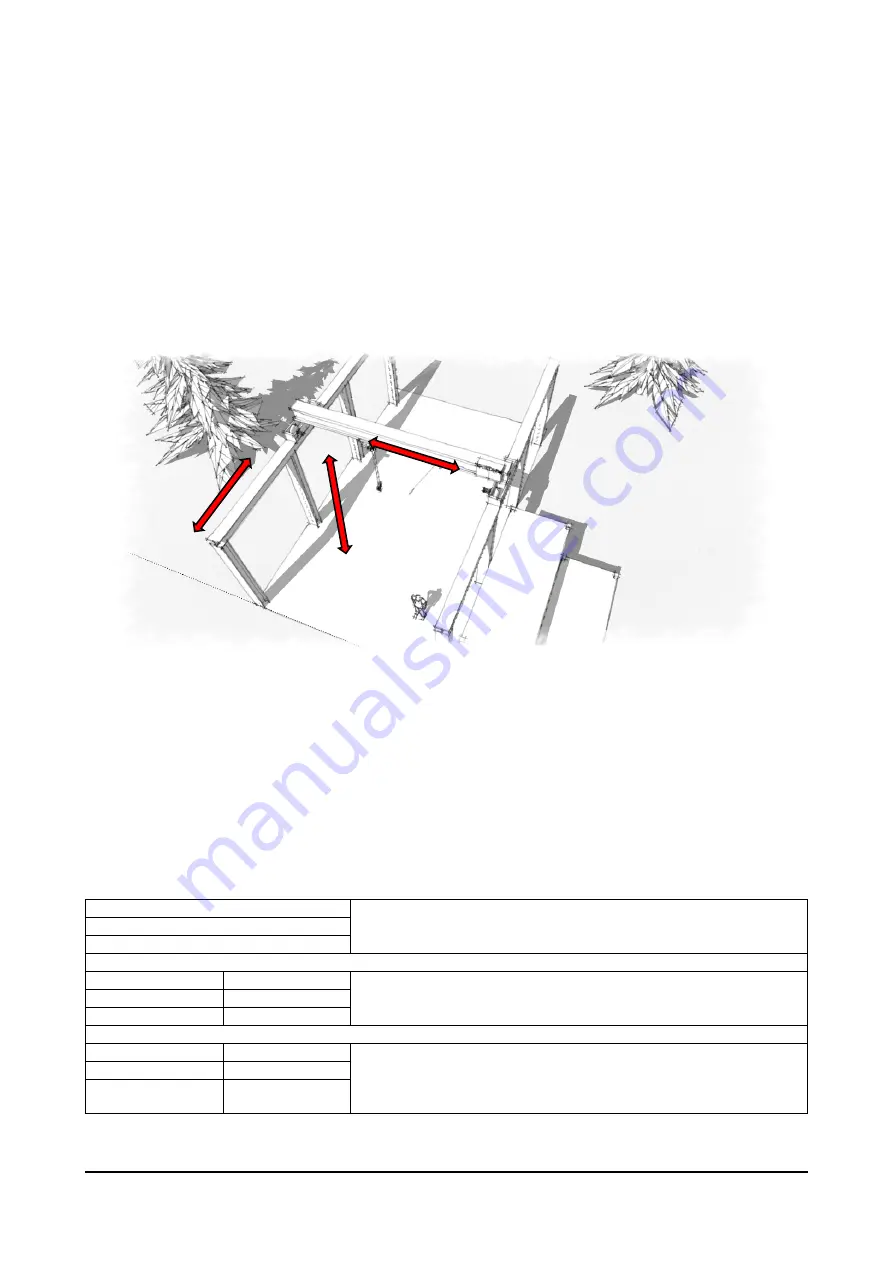
ADV200-HC Manual
Page 5 of 55
2
GENERAL DESCRIPTION
The application lets you control motors and manage commands and sensors for fixed applications used to
handle loads, such as:
•
rail mounted crane,
•
double cantilever crane,
•
gantry cranes,
•
overhead cranes,
•
shipyard cranes,
•
oil platform cranes,
•
container handling cranes,
•
steel mill cranes,
Typical structure of a load handling system:
A solid structure supports the trolley and its support beam, which moves forward and reverse on parallel
rails. The trolley moves the lift equipment to the left and right.
.
Drive connected to electric motors supply motion: Gantry (forward), Trolley (translation) and Hoist.
HOIST&CRANE software applied to every drive of each mechanical shaft lets you control and set its speed as
well as manage all of its main components (joystick, brake, and limit switch) without having to use an external
PLC.
You can control and run multiple synchronized motors by using the Electric Shaft or Helper functions. The
drives communicate with each other by means of these functions, coordinating system movements and
management. The type is configured with the &C SERVICE\Movement type IPA11002 parameter, and
includes:
Hoist
Drives used individually.
Gantry
Trolley
Hoist-ELS-VM
Hoist-ELS
Drives connected via FastLink.
In electric shaft, the movement of drives is controlled in position.
See ELS chapter for more information.
Gantry-ELS-VM
Gantry-ELS
Trolley -ELS-VM
Trolley-ELS
Hoist-HL-M
Hoist-HL-S
Drives connected via FastLink.
In Helper(HL) the slave(S) drive follows the torque reference
generated by master(M) drive.
See HELPER chapter for more information.
Gantry-HL-M
Gantry-HL-S
Trolley-HL-M
Trolley-HL-S
Hoist
Trolley
Gantry