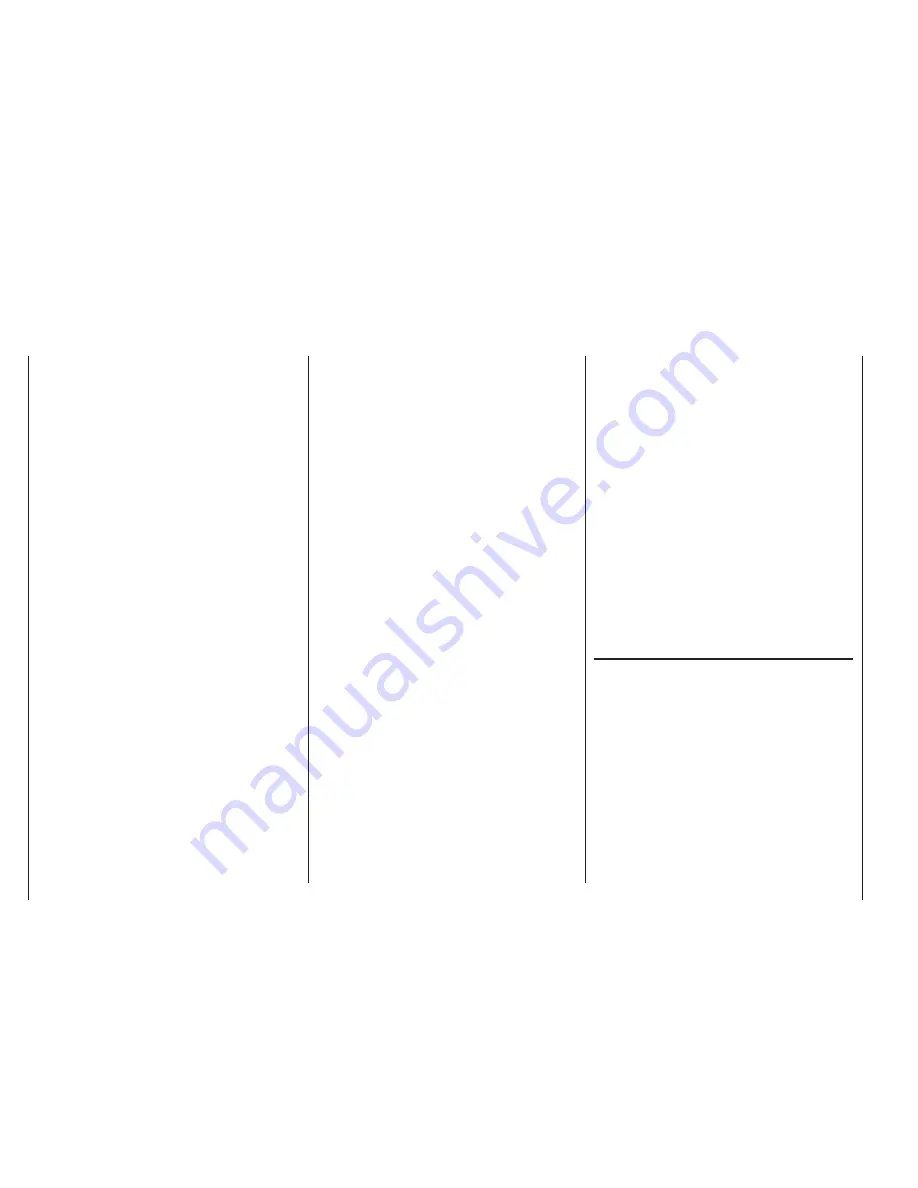
114
Programming example: F3A model
the mixers of a computer radio control system are then
required to compensate for these defi ciencies. In this
section we will describe how to carry out the adjust-
ments required, but please note the following points
before we get started: it is vital to ensure that the model
is built as accurately as humanly possible, is balanced
perfectly around the lateral and longitudinal axes, and
that motor downthrust and sidethrust are set correctly.
Rudder causes unwanted movement around the
1.
longitudinal and lateral axes
It is often the case that a rudder command caus-
es the model to rotate slightly around the longitudi-
nal and / or lateral axis. This is particularly trouble-
some in what is known as knife-edge fl ight, where the
model’s total lift is generated by the fuselage, aided
by the rudder defl ection. The result is that the mod-
el rotates and changes heading slightly, as if the pi-
lot were applying aileron or elevator at the same time.
