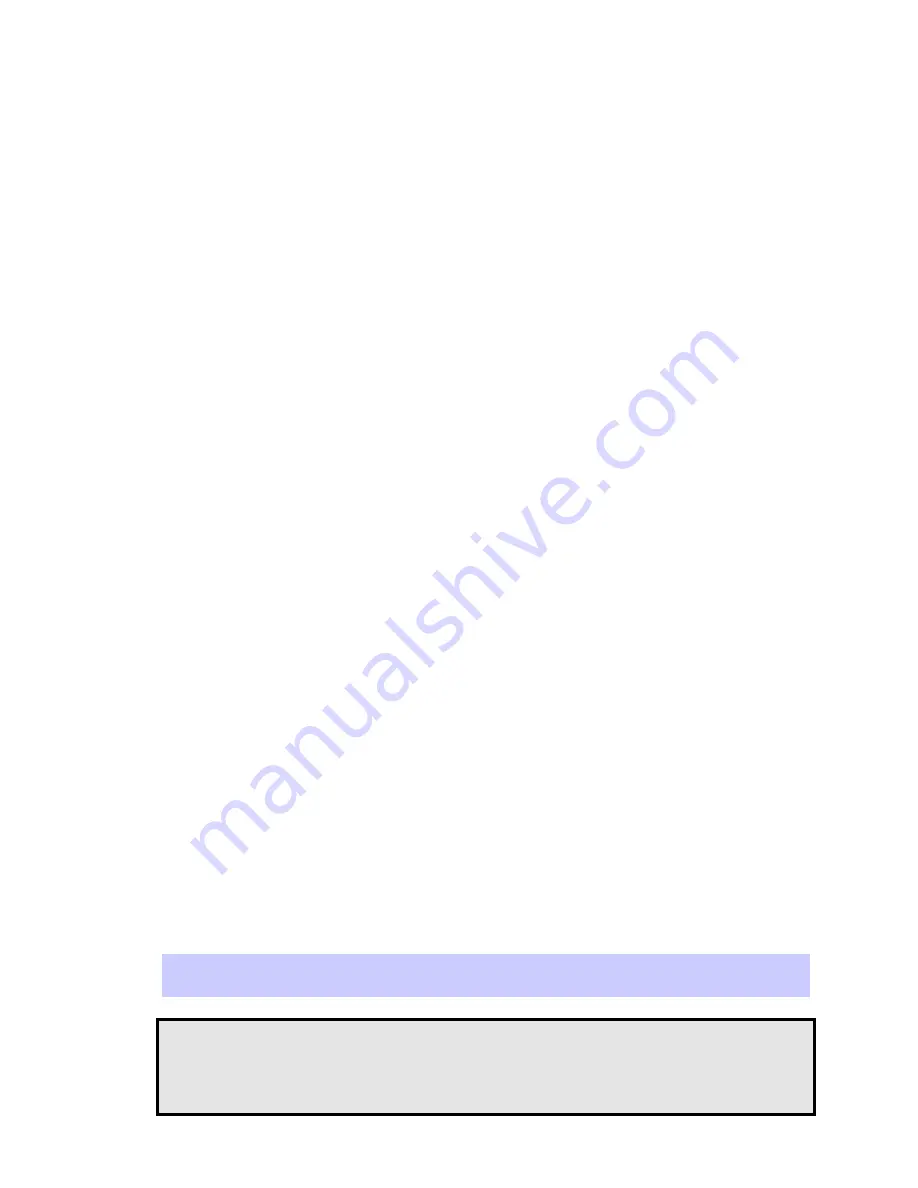
Page 39
5.4.2 SEAM WELDING MODE - [
=!0!
]
To program the control for SEAM OPERATION:
1. Put the control in PROGRAM MODE.
2. Use SELECT to find [
01
].
3. Use the SCHEDULE push-buttons to scroll through extended functions and find [
=0
].
4. Enter a value for [
=0
] of [
"#
] using the DATA push-buttons.
5. Press the ENTER push-button.
Entering [
=0
] = [
""
] into the DATA Display puts the control back in Spot Mode.
A seam welder can be operated in one of two modes: INTERMITTENT and
CONTINUOUS. In either SEAM mode, current starts synchronously upon initiation,
remains on as long the pilot switch is closed, and stops synchronously when the pilot switch
is opened.
INTERMITTENT SEAM MODE
INTERMITTENT SEAM welding is the mode of operation in which weld current flows only
for the duration of the WELD/HEAT time setting and is off during the COOL. The
intermittent operation continues as long as the initiation switch remains closed. When the
initiation is opened the sequence ends. WELD/HEAT time is the time duration in which
weld current flows in a single impulse, and must be programmed for at least 1 cycle. COOL
time is the time between subsequent WELD/HEAT impulses.
If the initiation is opened during a WELD/HEAT Time, the impulses end immediately and
advances to HOLD Time. If the initiation is opened during a COOL time, the sequence ends
at the end of the programmed COOL Time and advances to HOLD Time.
CONTINUOUS SEAM MODE
CONTINUOUS SEAM welding is the mode in which current flows continuously as long as
the pilot switch remains closed. COOL Time is programmed to 00, and WELD must be
programmed for at least 1 cycle, for CONTINUOUS SEAM mode.
Notice that in either seam mode, initiations can be changed during the welding of a seam to
provide different heat-cool pattern and/or a different percent current. This feature is useful
to compensate for possible machine power factor changes which may occur as a seam is
being welded. As an example a seam may be started by closing FS3 to GND, then closing
FS7 to GND and finally closing FS11 to ground as the seam progresses. The highest number
closed to ground determines which schedule will be active. Schedule changes made during
a heat or cool time become effective immediately. When in seam mode the FS3 initiation
will use the dialed schedule, FS7 will use schedule 10, and FS11 will use schedule 20.
NOTE:
Some SEAM features may be desired when the control is used for resistance brazing
or soldering applications. See Section 5.4.8 on BEAT operation.
WARNING
:
Care MUST be taken to minimize the over heating of internal components when in the
SEAM Mode. Correct transformer power dissipation (sizing) and welding control
capability are essential to avoid component overheating.
StockCheck.com
Summary of Contents for EN1000 series
Page 2: ...S t o c k C h e c k c o m ...
Page 19: ...Page 17 Figure 3 6 External SCR Contactor connection S t o c k C h e c k c o m ...
Page 120: ...Page 118 11 3 TROUBLESHOOTING GUIDE S t o c k C h e c k c o m ...
Page 121: ...Page 119 S t o c k C h e c k c o m ...
Page 122: ...Page 120 11 4 BLOCK DIAGRAM S t o c k C h e c k c o m ...