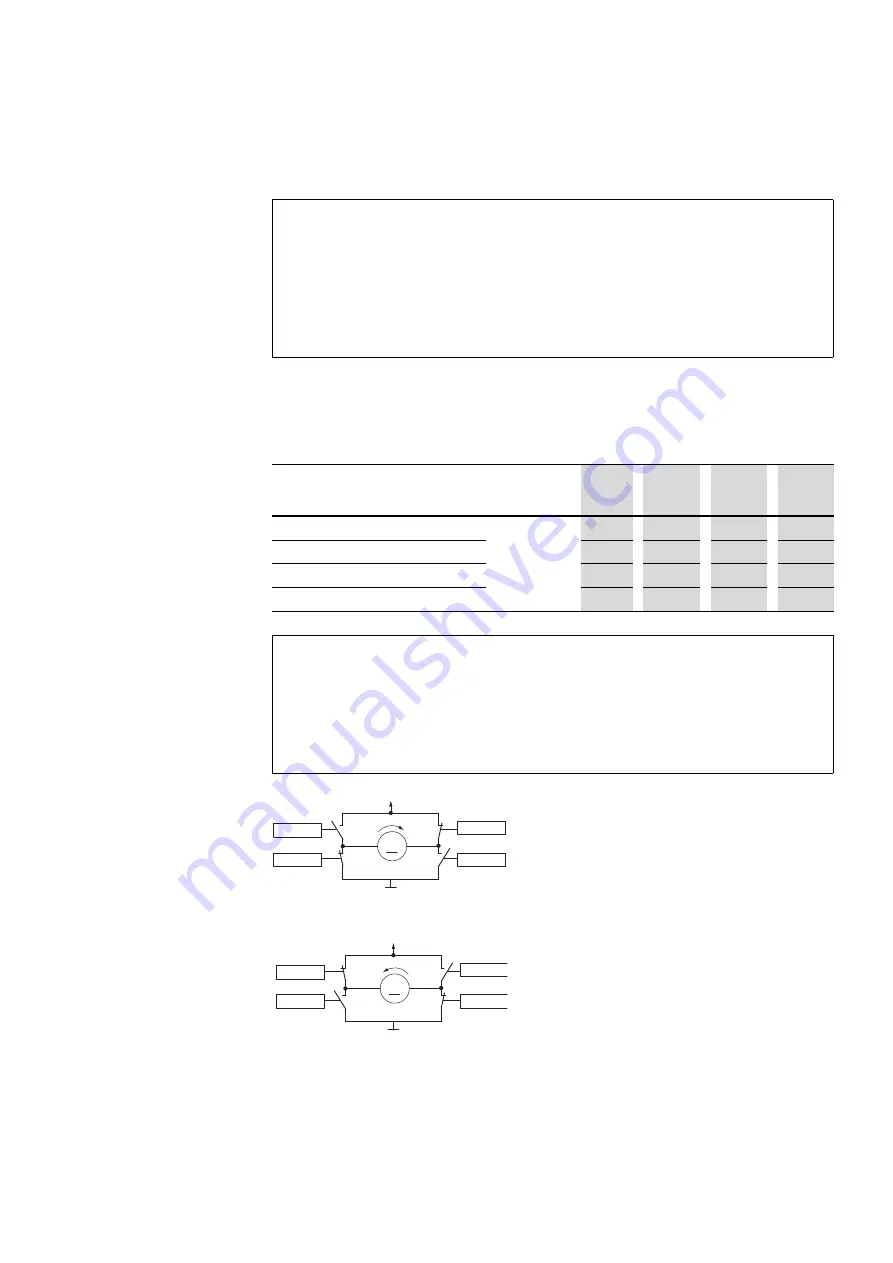
30 DC motor driver module XN-322-1DCD-B35
30.3 Wiring
XN300 slice modules
06/16 MN050002 EN
www.eaton.com
241
Defining the motor's operating direction
The motor's operating direction can be defined for each subsequence in
objects 0x20E0 – 0x20E3 using bits 12 – 15. A state of "1" means: switch
closed. These switches are implemented inside the device with the use of
transistors.
Figure 126:
Block diagram for a clockwise motor operating direction
Figure 127:
Block diagram for a counterclockwise motor operating direction
CAUTION
There should be no state changes in the motor's operating
direction within an output sequence.
In order to reduce motor overload and the mechanical load on
the motor, start by decelerating the motor's speed to "zero,"
then change the operating direction, and finally increase the
speed back to the setpoint.
Permitted switching combinations for
the sequence setting
Bit 12-15
Value
hex
Bit 15
Bit 14
Bit 13
Bit 12
Motor Off
0
hex
0
0
0
0
Operating direction right
6
hex
0
1
1
0
Operating direction left
9
hex
1
0
0
1
Motor armature short-circuit
C
hex
1
1
0
0
CAUTION
When changing the motor's operating direction, make sure to
keep the motor switched off for a minimum period of 5
μ
s by
using an armature short-circuit sequence. Otherwise, an imper-
missible I
2
dt energy flux may be produced, resulting in the
XN300 slice module overheating.
+
-
VCC
M
Bit 13/RH
Bit 12/LH
Bit 14/LL
Bit 15/RL
+
-
VCC
M
Bit 13/RH
Bit 12/LH
Bit 14/LL
Bit 15/RL
Summary of Contents for XN300
Page 4: ...II...
Page 14: ...10 XN300 slice modules 06 16 MN050002 EN www eaton com...