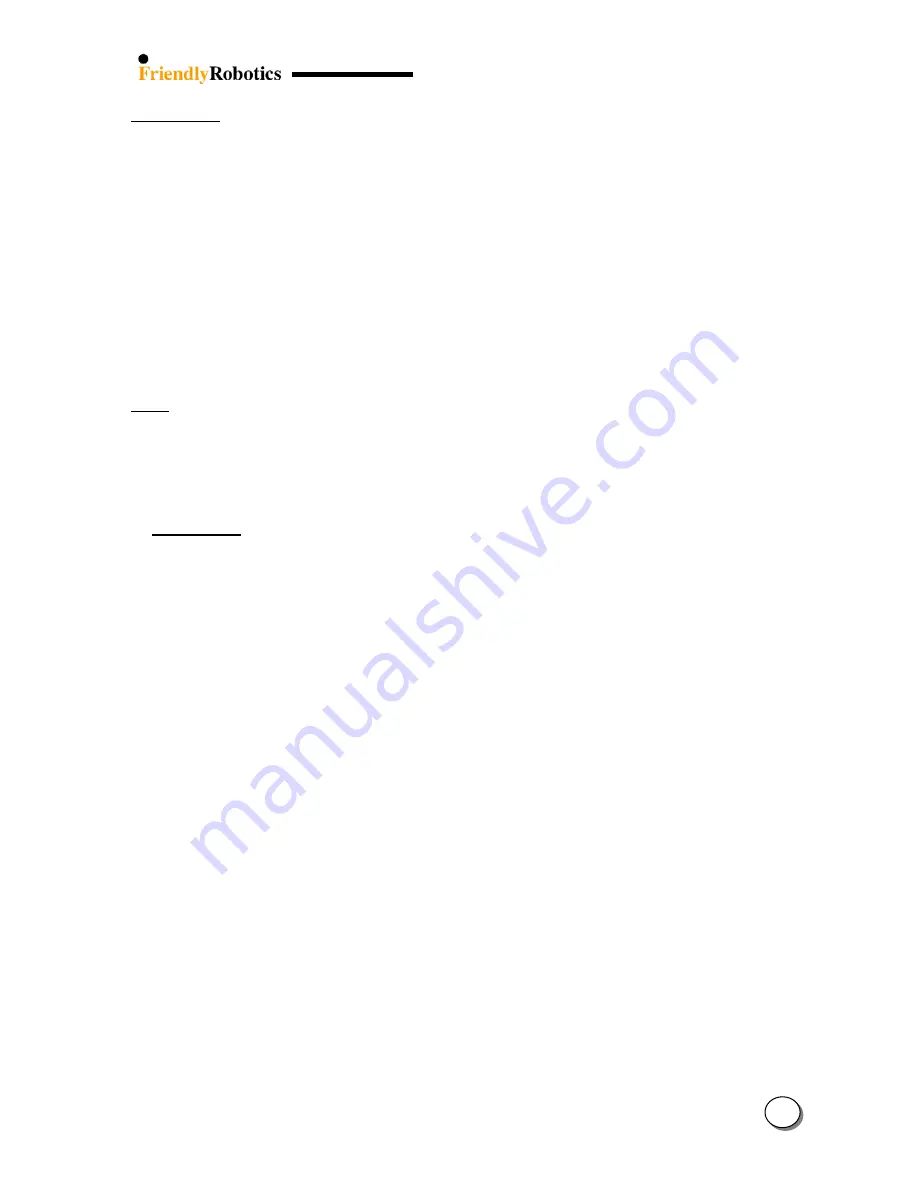
2
15
Poor Storage – poor storage counter indicates how many times the mower was put into operation
where the power pack capacity was less than 80% of fully charged. This essentially indicates how
often the mower was used prior to the power pack being fully re-charged, where the count will not
start until there is a 20% capacity loss from fully charged. The 20% criteria is important, as many
people will use the mower in several smaller areas in addition to the main area. A smaller area
will discharge the power pack, but not to the 20% level, so we do not want to count such
operations. A high count here, greater than 3 or 4 indicates that the user is not fully re-charging
the power pack. If a customer claims that that’s his only solution to mow the entire lawn, it is
recommended that they purchase an additional power pack and an external charger. Lastly, if the
voltage of a power pack, when inserted, is less than 90% of the last measured voltage, that
indicates that the power pack has not been fully charged at the end of the previous season, which
is critical for good service life (winter/storage charging instructions are given in the operating &
safety manual).
Reset – allows resetting all listed battery parameters back to zero when a new power pack has
been put in service or possibly if a service repair was done, which may have affected the counters.
6.3 SETTINGS
6.3.1 Docking Options
6.3.1.1
Edge to Dock
Enable the mower to complete the edge operation from the Docking Station back to the
Docking Station without any condition, otherwise there are few events that may cause the
mower to leave the edge, such as distance limit or number of turns to the left.
6.3.1.2 Docking search vlt.
Option to increase the ‘Searching dock’ threshold voltage (22.5 and 23.0) in case, which
the mower doesn't succeed to drive back to the Charging Station because of low battery
voltage.
6.3.1.3 Dock bumper
Changing this option to 'off' will change the bumper behavior so it will make bypass in
every bumper event during 'Edge' mode.
6.3.1.4 Islands
Setting this option to ‘off’ allow the mower to acquire the Perimeter Wire immediately as
starting to search for the Charging Station with no need to converge to the end of the lawn.
6.3.2 Small Wheels
In some markets there are two types of wheels for different Robomow models. There are knobby
wheels (as in all US models) and there are smaller diameter wheels without treads. If this setting
is inadvertently selected, the mower will not navigate properly and will likely not drive in straight
lines.
It is important to have the setting right according to the type of wheels.
Summary of Contents for robomower RL1000
Page 11: ...1 8 1 2 2 Base top view 41 42 28 25 44 21 27 40 43 17 22 10 5 18 20 8...
Page 12: ...1 9 1 2 3 Cover top view 45 3 46 2 4 105 7 10 9 6 47 9...
Page 13: ...1 2 4 Charging Station 10 53 30 48 29 31 54 122 123 29 32 48 49 50 127 51 52 1 10...
Page 14: ...1 2 5 Gear Case 5 5 42 21 44 57 56 58 22 23 59 61 60 1 11...
Page 17: ...1 14 1 2 8 Perimeter Switch 73 74 75 76 77 1 2 9 Bumpers 78 10 79 5...
Page 18: ...15 1 2 10 Front Wheel 83 82 81 80 11 1...
Page 25: ...1 5 Wiring layout 1 22 1 5 1 Robomow schematic wiring diagram 109...