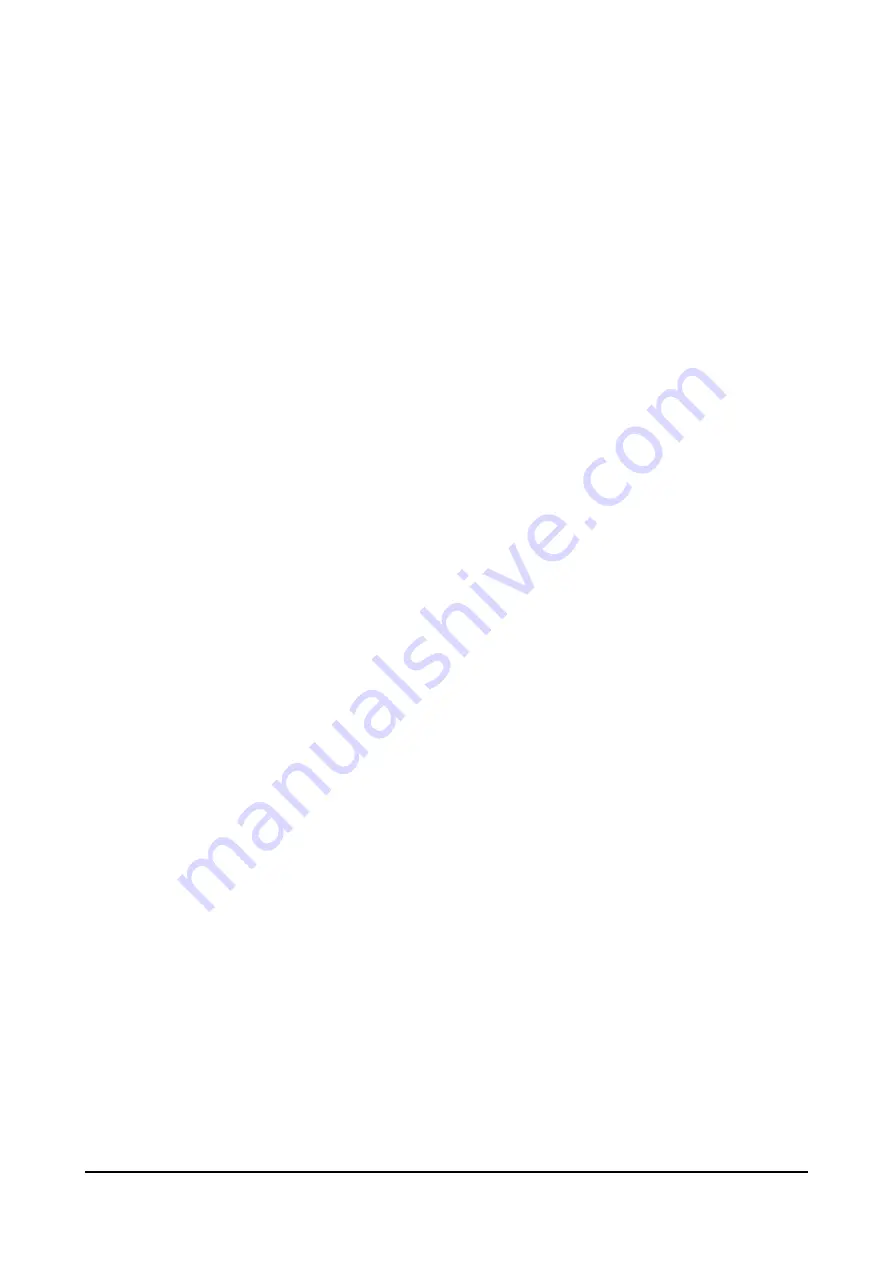
ADV200-HC Manual
Page 32 of 55
At system Start, the standard procedure to check exceeding of speed reference and torque thresholds is
run on each drive. When all monitors are active (thresholds exceeded), the block sends the command to
open all of the brakes.
At Stop, each drive independently manages brake closing by the standard method.
Manages the stopping of all shafts if the limit switch (HW or SW) trips on a single shaft configured as
Follower and allows its operation only in the opposite direction.
Manages the disabling of drives. If a drive is disabled for any reason during function in Follower, the block
commands closing of all brakes and then disabling of drives.
Manages any shaft errors by stopping the entire system.
Manages a common reset of all drives. The “Virtual Master” …-ELS-VM sends the reset command to all
drives connected to Fast Link. The command can also be sent locally to a single drive.
Follower Regulator Block
Active on all drives where the Follower command has been activated, including on the “Virtual Master”. It
regulates drive speed to follow the position reference indicated by the Virtual Master.
The Follower setting can be enabled as needed by the operator. Therefore, an On/Off switch will be placed on
the control panel to command the relative digital input of the drive.
In Follower mode, the drive no longer accepts movement commands configured locally, but, via the Follower
Regulator block, repeats the commands and speed reference received from the “Virtual Master”.
The block receives the position and speed reference from the Virtual Master, the position is compared to the
position generated by the encoder, then an error is generated that consequently changes the speed reference.
The position error is managed by a PI regulator with limitation of output value.
There is a maximum threshold of the position error beyond which you can activate a Warning or an Alarm and
the related consequent activity.
The block manages the initial positioning function, which allows each shaft to individually align with its ELS
align pos reference.
Even if a procedure to identify the travel was initially executed, the current position of the shaft will always be
calculated.
So that the ELS function may operate correctly, during commissioning you have to run a position recognition
procedure for each shaft. To do this, use the same function and parameters provided for Anti sway control for
the Hoist shaft and for Low Speed Zone control (SW limit switch) for the Trolley and Gantry.
Typical connection diagrams for -ELS-VM (Virtual Master) and -ELS (slave) configuration
The following is an example of a typical configuration of the -
ELS-VM
(Virtual Master) drive with EXP-IO-
D6A4R1-ADV expansion card (optional), encoder (required) and EXP
‐
FL
‐
XCAN
‐
ADV card (required).
Per l’installazione e la parametrizzazione delle schede si faccia riferimento al manuale dedicato.
See the specific manual for information on installing and parameterizing the cards.
This configuration lets you connect a joystick/button panel for movement commands, brake/feedback
management, limit switch sensors, alarms reset button, “ELS src” and “ELS align” selector.
Digital input signals are set on the HOIST&CRANE / DIGITAL INPUTS menu.
Digital output signals are set on the HOIST&CRANE / DIGITAL OUTPUTS menu.
!! ATTENTION !!
To enable drives in Electric Shaft, all Enable signals (including on drives set as NOT Follow) must be up.