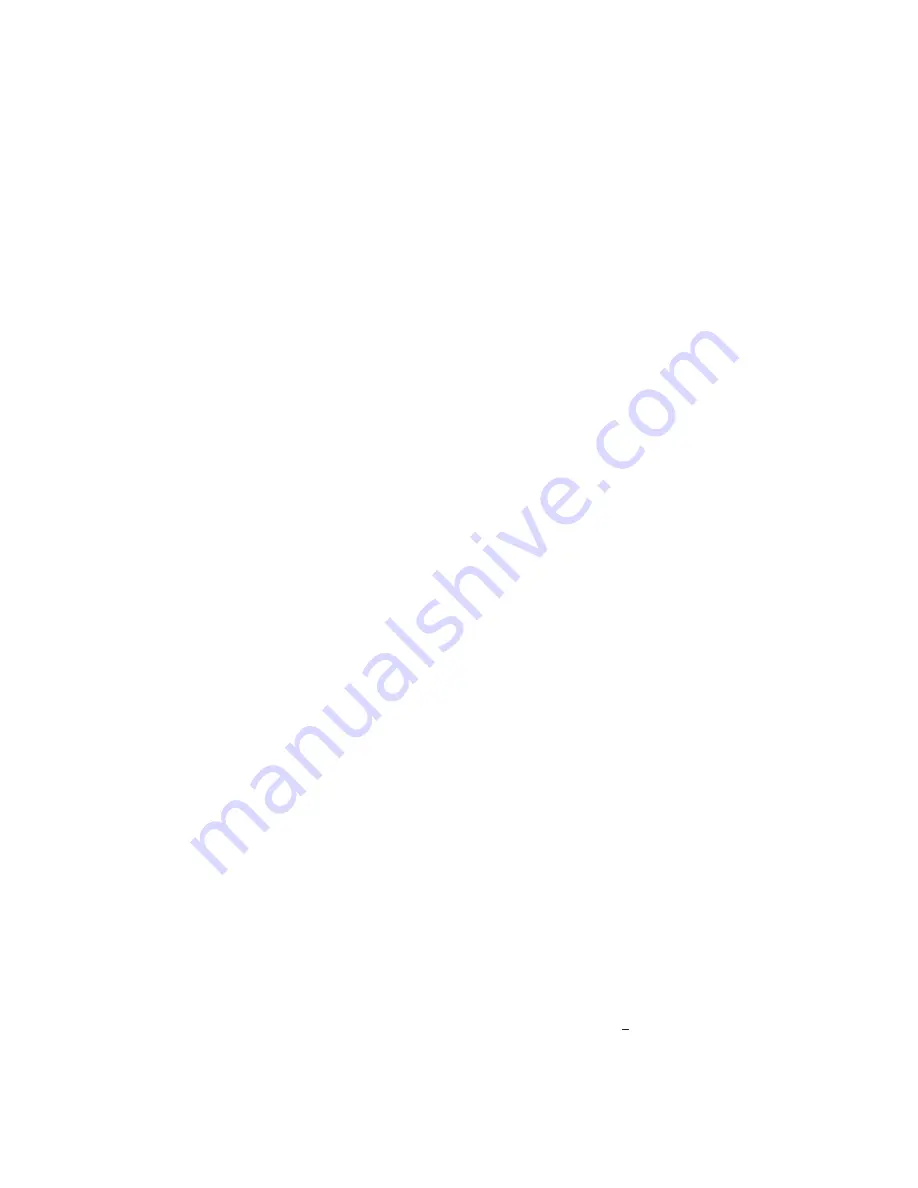
into band. When the voltage goes in-band, the timer is
decremented at the rate of 1.1 seconds for every second
elapsed, until it reaches zero.
Voltage-averaging mode
When the load voltage goes out-of-band, the time-delay
circuit is activated. During this time-delay period, the
microprocessor monitors and averages the instantaneous
load voltage. It then computes the number of tap changes
required to bring the average voltage back to the set
voltage level. When the time-delay period is complete,
the computed number of tap changes are performed
without any delay between them, up to a maximum of five
consecutive tap changes, to avoid an accumulative error. The
timer is not reset on voltage excursions in-band unless the
voltage stays in-band for at least ten continuous seconds.
