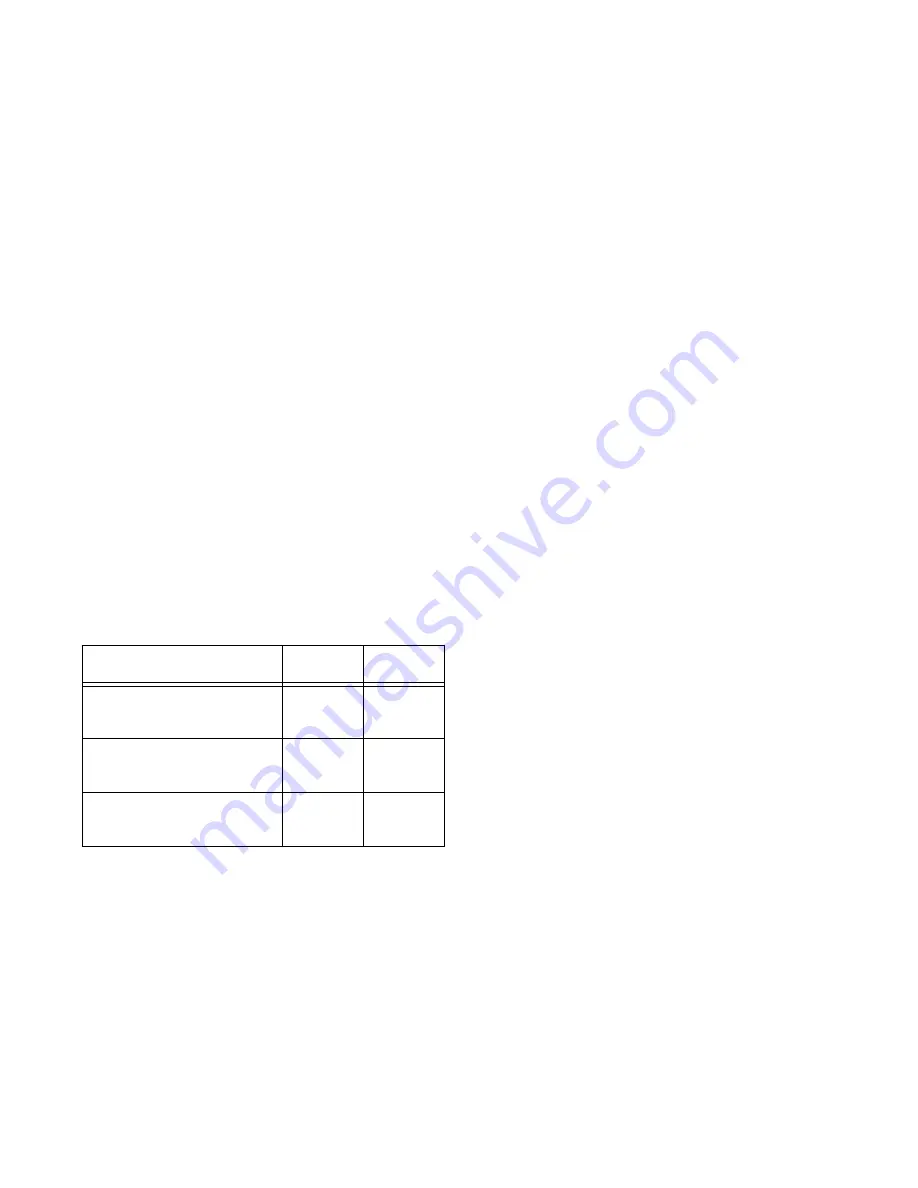
Chapter 3 - Drive System: Drive Shafts and Differentials
99
12.
Assembly notes:
•
Inspect the splines and shaft seals before install-
ing the front drive shaft. Make any necessary
repairs before reassembly.
•
Lubricate the splined joints with anti-seize com-
pound on assembly.
•
Reverse the removal procedure to install the
front drive shaft.
•
Replace any worn hardware or components
before reassembly. If the self-locking feature of
any of the nuts is degraded, replace the nuts or
apply thread locking compound such as Loctite
242 (blue) to the threads.
•
When locating the front differential, install all of
the hardware that secures the differential and
torque bracket, then go back and tighten it.
•
When locating the brush guard, slip it straight on
from the front, then secure it by inserting the
bolts in the holes for the top two attachment
points. Once it is held in position, insert the
remaining bolts, then install and tighten the nuts.
•
Check the level of the gear lube in the differen-
tial. Top-up if needed before running the vehicle.
•
Tighten the hardware to the torques specified in
the accompanying table:
** Install with permanent thread locking compound
such as Loctite®
262 (red).
13.
Test-run the vehicle in a safe area before return-
ing it to service.
Item
ft-lbs
N-m
Front differential to
frame
32-36**
43-49**
Front differential to
torque bracket
16**
24**
Torque bracket to
frame
12
16
FRONT HALF SHAFT REMOVAL
Failure mode, cause, and remedy:
•
The Rzeppa type constant velocity joints at each
end of the front half shafts are protected by
rub-
ber boots
. If a boot gets torn, the joint will be
damaged quite rapidly by any foreign material
that gets into the joint. Replace the joint if a boot
is compromised for any significant length of time.
•
Heat is the enemy of rotating joints. These
joints should be kept clean
to dissipate heat.
Avoid pressure washing. Wipe the joints clean
when they become dirty.
•
If a joint begins to click, that is a sign that the
internal races have troughs worn into them. The
clicking
is the sound of the balls that transmit
force between the inner and outer races passing
over the trough. A constant velocity joint that
clicks as the steering or suspension travel
through their range of motion has worn, and
should be replaced.
•
At the time of printing, it is uncertain if replace-
ment axle components will be available:
- Replacement boots may be available for instal-
lation on the constant velocity joints
- Replacement joints may be available for instal-
lation on the axles.
- If replacement of a constant velocity joint
becomes necessary, the complete axle (half
shaft) may be the only service option.
Use the following steps to remove a front axle:
1.
Remove the front wheel:
1a. If an impact wrench is unavailable, loosen
the lug nuts on the wheel driven by the
axle that is to be replaced using a 3/4”
wrench.
1b. Lift and safely support the front of the
vehicle.
1c. Remove the wheel.
Summary of Contents for Volunteer 4x4 Utility Vehicle
Page 2: ......
Page 4: ......
Page 12: ...Chapter 1 Introduction 8 ...
Page 66: ...Chapter 2 Drive System CVT and Transfer Case 62 ...
Page 78: ...Kohler Enclosed CVT Addendum 74 ...
Page 92: ...Caterpillar Enclosed CVT Addendum 88 ...
Page 126: ...Chapter 3 Drive System Drive Shafts and Differentials 122 ...
Page 278: ...Chapter 8 Caterpillar Engine and Related Systems 274 ...
Page 319: ...Chapter 9 Electrical 315 Electrical Schematic Engine Harness w Kohler engine ...
Page 321: ...Chapter 9 Electrical 317 Electrical Schematic Engine Harness w Caterpillar engine 725 04341 ...
Page 322: ...Chapter 9 Electrical 318 ...
Page 327: ...5 ...
Page 328: ...6 ...