These tendencies have to be corrected with compen-
sation around the lateral axis (elevator) and around
the longitudinal axis (aileron).
These corrections can be achieved easily with the
mx
-16iFS, exploiting the »
free mixer
« once again.
For example, if the model rotates to the right around
the longitudinal (roll) axis when the rudder is defl ect-
ed to the right for a knife-edge pass, then a mixer is
set up which defl ects the ailerons slightly to the left.
Heading changes around the lateral (elevator) axis
can be corrected in a similar way using a mixer act-
ing upon the elevator:
a) Correction around the lateral axis (elevator)
MIX
“rd
¼
el”
ASY
mmetrical setting. The exact values required
must be found by fl ight testing.
b) Correction around the longitudinal axis (aileron)
MIX “rd
¼
ar”
ASY
mmetrical setting. The exact values required
must be found by fl ight testing.
In most cases relatively small mixer values are called
for – typically below 10% – but this does vary from
model to model.
Vertical climb and descent
2.
Many models exhibit a tendency to deviate from the
ideal line in vertical climbs and descents. To correct
this we need an elevator neutral position which varies
according to the throttle setting. For example, if the
model tends to pull out of a vertical descent by itself
when the motor is throttled back, slight down-elevator
must be mixed in at this throttle setting.
MIX “c1
¼
el”
As a rule you will need to set mixer values below 5%,
but once again there is no substitute for test-fl ying.
Rolling (movement around the longitudinal axis)
3.
at idle
When you reduce the throttle setting, the model may
tend to roll slightly in one direction. Clearly an ai-
leron correction must be made. However, it is much
more elegant to let a mixer correct this effect for you
than to move the stick manually. Once again, a mixer
needs to be set up:
MIX “c1
¼
ar”
As a rule you will need to set mixer values below 5%,
but once again test-fl ying is called for.
The adjustment process should only be carried out
in calm weather. Often all you need to do is apply the
mixer in the control segment between half-throttle
and idle. To achieve this, leave the Offset point at the
centre position, and set up the mixer
ASY
metrically.
Rolling when ailerons and fl aps are extended
4.
If you fl y the landing approach with both ailerons de-
fl ected up, the model may show a tendency to roll
slightly due to minor variations in aileron servo trav-
el (or constructional inaccuracies); i. e. the model may
turn to either side by itself. Once again, this tenden-
cy can easily be corrected using a mixer to vary the
compensation according to the position of the ailer-
ons / landing fl aps.
MIX “c1
¼
ar”
It is essential to provide a means of switching the
mixer on and off using the switch which controls the
aileron / landing fl ap function (see previous page), to
ensure that this mixer only has any effect when the
aileron / landing fl ap function is activated. The opti-
mum value has to be found by test-fl ying.
And fi nally a few words on the …
“FAIL-SAFE settings”
We strongly recommend that you make use of the safety
potential of this option by at least setting the throttle
position (glow-powered models) to idle, or the electric
motor to stop, if a fail-safe event should be triggered.
This simple precaution ensures that the model is much
less likely to cause havoc and cause property damage
or personal injury.
In the receiver’s default state the servos remain in their
last valid position (“hold mode”) when interference
occurs. However, you can program any individual servo
output of your receiver to either “fail-safe position” or
“hold”, as described on page 28 and in the instructions
supplied with the receiver. You can also defi ne the length
of time ( 1 … max. 5 seconds) after which the fail-safe
Summary of Contents for mx-16 ifs
Page 1: ...mx 16 Programming Manual mx 16iFS 1 gb 3D CYLINDER ROTARY SELECT INTELLIGENT FREQUENCY SELECT...
Page 15: ...15 For your notes...
Page 31: ...31 For your notes...
Page 35: ...35 For your notes...
Page 39: ...39 For your notes...
Page 55: ...55 For your notes...
Page 65: ...65 For your notes...
Page 77: ...77 For your notes...
Page 104: ...104 For your notes...
Page 111: ...111 For your notes...
Page 128: ...128 For your notes 128...
Page 129: ...129 For your notes 129...
Page 130: ...130 For your notes...