 code is specified.
Programming note: Generally, rapid motion will not be in a straight line. Each
axis specified is moved at the same speed, but all axes will not necessarily
complete their motions at the same time. The machine will wait until all motions
are complete before starting the next command.
Incremental or absolute position commands (G90 or G91) will change how
those axis motion values are interpreted. Setting 57 (Exact Stop Canned X-Y)
can change how closely the machine waits for a precise stop before and after a
rapid move.
G01 Linear Interpolation Motion (Group 01)
F
Feedrate in inches (mm) per minute
X
Optional X-axis motion command
Y
Optional Y-axis motion command
Z
Optional Z-axis motion command
A
Optional A-axis motion command
,R
Radius of the arc
,C
Chamfer distance
This G code moves the axes at a commanded feed rate. It is primarily used to
cut the workpiece. A G01 feed can be a single axis move or a combination of
the axes. The rate of axes movement is controlled by feedrate (F) value. This
F
value can be in units (inch or metric) per minute (G94) or per spindle revolu
-
tion (G95), or time to complete the motion (G93). The feedrate value (F) can be
on the current program line, or a previous line. The control will always use the
most recent F value until another F value is commanded.
G01 is a modal command, which means that it will stay in affect until canceled
by a rapid command such as G00 or a circular motion command like G02 or
G03.
Once a G01 is started all programmed axes will move and reach the destina
-
tion at the same time. If an axis is not capable of the programmed feedrate the
control will not proceed with the G01 command and an alarm (max feedrate
exceeded) will be generated.
Summary of Contents for 96-8000
Page 15: ...6 96 8000 Rev AC May 2010 Mill Warning Decals ...
Page 16: ...7 96 8000 Rev AC May 2010 Safety Lathe Warning Decals ...
Page 41: ...32 96 8000 Rev AC May 2010 ...
Page 93: ...84 96 8000 Rev AC May 2010 ...
Page 129: ...120 96 8000 Rev AC May 2010 ...
Page 133: ...124 96 8000 Rev AC May 2010 ...
Page 268: ......
Page 269: ......