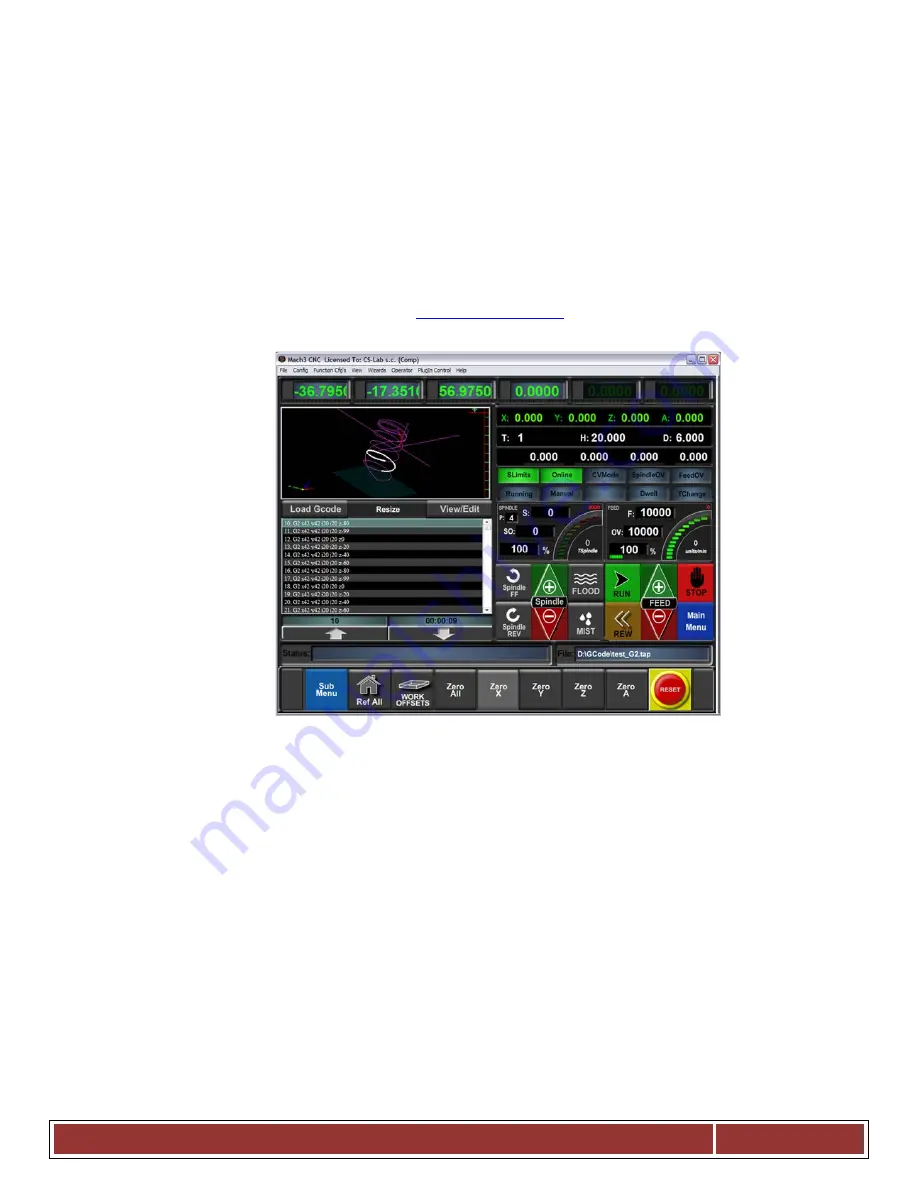
8.
Mach3 program – general information
Mach3 software of ArtSoft® Company has developed over many years and during these years, it
gathered many users. For relatively low price (~170USD) we get complete solution for multi-axis CNC
machining. Key benefits of the program are:
•
Flexibility
o
Ability to create own user interfaces, transparent and suited to specific machine
applications. There is a special visual editor where you can create the Mach3 in-
terface design from the beginning or use already existing project. On the inter-
net, there are many ready solutions. Below – one of the most visually attractive
interfaces available on
www.machmotion.com
.
o
Ability to self-extend the functionality of the program through macros, written
in simple and known by many people - VisualBasic®. It allows you to implement
a variety of measurement probes, automatic tool length measurement, auto-
matic storage of tools in many variants etc.
o
Plug-ins support, which further extend functions of the program and allows for
cooperation with outside motion controllers. Connection with CSMIO/IP-S con-
troller is made by that plug-in, made by our company.
•
Easy to use
o
Those, who are already little familiar with CNC machines are able to learn all the
general functions and rules of using the Mach3 program – within one day.
o
Configuration of the key parameters is transparent and intuitive, so they can be
quickly adjusted to the requirements of a specific machine.
•
Dynamic analysis of the trajectory
o
CNC program is analyzed in advance, so it allows for optimal adjustment of mo-
tion speed at every point of trajectory. Thus, the program is done quickly, but
with full smoothness of the motion.
C S - L a b s . c . – C S M I O / I P - S - C N C C o n t r o l l e r
Page 45