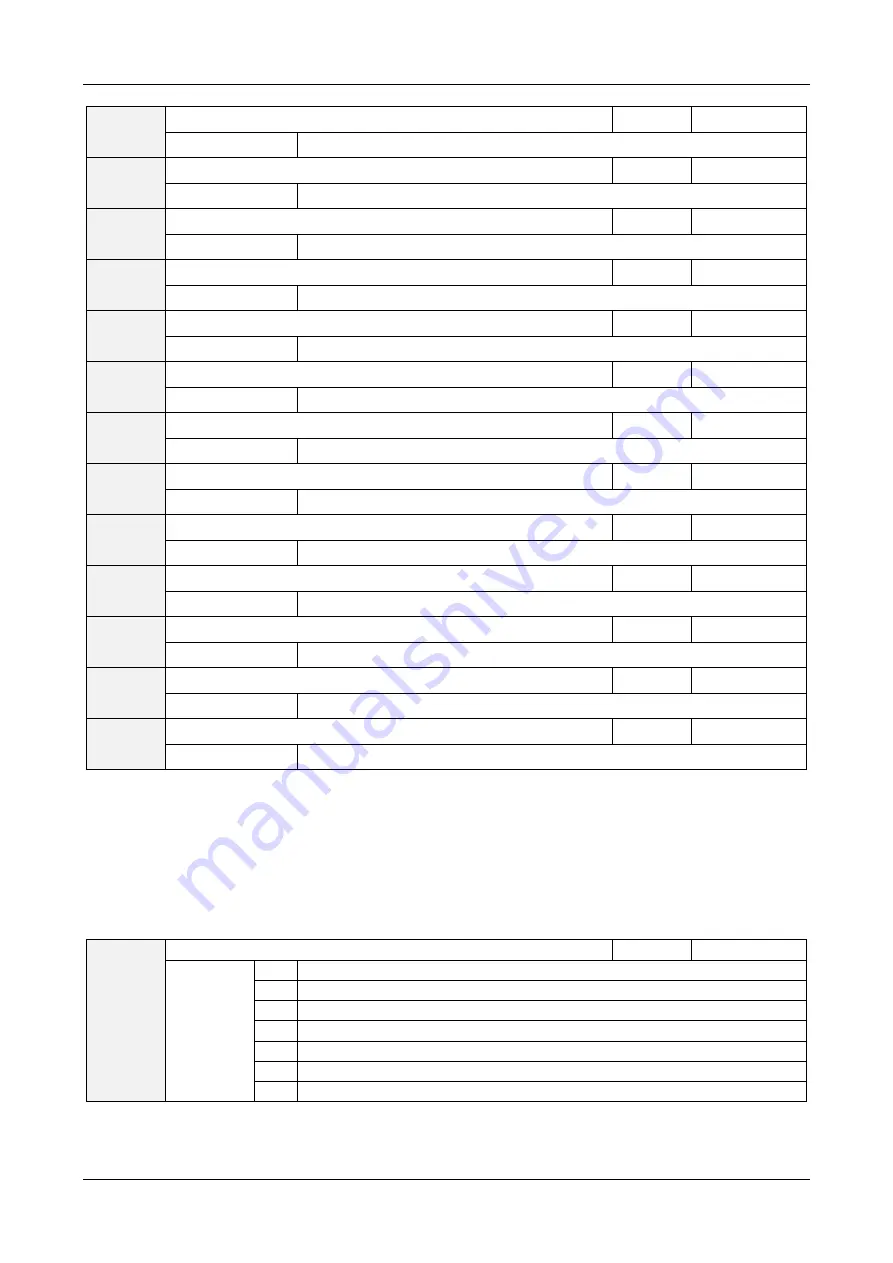
EM15 User’s Manual
5. Description of Function Codes
83
C1-03
Multi-function 3
Default
0.0%
Setting Range
-100.0%~100.0%
C1-04
Multi-function 4
Default
0.0%
Setting Range
-100.0%~100.0%
C1-05
Multi-function 5
Default
0.0%
Setting Range
-100.0%~100.0%
C1-06
Multi-function 6
Default
0.0%
Setting Range
-100.0%~100.0%
C1-07
Multi-function 7
Default
0.0%
Setting Range
-100.0%~100.0%
C1-08
Multi-function 8
Default
0.0%
Setting Range
-100.0%~100.0%
C1-09
Multi-function 9
Default
0.0%
Setting Range
-100.0%~100.0%
C1-10
Multi-function 10
Default
0.0%
Setting Range
-100.0%~100.0%
C1-11
Multi-function 11
Default
0.0%
Setting Range
-100.0%~100.0%
C1-12
Multi-function 12
Default
0.0%
Setting Range
-100.0%~100.0%
C1-13
Multi-function 13
Default
0.0%
Setting Range
-100.0%~100.0%
C1-14
Multi-function 14
Default
0.0%
Setting Range
-100.0%~100.0%
C1-15
Multi-function 15
Default
0.0%
Setting Range
-100.0%~100.0%
Multi-function can be the setting source of frequency, V/F separated voltage and process PID. The Multi-function is
relative value and ranges from -100.0% to 100.0%.
As frequency source, it is a percentage relative to the maximum frequency. As V/F separated voltage source, it is a
percentage relative to the rated motor voltage. As process PID setting source, it does not require conversion.
Multi-function can be switched over based on different states of DI terminals. For details, see the descriptions of
group b3.
C1-16
Multi-function 0 source
Default
0
Setting
Range
0
Set by C1-00
1
AI1
2
AI2
3
AI3
4
Pulse setting(HDI)
5
PID
6
Set by digital setting frequency (b0-12), modified via terminal UP/ DOWN
It determines the setting channel of multi-function 0. You can perform convenient switchover between the setting
channels. When multi-function or simple PLC is used as frequency source, the switchover between two frequency