An error-averaging characteristic is inherent with the voltage-
averaging mode.
ote:
N
To permit sufficient time for the microprocessor to
average the voltage, the time-delay period must be
30 seconds or longer. If the time delay is set for less
than 30 seconds, the control ignores the setting and
uses 30 seconds.
System line voltage
The control performs ratio correction in the firmware, and,
consequently, the primary voltage must be entered for the
control to perform this calculation. This value is simply the
nominal single-phase voltage supplied across the L and SL
terminals. Regulators shipped from the factory are set for
the voltage indicated by the pin on the nameplate, and this
value is programmed into the control. If the regulator is
installed on any other system voltage, this system voltage
must be entered for proper operation.
Overall PT ratio
Since the control performs ratio correction in the firmware,
the PT ratio for the voltage-sensing supply is required
for the control to perform the calculation. The ratio to be
programmed in the control is the Overall PT Ratio, which
is a combination of the ratios of the PT in the tank and
the RCT. For standard voltages shown on the regulator
nameplate an Overall PT Ratio is listed. The Overall PT
Ratio, which corresponds to the regulator’s rated voltage, is
set by the factory. If the regulator is installed on any other
system voltage, the corresponding Overall PT Ratio is also
required and must be determined. See
Control Programming: Allowable system voltages and
calculation of overall PT ratio
for more information.
The voltage from the RCT is normally corrected to 120 V.
However, when this voltage is other than 120 V, the control
will calibrate the input voltage to a 120 V (or 240 V when
FC 148 is set to 240 Volts) base and 120 V (or 240 V) will be
displayed at FC 6. The voltage test terminals will continue to
show the voltage as applied to the control from the RCT.
Internal PT ratio
The CL-7 control does not require a ratio correction
transformer (RCT) for the internal differential PT (IDPT). If
a regulator design includes an IDPT, but does not have a
second RCT, the control is able to use the Internal PT ratio
to determine the differential and source-side voltage. In
order for this to work, the Internal PT ratio must be entered
at FC 44
and the Vin PT Configuration (FC 146) must be
set to Vdiff without RCT2. The Internal PT ratio is also used
by the control to determine the source bushing voltage
when the FC 146 is set to Vin and the the voltage regulator
is equipped with a PT used to measure the voltage between
the S and SL bushings.
Current transformer primary rating
The control is designed for 200 mA as the rated CT current
and will meter to 800 mA with no loss of accuracy. Ratio
correction is performed by the firmware, and, consequently,
the CT primary rating must be entered. The CT primary
rating is available on the regulator nameplate.
EXAMPLE: If a CT ratio 400/0.2 is indicated on the
nameplate, then 400 must be entered at FC 45.
Delta-connected (line-to-line connected) regulators
When a regulator is connected line-to-line, the phase angle
of the line current is 30 degrees displaced from the voltage
impressed across the regulator. After setting the Regulator
Configuration, FC 41, the correct relationship between the
voltage and current is established. Setting the regulator
Configuration to the incorrect delta value (lagging instead of
leading, or vice versa), the phase angle will be in error 60
degrees.
See
Section 3: Initial Control Programming:
Determination of leading or lagging in delta-connected
for information on selecting the correct setting.
Below are considerations concerning delta-connected
regulators:
●
●
The basic decision-making of the control when line-drop
compensation is not used is not affected by the phase
angle; therefore, operation will be correct even if FC 41
is set to either of the two incorrect values. This is true for
forward and reverse operation.
●
●
If line-drop compensation is used, the scaling of the
R and X values is controlled by FC 41; therefore, it is
important to correctly set FC 41 for the compensated
voltage to be correctly determined.
●
●
The following metering parameters will be correct only if the
Regulator Configuration is correctly set: power factor, kVA,
kW, kvar, demand kVA, demand kW, and demand kvar.
ote:
N
The kVA, kW, kvar, demand kVA, demand kW, and
demand kvar use the line-to-line voltage; therefore,
they display the value at the regulator not on any one
feeder. To determine the total three-phase value of
any one of these parameters, each regulator value
must be divided by √3 (1.732) before adding the three
together.
28
INSTALLATION, OPERATION, AND MAINTENANCE INSTRUCTIONS
MN225003EN April 2018
CL-7 Voltage Regulator Control