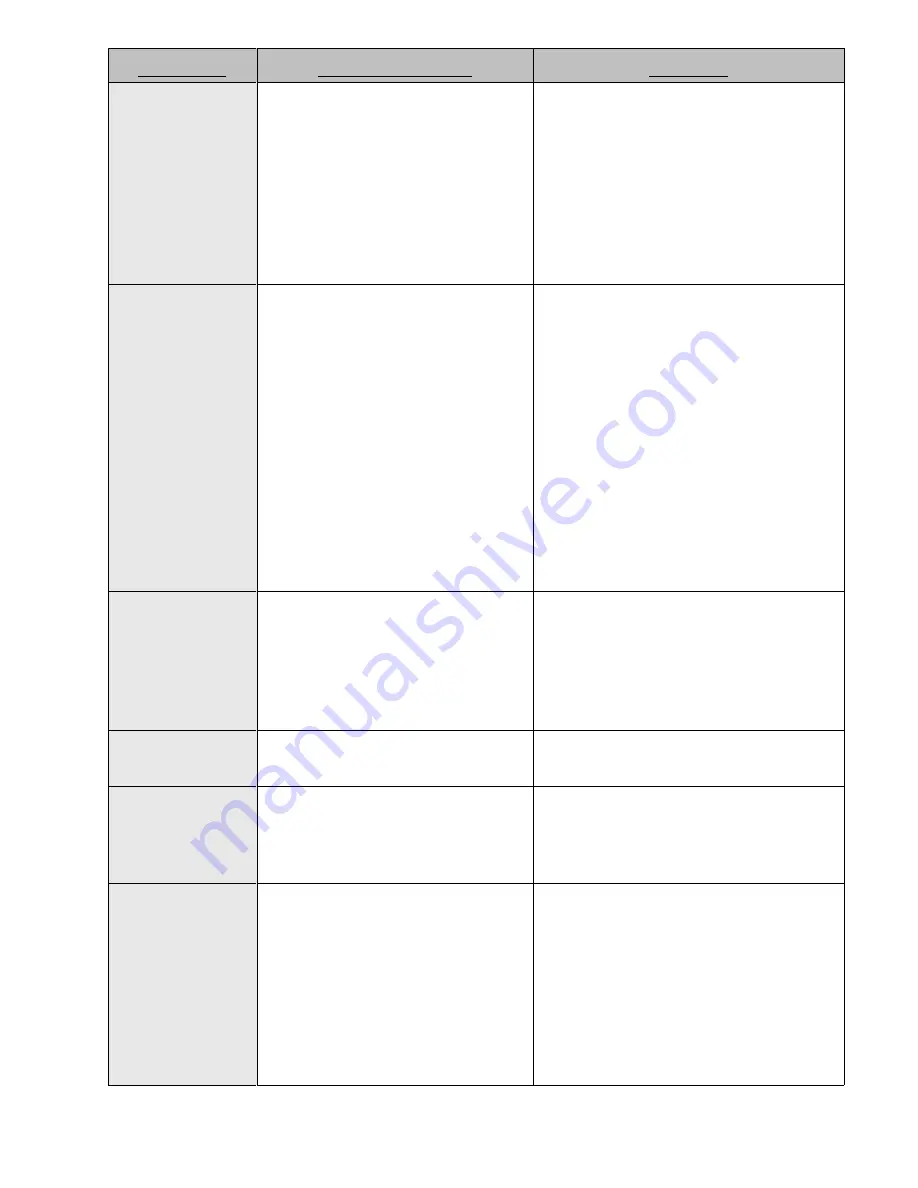
Page 117
TROUBLE
POSSIBLE CAUSE
REMEDY
Control initiates
and sequences
properly, but
solenoid valve
chatters.
1. Solenoid valve coil.
2. Defective Control/Display PCB.
3. Defective Terminal Strip/Firing
Board.
1.a) Check that valve supply voltage is
not varying below tolerance, -15%.
1.b) Check if valve coil is proper voltage.
1.c) Insufficient air pressure.
1.d) Loose connections in valve wiring.
2. Replace board with another board
stamped with the same A/N.
3. Replace board. See wiring diagram for
correct Assembly Number.
Control
sequences but
will not weld.
1. External Weld/No-Weld Switch,
or Weld/No-Weld Switch on front
panel of control.
2. Welding transformer not
connected.
3. Welding transformer secondary
open.
4. Defective Terminal Strip/Firing
PCB.
5. Defective Control/Display PCB.
6. Excessive Ripple in secondary.
1.a) Check both for proper operation
and/or loose wires on NW1 & GND.
1.b) If no external Weld/No-Weld Switch
is used, put jumper across NW1 & GND.
2. Connect H1 and H2 to Lugs in the
control.
3. Check corroded or open connections.
Be sure welding electrodes close on
work.
4. Replace board. See wiring diagram for
correct Assembly Number.
5. Replace board with another board
stamped with the same A/N.
6. Check for missing phase.
Weld too cool.
1. Line voltage drop.
2. Excessive pressure at electrodes.
3. Weld Count too short.
4. Excessive tip "mushrooming".
1. KVA demand for welding transformer
too high for input power line. Check line
voltage.
2. Check air system regulator.
3. Increase Weld Count duration.
4. Properly dress tips.
Weld too small.
1. Percent current too low.
2. Electrode face too large.
1. Increase value of Percent Current.
2. Select correct electrode face diameter.
"HOT" Welds
1. Insufficient air pressure.
2. Weld Count set too high.
3. Percent Current set too high.
4. Electrode diameter too small.
1. Check air supply and accessories.
2. Reduce Weld Count duration.
3. Decrease value of Percent Current.
4. Dress or replace tip with proper size.
Inconsistent
Welds
1. Varying air pressure.
2. Work not square with electrodes.
3. Poor part fit-up.
4. Dirty material to be welded.
5. Loose connection.
1. Check air supply and accessories.
2. Check welding fixtures set-up or
electrode alignment.
3. Check parts for proper fit-up.
4. Work should be free from excessive
dirt, paint and oxides.
5. Check for all terminals and/or lugs
connections inside the Cabinet.
StockCheck.com
Summary of Contents for EN1000 series
Page 2: ...S t o c k C h e c k c o m ...
Page 19: ...Page 17 Figure 3 6 External SCR Contactor connection S t o c k C h e c k c o m ...
Page 120: ...Page 118 11 3 TROUBLESHOOTING GUIDE S t o c k C h e c k c o m ...
Page 121: ...Page 119 S t o c k C h e c k c o m ...
Page 122: ...Page 120 11 4 BLOCK DIAGRAM S t o c k C h e c k c o m ...