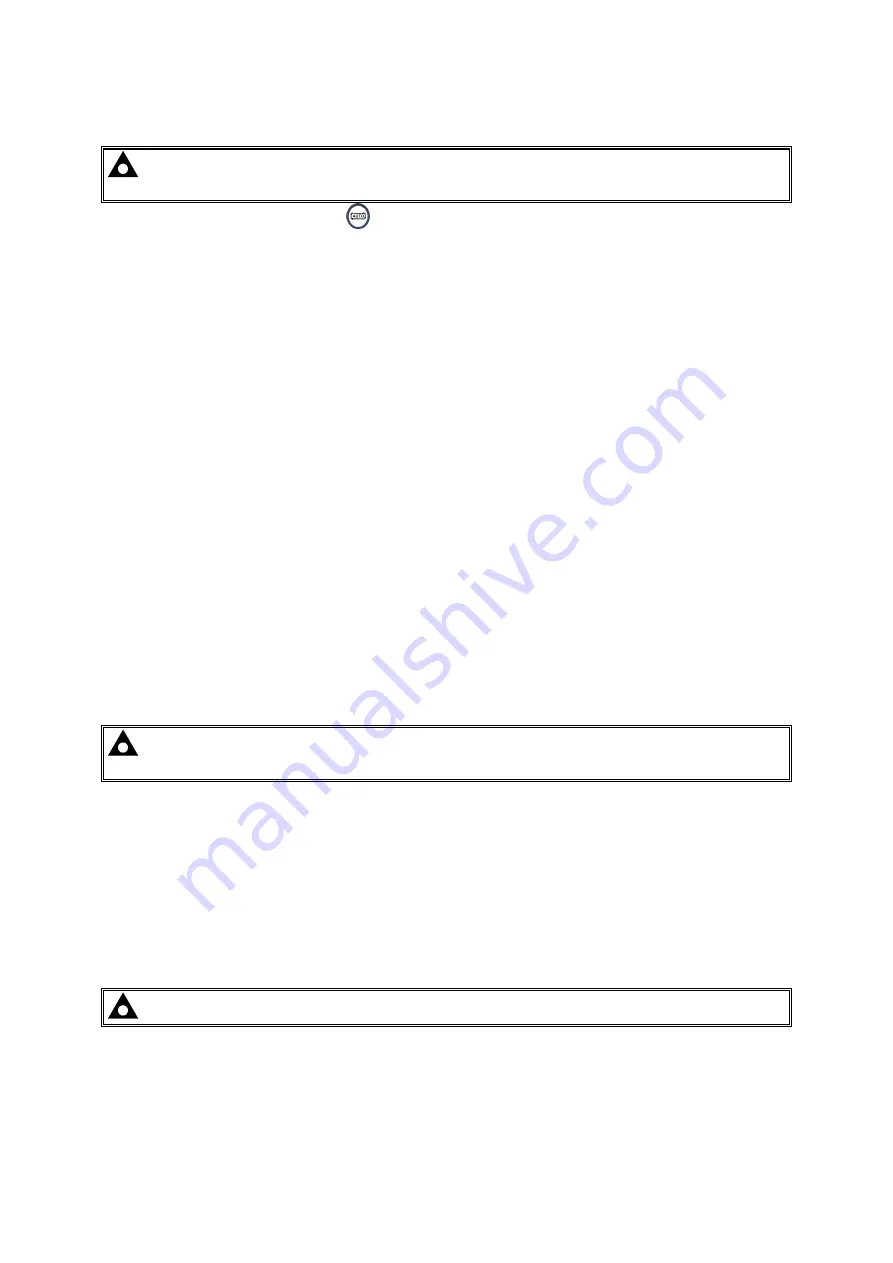
Operation
81
6.5 AUTOMATIC MODE
NOTE: If a digital input configured to
panel lock
is active, changing module modes will
not be possible. Viewing the instruments and event logs is NOT affected by panel lock.
Activate auto mode be pressing the
pushbutton. An LED indicator beside the button confirms this
action.
Auto mode will allow the generator to operate fully automatically, starting and stopping as required with
no user intervention.
6.5.1 WAITING IN AUTO MODE
If a starting request is made, the starting sequence will begin.
Starting requests can be from the following sources:
•
Activation of an auxiliary input that has been configured to
remote start on load
or
remote
start off load.or Remote Start Dead Bus Synchronising (see elsewhere in this manual)
•
Request from DSE8660 mains controller or from another DSE8610 controller over the MSC
link.
•
Activation of the inbuilt exercise scheduler.
•
Instruction from external remote telemetry devices using the RS232 or RS485 interface.
6.5.2 STARTING SEQUENCE
To allow for ‘false’ start requests such as mains brownouts, the
start delay
timer begins. There are
individual start delay timers for each of the different start request types.
Should all start requests be removed during the
start delay
timer, the unit will return to a stand-by
state.
If a start request is still present at the end of the
start delay
timer, the fuel relay is energised and the
engine will be cranked.
NOTE: If the unit has been configured for CAN, compatible ECU’s will receive the start
command via CAN.
If the engine fails to fire during this cranking attempt then the starter motor is disengaged for the
crank
rest
duration after which the next start attempt begins. Should this sequence continue beyond the set
number of attempts, the start sequence will be terminated and the display shows
Fail to Start.
The starter motor is disengaged when the engine fires. Speed detection is factory configured to be
derived from the main alternator output frequency, but can additionally be measured from a Magnetic
Pickup mounted on the flywheel (Selected by PC using the 8600 series configuration software).
Additionally, rising oil pressure or charge alternator voltage can be used to disconnect the starter
motor (but cannot detect underspeed or overspeed).
NOTE: If the unit has been configured for CAN, speed sensing is via CAN.
After the starter motor has disengaged, the
Safety On
timer activates, allowing Oil Pressure, High
Engine Temperature, Under-speed, Charge Fail and any delayed Auxiliary fault inputs to stabilise
without triggering the fault.
Summary of Contents for DSE8610
Page 47: ...Installation 47 4 2 2 3 PHASE 4 WIRE WITHOUT EARTH FAULT PROTECTION...
Page 51: ...Installation 51 4 3 2 SINGLE PHASE WITHOUT EARTH FAULT...
Page 53: ...Installation 53 4 3 4 2 PHASE L1 L2 3 WIRE WITHOUT EARTH FAULT...
Page 55: ...Installation 55 4 3 6 2 PHASE L1 L3 3 WIRE WITHOUT EARTH FAULT MEASURING...
Page 118: ...Intentionally Left Blank 118...