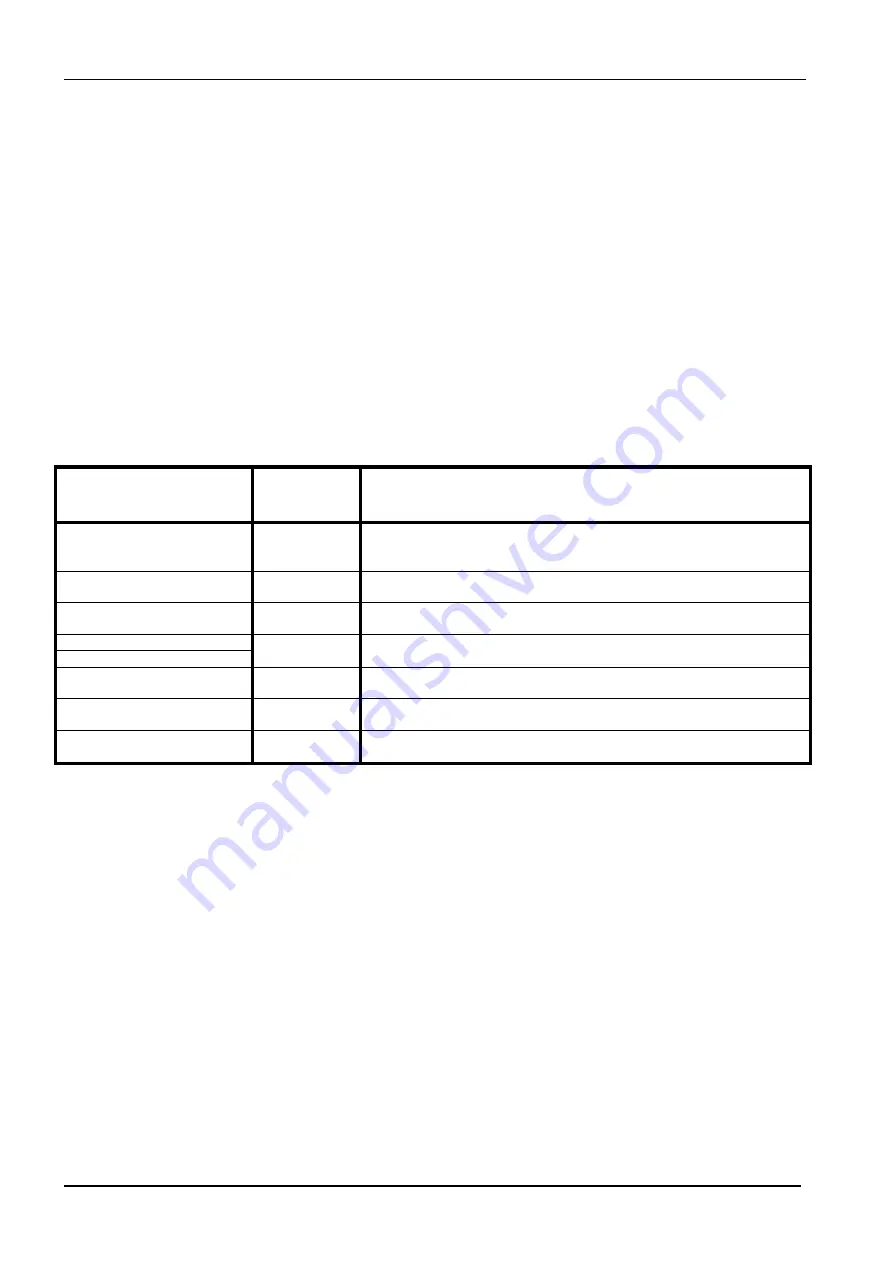
Split system (Single phase and 3-phase type)
112
Maintenance
Document
1544-1
Procedure for compressor installation
Reverse procedure to removing the compressor.
Precautions for installation of compressor.
1 When brazing, do not apply the flame on the terminal.
2 When brazing, be sure to replace the air in the pipe with nitrogen gas to prevent forming oxidization
scale.
6.3 Precautions for exchange of refrigerant-cycle-parts
(1) During exchange the following parts shall be protected by wet rag and not make the allowable temperature or more.
(2) Remove the heat insulation when there is the heat insulation near the welding place. Move and cool it whan its
detaching is difficult.
(3) Cool the parts when there are parts where heat might be transmilled besides the replacement part.
(4) Interrupt the flame with the fire-retardant board when the flame seems to hit the following parts directly.
(5) Do no allow moisture or debris to get inside refrigerant pipes during work.
(6) When brazing, be sure to replace the air in the pipe with nitrogen gas to prevent forming oxidization scale.
Part name
Allowable
temperature
Precautions in work
EXPANSION VALVE (MAIN)
120°C
Remove the coil before brazing.
And install the coil after brazing.
Detaching necessity sensor.
EXPANSION VALVE
(INJECTION)
120°C
Remove the coil before brazing.
And install the coil after brazing
4 WAY VALVE
120°C
Remove the suction temp. sensor before brazing.
And install the suction temp. sensor after brazing.
3 WAY VALVE (GAS)
3 WAY VALVE (LIQUID)
100°C
UNION JOINT
100°C
Remove the pressure sensor before brazing.
And install the pressure sensor after brazing.
PRESSURE SENSOR
100°C
Tighten the flare part gripping it. (Tightening torque : 12+-1.5N.m)
Do the static electricity measures.
SOLENOID VALVE
200°C
Remove the coil before brazing.
And install the coil after brazing.
Fujitsu General (Euro) GmbH
Werftstrasse 20
40549 Düsseldorf - Germany
Summary of Contents for Waterstage WO G112LCT Series
Page 2: ......