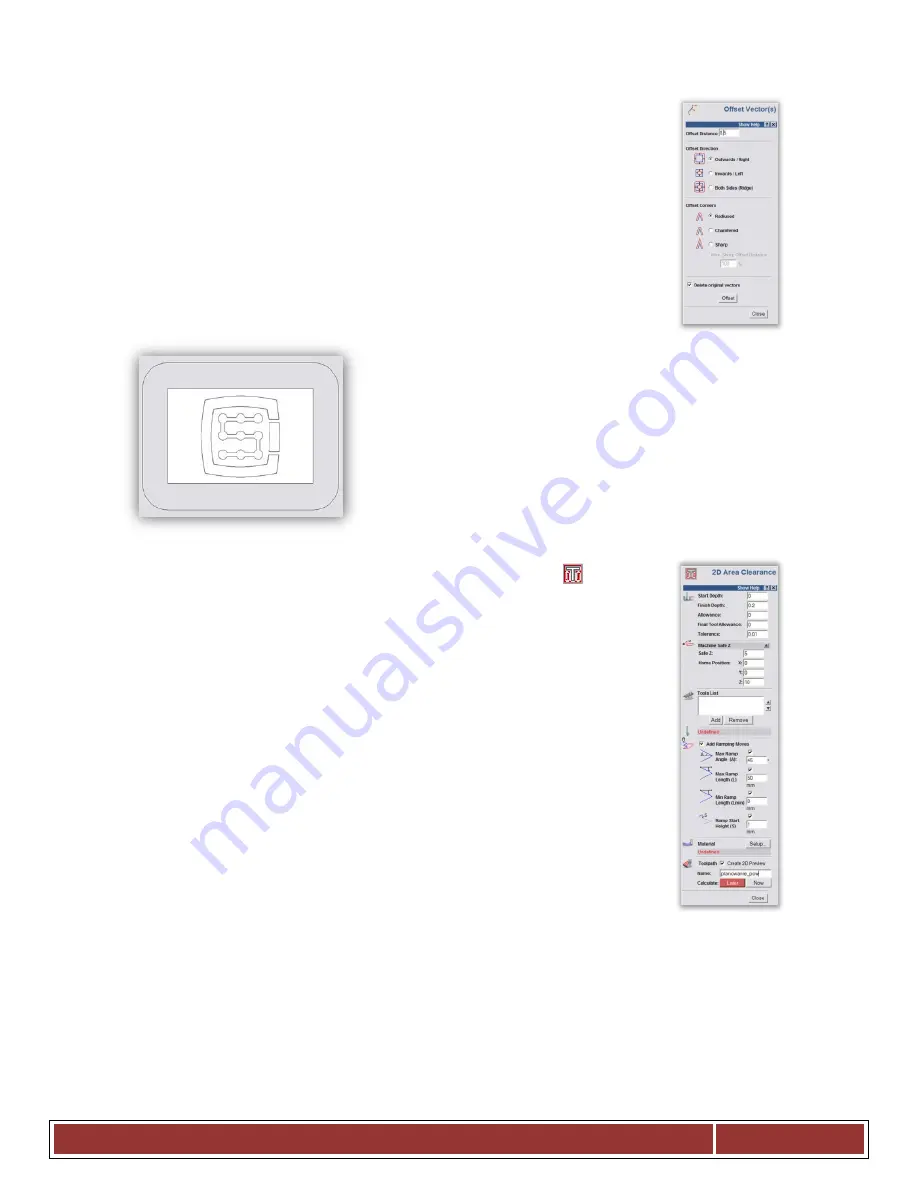
The newly created object with its position and size exactly coincides with the work-
ing area. Now you should add the additional enlargement that was mentioned, so
that the milling cutter will go with its whole diameter out of the material – thus we
get a better surface.
We click on our object and select „Vectors/Offset” menu position. The milling cut-
ter diameter is 8mm - we should give it a small reserve by entering as an Offset
Distance the 8.5mm value. We are giving the Offset Direction as Outwards – that is
the outside. Offset corners – irrelevant here. Select - Delete original vectors, be-
cause we do not need to save the original object.
At this stage, our project looks like this:
You can now generate trajectories for tools.
First, a tool path for planning the surface.
Select the object we have created and select Area Clearance
icon from
Toolpath tab.
In Finish Depth box, enter treatment depth - 0.2mm in this case. In toleration area,
enter 0,01mm. As practice shows, it is not worth to overdo with toleration value.
Of course, if you have a high-class mechanics, granite construction, all is thermally
stabilized, and you execute precise jobs – you can set the toleration more detailed.
Safe Z parameter you can set at 5mm, Home Position at [0, 0, 10]. You can also
select „Add Ramping Moves” on default parameters, the result is smoother entry
into the material.
C S - L a b s . c . – C S M I O / I P - S - C N C C o n t r o l l e r
Page 80