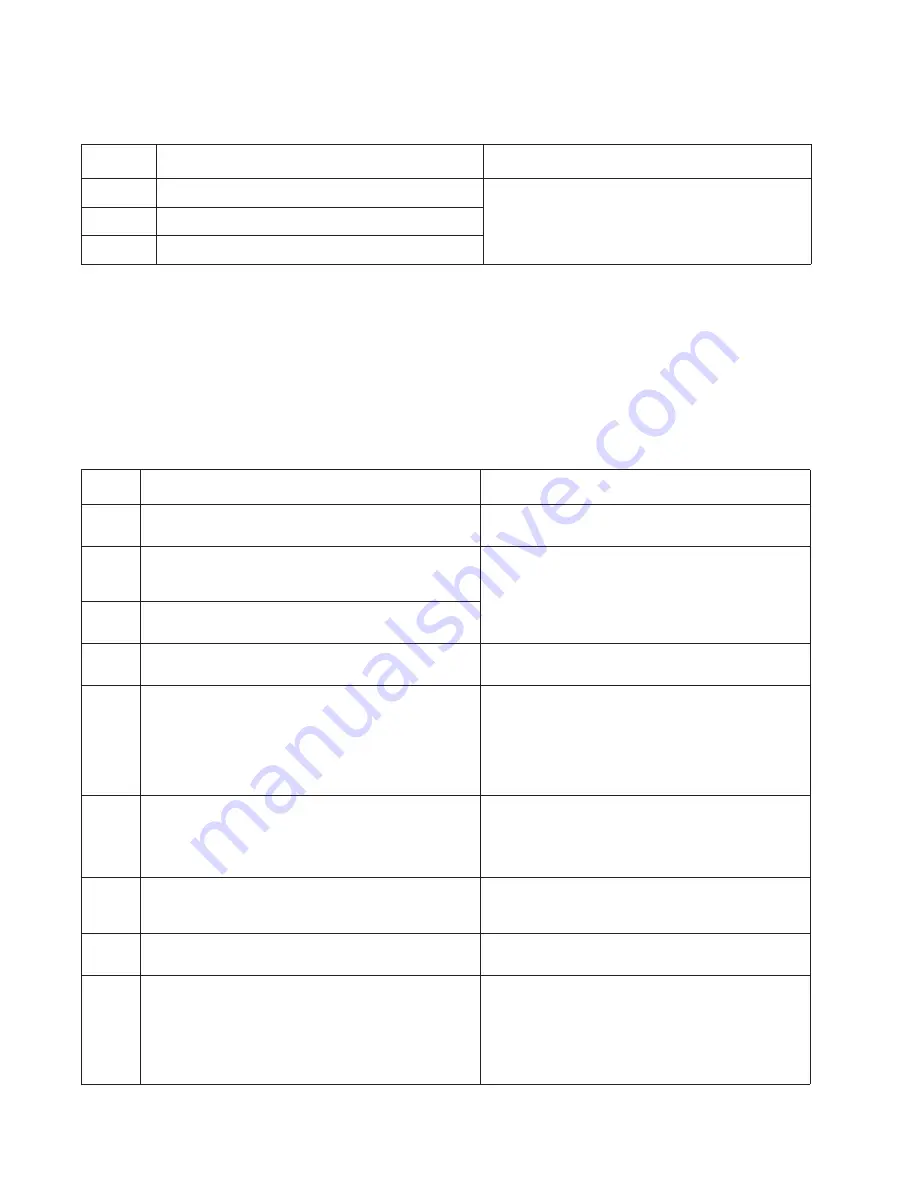
2-20
Service Manual
Cartridge error messages
Paper jam error codes (200-series)
Note:
The Event log (See
“EVENT LOG” on page 3-32
) will list any of these errors that have occurred.
Repeating jams or jam messages can be caused by any of the following:
•
Faulty/contaminated pick solenoids or worn cams of the solenoids.
•
Faulty/contaminated flags or springs.
•
Debris in the paper path.
•
Media not of the specified length.
Error
Description
Action
30
Invalid refill
Replace the cartridge.
31
Missing or defective cartridge
32
Unsupported print cartridge
Error
Description
Action
200.00
Paper jam around input sensor.
