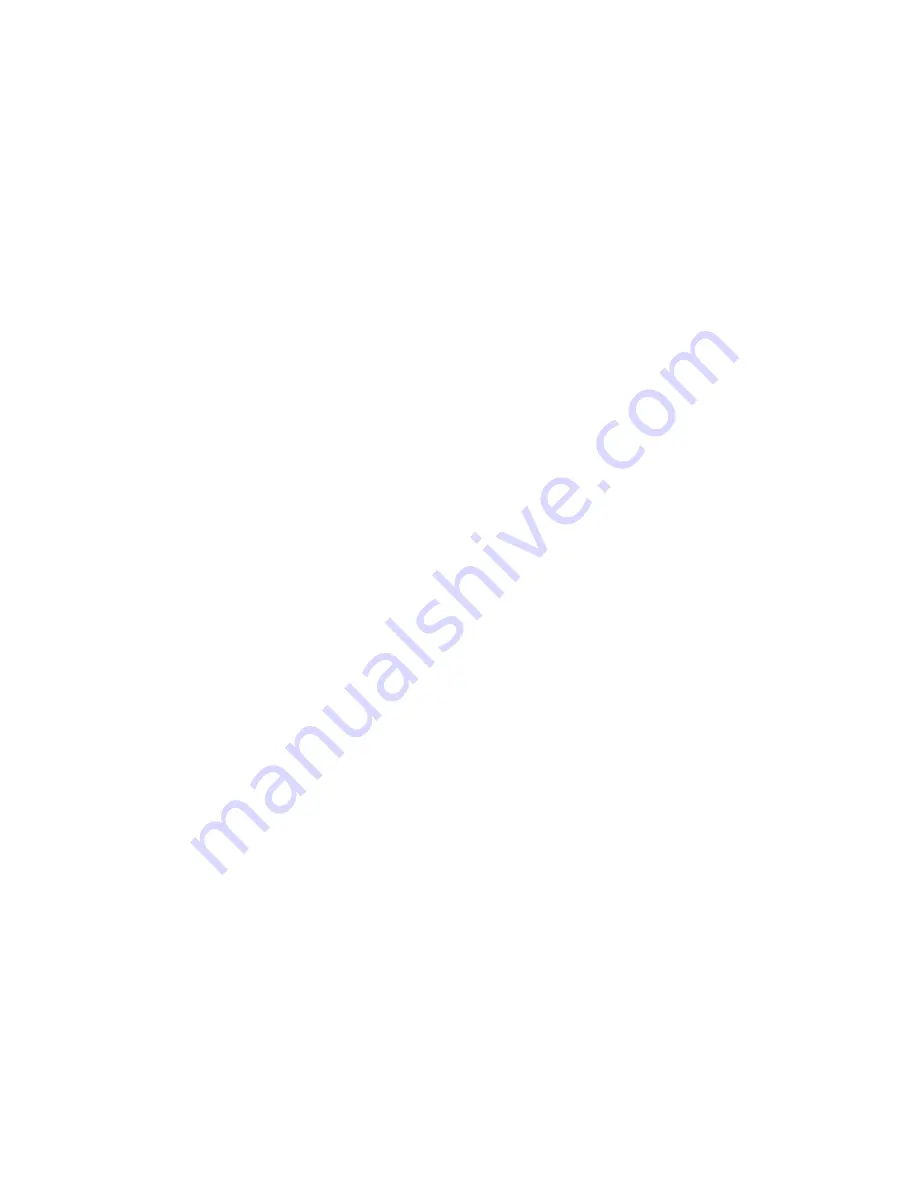
Page
60
/
62
9.5 Inspections
9.5.1 General recommendations
• After each shift change, clean the machine (mainly from paper dust)
• Pay attention to the cleanliness of contacts of control elements (contactors, connectors)
• Check the screw connections of the cutter elements and if necessary, tighten the screws.
9.5.2 Checking hydraulic hoses
Check regularly that the hose is not damaged or frayed, and check the oil level.
Recommended test criteria for hydraulic hoses:
• Damage to the inner layer (scratches, cuts, cracks)
• Hose deformation
• Leaks (on the surface of the hose, fixing)
The condition of the hoses should be checked at least every 12 months.
Replacement of hoses is recommended at least every 6 years.
9.5.3 Knife sharpening
The quality and accuracy of cutting depends primarily on the sharpness of the knife and the
correct angle of its blade.
9.5.3.1 Features of a blunt knife
• rough and uneven surface of the cut ream
• ticking the edge of the cut material
• inaccurate cutting
• increased formation of paper dust.