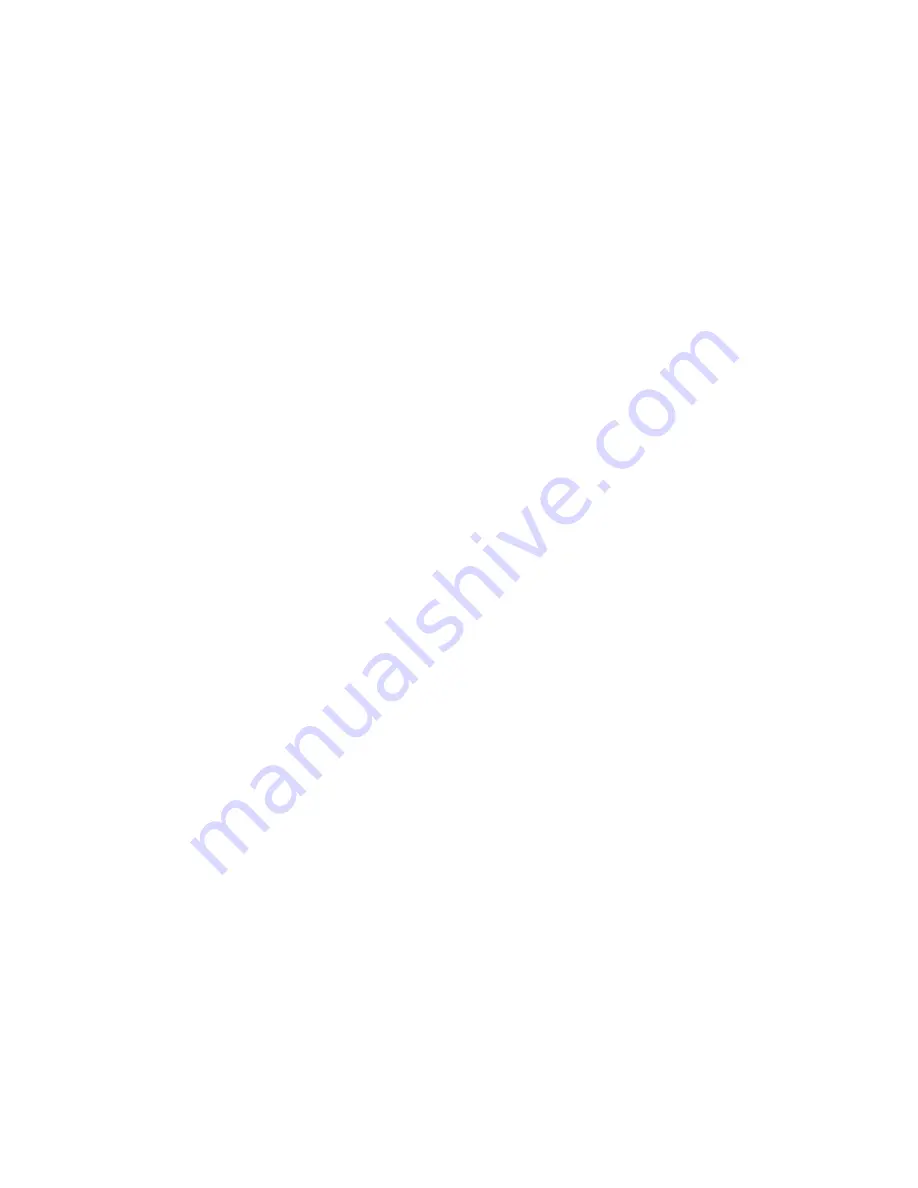
Page 52
[
;!:!
] = [
$%
]
- Used with RS232 or RS485 Option - EN1001
ONLY
.
This Process Output will prepare Error Code and Current to be sent to master on ENBUS
or to Serial Printer:
Error message
0!X!3O
if current was above maximum limit and current value in [%]
or [kA]. Error message
0!X!7U
if current was below minimum limit and current
value in [%] or [kA].
[
;!:!
] = [
$&
]
- EN1001
ONLY
CURRENT OUTSIDE OF HI or LO LIMIT
PROCESS OUTPUT. This Process
Output uses Valve 1 to indicate HIGH current errors, Valve 2 for LOW current errors,
and Valve 3 to indicate end of sequence, display measured current on DATA display
after end of sequence and display H.i. or L.o. if measured current is out of HI/LO
window.
[
;!:!
] = [
$'
]
- EN1001
ONLY
INDICATE CURRENT OUTSIDE OF LIMIT and DISPLAY CURRENT
PROCESS OUTPUT. This Process Output uses Valve 1 to indicate HIGH current
errors, Valve 2 for LOW current errors, and Valve 3 to indicate end of sequence, and will
display measured current on DATA display after end of sequence.
[
;!:!
] =
[
$(
]
- EN1001
ONLY
CURRENT OUTSIDE OF LIMIT
Flash HI or LO, Stop Sequence, and Hold Part
PROCESS OUTPUT. This Process Output uses Valve 3 to indicate High or Low current
errors and stop the sequence until the error is cleared. Valve 1, if programmed, may be
used to hold the part after the weld. Refer to Application Note 700187.
[
;!:!
] = [
$)
]
- EN1001
ONLY
CURRENT OUTSIDE OF LIMIT FLASH HI or LO and Stop the Sequence
PROCESS OUTPUT - This Process Output is the same as [
;!:!
]=[ 14 ], except that in
this case the Valve 3 output will be
ON
for 0.5 second to indicate High or Low current.
[
;!:!
] = [
$*
]
- EN1001
ONLY
EOS INDICATION IF
CURRENT
WITHIN
THE LIMITS AND CONTROL
IN
WELD MODE
PROCESS OUTPUT. This Process Output uses Valve 3 at the End of
Sequence to indicate that Current was
within
the HI and LO limits, and if Control was
in WELD mode with closed NW1-GND input on TS1. Valve 3 will be ON for 0.5
seconds. In non constant current mode, this Process Output will turn Valve 3 ON for 0.5
seconds after EOS only if Control was in WELD mode and closed NW1-GND input.
[
;!:!
] = [
%"
]
- Valve 3 turns ON whenever Error 36, i.e. IPSC or IPS error, occurs.
When the control includes the IPSC or IPS option, the Control may be programmed to
indicate whenever any pressure error is detected.
[
;!:!
] = [
%#
]
- Valve 3 ON if Error 36, IPSC or IPS error, occurs
after
the weld.
When the Control includes the IPSC or IPS option, and while using this Process Output
the control reads the Sensor output
after
the weld portion of the weld sequence and turns
the Valve 3 on if the trigger value for pressure/force/current is not reached. The trigger
values must be programmed within a valid range.
StockCheck.com
Summary of Contents for EN1000 series
Page 2: ...S t o c k C h e c k c o m ...
Page 19: ...Page 17 Figure 3 6 External SCR Contactor connection S t o c k C h e c k c o m ...
Page 120: ...Page 118 11 3 TROUBLESHOOTING GUIDE S t o c k C h e c k c o m ...
Page 121: ...Page 119 S t o c k C h e c k c o m ...
Page 122: ...Page 120 11 4 BLOCK DIAGRAM S t o c k C h e c k c o m ...