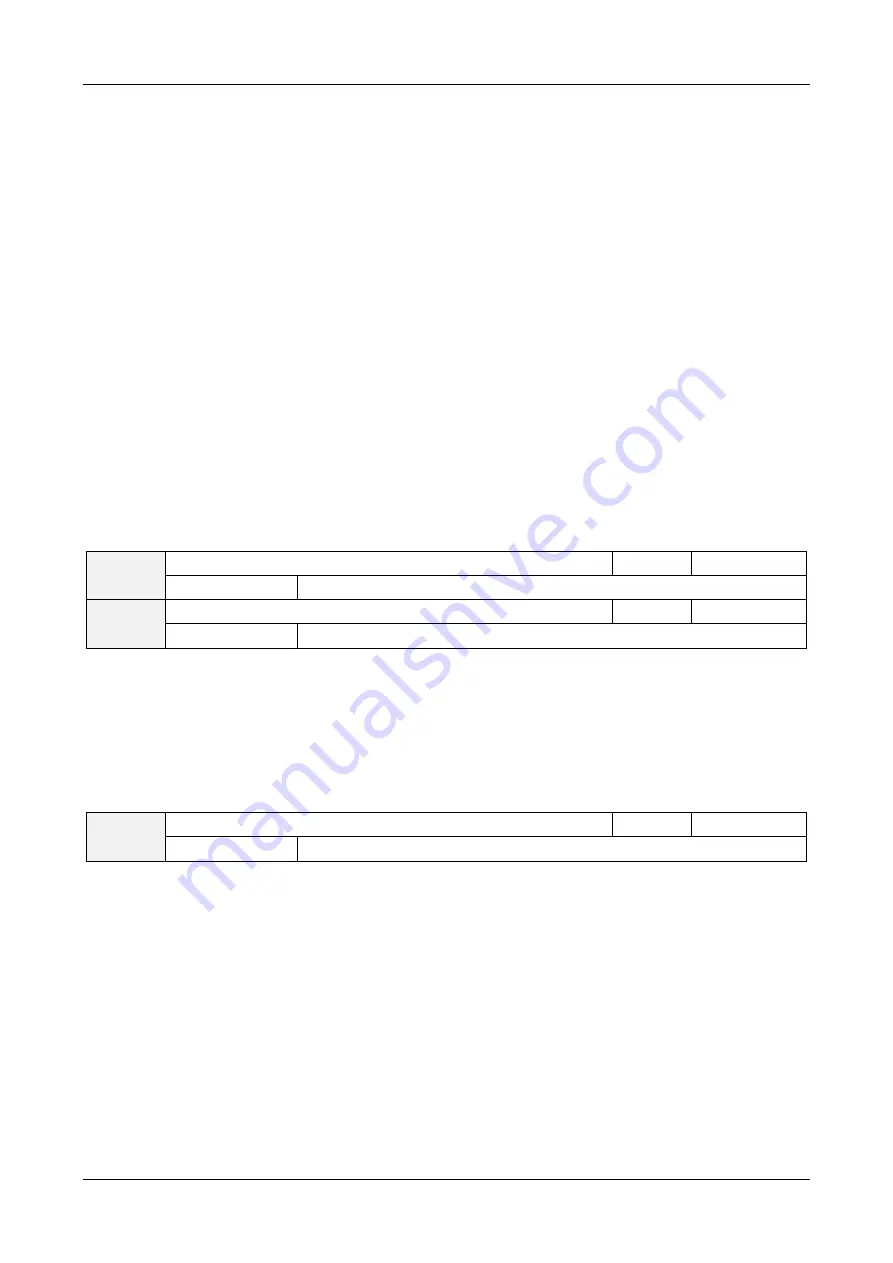
5.Description of Function Codes
EM15 User's Manual
94
0: Digital setting (d1-26)
The target torque directly uses the value set in d1-26.
1:AI1
2:AI2
3:AI3
The target torque is decided by analog input. The EM15 control board provides three AI terminals (AI1, AI2,AI3).
AI1 and AI2 is 0V~10 V voltage input or 0mA~20mA current input decided by jumper on the control board, and
AI3 is -10 V ~ +10 V voltage input.
For the details of AI Curve setting, please refer to the description of analog input parameters.
When AI is used as frequency setting source, the corresponding value 100% of voltage/ current input corresponds
to the value of d1-26.
4: Pulse setting (HDI)
The target torque is set by HDI (high-speed pulse). The pulse setting signal specification is 9V~30 V (voltage
range) and 0 kHz~100 kHz (frequency range). The pulse can only be input via HDI. The relationship (which is a
two-point line) between HDI input pulse frequency and the corresponding value is set in b5-00 ~ b5-03. The
corresponding value 100.0% of pulse input corresponds to the percentage of d1-26.
5: Communication setting
The target torque is set by means of communication.
d1-28
Forward maximum frequency in torque control
Default
50.00 Hz
Setting Range
0.00 Hz ~ maximum frequency(b0-13)
d1-29
Reverse maximum frequency in torque control
Default
50.00 Hz
Setting Range
0.00 Hz ~ maximum frequency(b0-13)
The two parameters are used to set the maximum frequency in forward or reverse rotation in torque control mode.
In torque control, if the load torque is smaller than the motor output torque, the motor's rotational speed will rise
continuously. To avoid runaway of the mechanical system, the motor maximum rotating speed must be limited in
torque control.
You can implement continuous change of the maximum frequency in torque control dynamically by controlling
the frequency upper limit.
d1-30
Acceleration time in torque control
Default
0.00s
Setting Range
0.00s~650.00s
In torque control, the difference between the motor output torque and the load torque determines the speed change
rate of the motor and load. The motor rotational speed may change quickly and this will result in noise or too large
mechanical stress. The setting of acceleration/deceleration time in torque control makes the motor rotational speed
change softly.
However, in applications requiring rapid torque response, set the acceleration/deceleration time in torque control
to 0.00s. For example, two frequency inverters are connected to drive the same load. To balance the load
allocation, set one frequency inverter as master in speed control and the other as slave in torque control. The slave
receives the master's output torque as the torque command and must follow the master rapidly. In this case, the
acceleration/deceleration time of the slave in torque control is set to 0.0s.
5.20 Group d2: Motor V/F Control Parameters
Group d2 is valid only for V/F control.