Remove the PC kit and paper or debris at the input
sensor.
200.01
Classic input jam. The media is too long over the input
sensor. Possible causes include multi-sheet feed, tray
size sensing problem, and media slippage.
First, remove the PC kit and paper or debric at the
input sensor. Then, inspect the flag on the input
sensor. It should rotate freely. Replace the sensor if
necessary. Finally, check the paper size settings in
the printer and the driver.
200.02
The main input sensor never became uncovered from
the sheet ahead.
200.03
The video never started on the page at the input
sensor within two inches after hitting the input sensor
Check the printhead. See
“Printhead service
check” on page 2-54
.
200.04
The media at the input sensor before interrupt
occurred–not enough time elapsed since the printhead
started to expect the printhead mirror motor lock.
Possible causes include bouncy sensor or
exceptionally fast pick– perhaps due to media pre-
staged in the source tray.
Carefully remove the tray and notice if the leading
edge of the media is pointed upward and out of the
tray. If so, then inspect the tray wear strips and
replace if necessary.
Inspect the input sensor flag and replace it if it does
not rotate freely or is too loose.
200.06
Imaged page not expected page (bouncy passthru
sensor)
Remove the toner cartridge/PC kit. At the front,
remove the upper front guide, and inspect the flag on
the manual input sensor. If the flag is loose, then
replace it. See
“Media manual input sensor” on
page 2-52
.
200.08
Media reached the input sensor before the EP was
ready
Inspect the tray for prestaging. Verify the proper
media and inspect the tray wear strips. Replace the
wear strips if necessary.
200.09
Transfer servo never started
Inspect the LVPS/HVPS. See
“Engine board
service check” on page 2-36
.
200.12
Media detected at manual feeder sensor when not
expected. Possible causes include user insert of media
when motor is running or pre-staged media in the tray.
Carefully remove the tray and notice if the leading
edge of the media is pointed upward and out of the
tray. If so, then inspect the tray wear strips and
replace if necessary.
Inspect the input sensor flag and replace it if it does
not rotate freely or is too loose.
Summary of Contents for 3333DN
Page 1: ... 02 Nov 2009 ...
Page 2: ... ...
Page 10: ...x Service Manual ...
Page 15: ...Notices and safety information xv ...
Page 16: ...xvi Service Manual ...
Page 28: ...1 8 Service Manual ...
Page 31: ...General information 1 11 Reduce Enlarge 25 to 400 Copy only ...
Page 160: ...3 56 Service Manual ...
Page 172: ...4 12 2 Remove the three screws B securing the top of the controller shield B ...
Page 182: ...4 22 6 Remove the screw D from the gear E 7 Remove the plastic bushing F ...
Page 192: ...4 32 2 Carefully pull the scanner front cover away from the tub assembly ...
Page 205: ...Repair information 4 45 5 Remove the three screws B from the left door mount B ...
Page 208: ...4 48 8 Use a screwdriver to pop the inner shaft lock B loose 9 Remove the inner shaft lock C ...
Page 211: ...Repair information 4 51 5 Remove the e clip B 6 Remove the media feed clutch with cable C ...
Page 217: ...Repair information 4 57 7 Open the front access door and remove the lower paper guide B ...
Page 219: ...Repair information 4 59 5 Remove the three screws B from the left side of the printer B ...
Page 250: ...4 90 12 Disconnect LSU HSYNC extension cable at the connector in the middle of the cable ...
Page 251: ...Repair information 4 91 13 Remove the three screws A from the left rear frame assembly A A A ...
Page 252: ...4 92 14 Remove the three screws B from the right rear frame assembly B B B ...
Page 282: ...6 2 Service Manual ...
Page 284: ...7 2 Service Manual Assembly 1 Covers 3 11 7 13 5 16 9 15 2 10 6 17 4 12 8 14 1 17 18 ...
Page 286: ...7 4 Service Manual Assembly 2 Imaging 3 11 7 13 5 16 9 15 2 10 6 4 12 8 14 1 ...
Page 288: ...7 6 Service Manual Assembly 3 Tray assemblies 3 2 1 5 4 ...
Page 296: ...7 14 Service Manual ...
Page 304: ...I 8 Service Manual ...