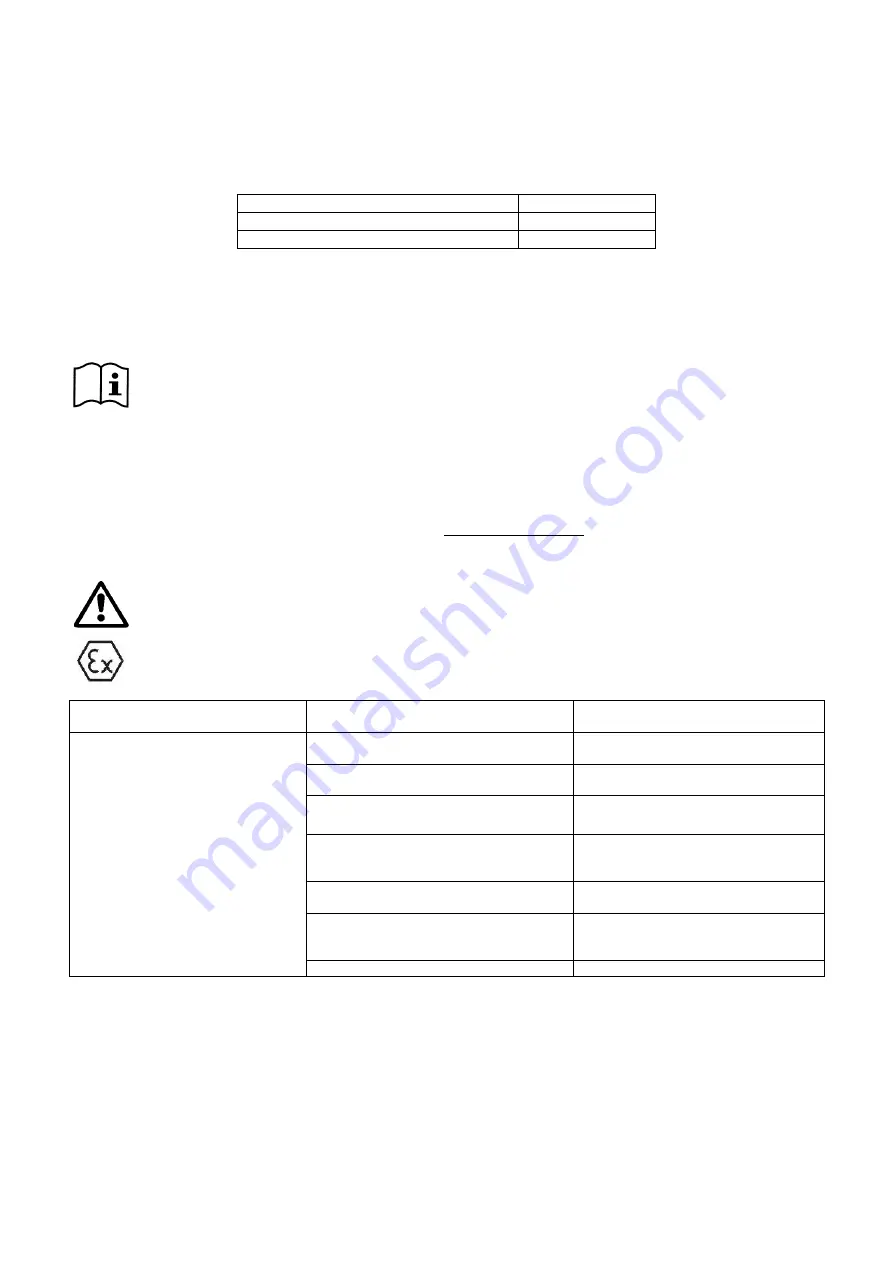
ENGLISH
35
2. Pour the oil into the chamber. The suitable amount of oil is indicated by the second oil venting hole
(positioned beside the vertical filling hole). Once the oil has reached and escapes from the hole at the
side, the oil quantity is correct.
3. Fit the oil screws with new gaskets.
The table shows the quantity of oil in the oil chamber of FKV and FKC pumps. Oil type: ESSO MARCOL 152.
Motor type
Oil quantity [l]
up to 3kW 2poles / up to 2.2kW 4poles
0.5
from 4kW 2poles /from 3kW 4poles
0.95
8.2 Special maintenance
Special maintenance operations must be carried out exclusively by an assistance workshop authorised by
DAB
Pumps.
8.3 Contaminated
pumps
If a pump has been used for a liquid which is injurious to health or toxic, the pump will be
classified as contaminated.
If you are asking to have a pump repaired, you must contact the service centre to give them the details about
the pumped liquid, etc., before sending the pump for repair. Otherwise, the service centre may refuse to accept
the pump.
However, any application for service (no matter to whom it may be made) must include details about the
pumped liquid if the pump has been used for liquids which are injurious to health or toxic.
Before a pump is returned, it must be cleaned in the best possible way before it is returned.
Service instruction and service video can be found on www.dabpumps.com.
9. FAULT FINDING
Before attempting to diagnose any fault, make sure that the fuses have been removed or the
mains switch has been switched off. It must be ensured that the power supply cannot be
accidentally switched on. All rotating parts must have stopped moving.
All regulations applying to pumps installed in potentially explosive environments must be
observed. It must be ensured that no work is carried out in potentially explosive atmosphere.
INCONVENIENTS PROBABE
CAUSES
REMEDIES
Failure in
electric pump.
Lack of current to the motor.
Check electric network, supply cables,
connections and fuses.
Insufficient
voltage.
Check the value (see chapter 10
“Technical Data”).
Thermal protection activated.
Wait for motor cooling, reset thermal
relay and check ratin starting.
No signal from electrodes for level
control.
Wait for level reset, check efficiency of
level control relay and relevant
electrodes.
One phase interruption (three-phase
motors).
Reset connections.
Clogged impeller.
Remove obstruction, wash and clean
(contact the Assistance Service if
necessary).
Motor failure.
contact the Assistance Service.