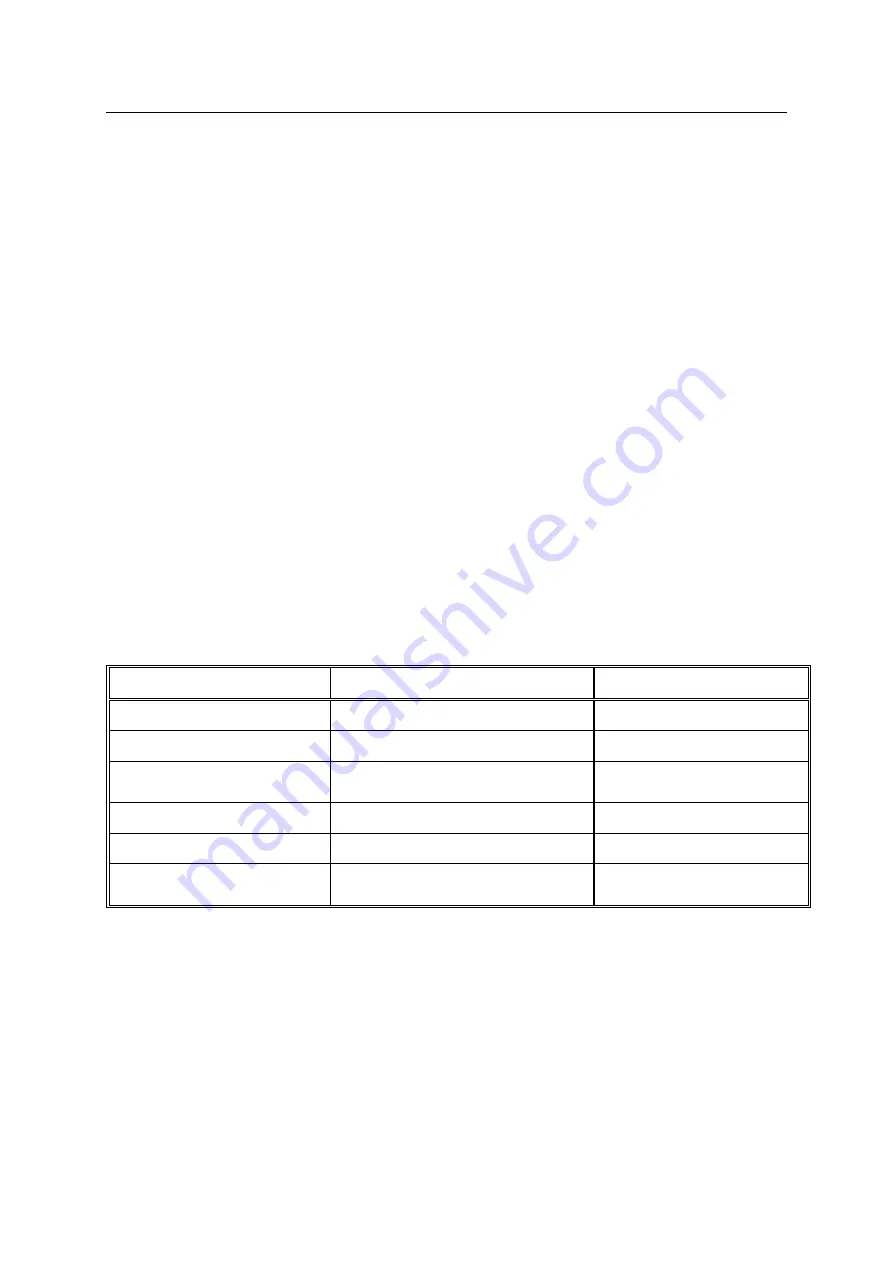
GSI Group - Laser Division
JK300HP/JK300P/JK125P
Issue 2.0
Pre-installation and User Manual
Part No: 1EA300E01
Page
163 of 172
Under normal conditions, adequate gas shielding can be provided via a pipe to the weld area
around the beam/material interaction point. Gas flow should typically be 10 - 20 litres/minute
Argon.
Where materials such as Titanium and its alloys require processing with zero contamination,
it is necessary to employ a more sophisticated gas delivery system.
Using a Gas Shoe will achieve the conditions required to process materials without
contamination. This device provides an inert atmosphere not only in the region of the molten
weld puddle but also to the solidified weld as it cools. Slightly more gas flow is required when
using the gas shoe, typically 30 - 50 litres/minute Argon.
Processing materials such as Stainless Steel, Aluminium and Titanium may require inert gas
shielding to the Weld Underbead during full penetration welding. A very effective method is
to introduce a channel flooded with inert gas underneath the weld. A gas inlet at one end of
the channel and an outlet at the other is one method of maintaining a constant stream of gas
along the underbead. The gas outlet should be slightly constricted to help retain the gas at
the underbead but not to cause excessive pressure. Excessive pressure causes concavity of
the Underbead or blows holes in the weld. Flow rates should typically be 2 - 5 litres / minute.
The absence of gas shielding when welding thin sheet mild steel (< 0.3 mm) may not
adversely affect the properties of the weld and will, in general, allow welds to be produced at
higher speeds and with greater penetration.
For most welding applications, Argon is efficient and cheap. The use of Helium as a
shielding gas is not normally necessary. However, the use of Helium when welding
Aluminium alloys is a significant benefit as it offers improved process stability. This results in
a smoother top bead and allows greater penetration to be achieved.
The table below gives details of Gas Shielding requirements and the recommended
Shielding Gas.
Material
Gas Shielding Requirements
Recommended Gas
Mild steel 0 -3.0 mm
Gas shielding not always necessary
Argon
Steel > 3.0 mm
Gas shielding recommended
Argon
Stainless steel and nickel
alloys
Gas shielding recommended
Argon
Aluminium alloys
Gas shielding essential
Argon/Helium
Titanium alloys
Gas shielding essential
Argon
Copper alloys
Gas shielding may prevent effective
coupling of the beam into workpiece
10.7 Fume and Spatter Control
During welding operations it is normally necessary to prevent spatter and fume from
impacting and accumulating on the Cover Slide that protects the Focusing Lens.
Fume and spatter control is easily achieved by use of a Cross-jet. This is a high velocity
compressed air jet, directed perpendicular to the beam path, in front of the Focus Head
between the Cover Slide and the workpiece.
If a Cross-jet is used, care must be taken to locate it in a position where the airflow does not
disrupt the gas shielding.
Petitioners Canadian Solar Inc. and Canadian Solar (USA) Inc.
Ex. 1025, p. 163