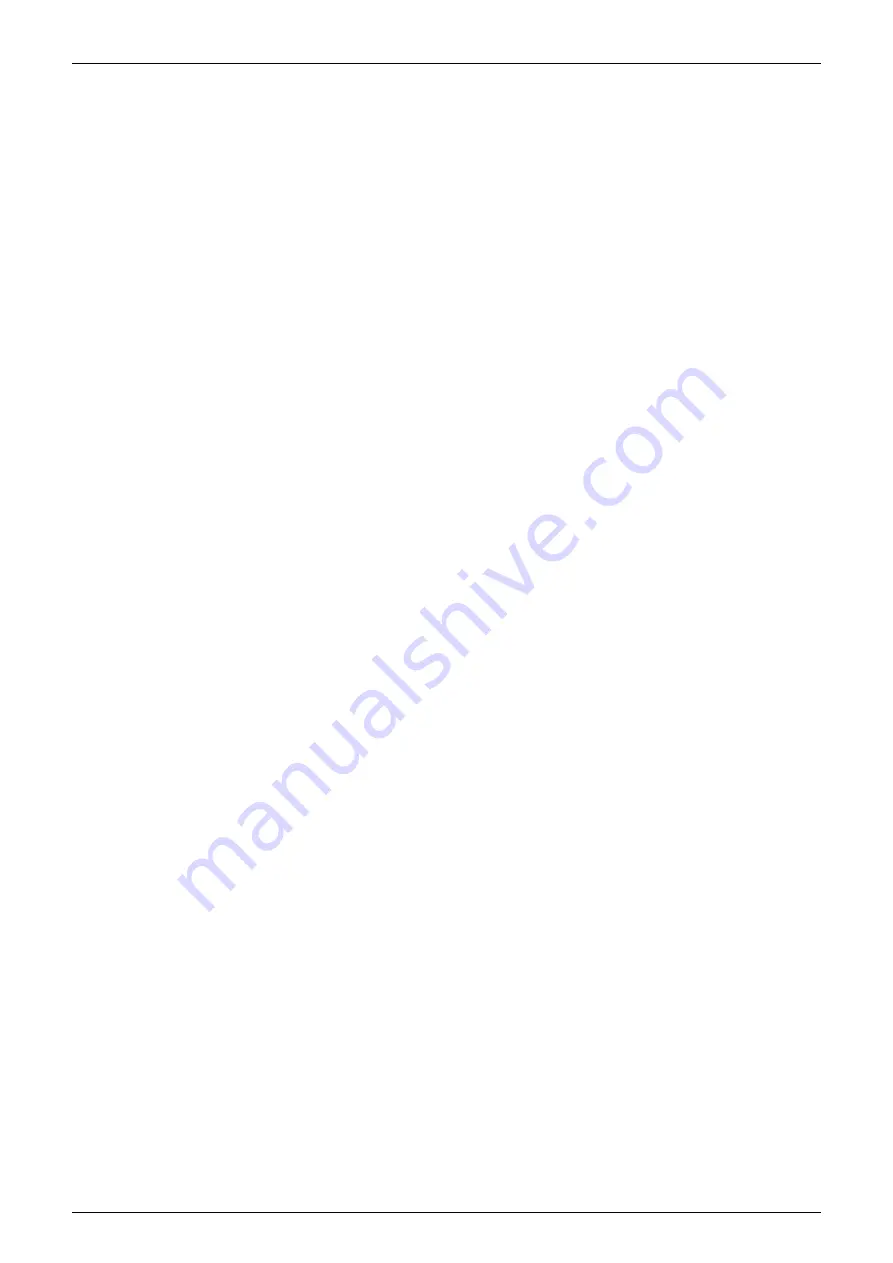
ESIE15-13C
ii
Table of Contents
Part 4 - Field Setting ....................................................................57
1.1 Pre-run Checks ......................................................................................58
1.2 Remote Controller Confirmation.............................................................58
1.3 Test Run.................................................................................................59
1.4 Precautions Regarding Test Run ...........................................................59
1.5 Failure Diagnosis at the Moment of First Installation .............................60
2. Field Setting from Remote Controller....................................................61
2.1 Wired Remote Controller........................................................................61
2.2 Wireless Remote Controller ...................................................................66
2.3 Settings Contents and Code No. for Indoor Units ..................................67
2.4 Overview of the Field Setting on the Outdoor Units ...............................73
2.5 Quiet (Low Noise) Operation..................................................................74
2.6 I-Demand Function.................................................................................76
2.7 Setting for Low Humidity Application......................................................77
2.8 Defrost Start Setting ...............................................................................80
2.9 Slow start................................................................................................80
3. Field Setting from Outdoor Unit PCB ....................................................81
3.1 Location of DIP Switch and BS Button ...................................................81
3.2 Field Setting for Outdoor Unit.................................................................82
4. Emergency Operation ...........................................................................92
Part 5 - Service Diagnosis ............................................................ 95
1. Maintenance Inspection ........................................................................97
2. Symptom-based Troubleshooting .........................................................99
2.1 Overview ................................................................................................99
2.2 Equipment does not Operate ...............................................................100
2.3 Indoor Unit Fan Operates, but Compressor does not Operate ............102
2.4 Cooling / Heating Operation Starts but Stops Immediately ..................104
2.5 After Unit Shuts Down, It cannot be Restarted for a While ..................105
2.6 Equipment Operates but does not Provide Cooling .............................107
2.7 Equipment Operates but does not Provide Heating .............................109
2.8 Equipment Discharges White Mist .......................................................111
2.9 Equipment Produces Loud Noise or Vibration .....................................112
2.10 Equipment Discharges Dust.................................................................113
2.11 Remote Controller LCD Displays "
" ..................................................114
2.12 Swing Flap does not Operate...............................................................115
3. Troubleshooting by LED Indications ...................................................117
4. Troubleshooting by Remote Controller ...............................................118
4.1 Procedure of Self-diagnosis by Remote Controller ..............................118
4.2 Error Codes and Description ................................................................122
4.3 Safety Devices .....................................................................................123
4.4 Indoor Unit PCB Abnormality ...............................................................124
4.5 Drain Water Level System Abnormality................................................125
4.6 Indoor Unit Fan Motor Abnormality ......................................................127
4.7 Capacity Setting Abnormality ...............................................................128
Summary of Contents for RZQG71L9V1
Page 2: ......
Page 6: ...ESIE15 13C iv Table of Contents...
Page 14: ...Introduction ESIE15 13C xii...
Page 18: ...Outlook Outdoor Units ESIE15 13C 4 General Information 2 Outlook Outdoor Units...
Page 22: ...Operating range ESIE15 13C 8 General Information...
Page 108: ...Emergency Operation ESIE15 13C 94 Field Setting...