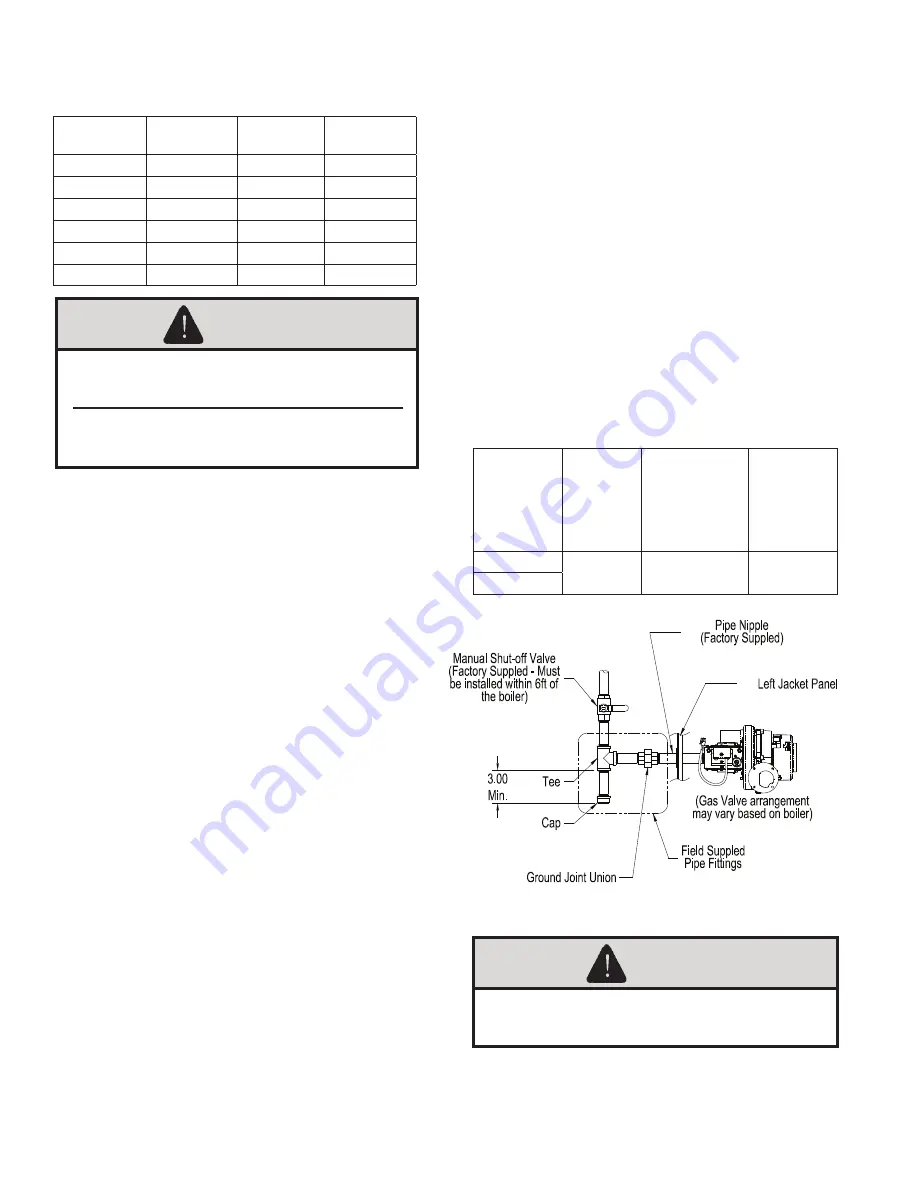
48
4. All above ground gas pipin
g upstream
from manual shut-off valve must be electrically
continuous and bonded to a grounding electrode. Do
not use gas piping as grounding electrode. Refer to
National Electrical Code
, NFPA 70.
C. Pressure test.
See Table 20 for Phantom Min./Max.
Pressure Ratings. The boiler and its gas connection
must be leak tested before placing boiler in operation.
1. Protect boiler gas control valve
. For all testing
over ½ psig, boiler and its individual shutoff valve
must be disconnected from gas supply piping. For
testing at ½ psig or less, isolate boiler from gas
supply piping by closing boiler’s individual manual
shutoff valve.
2. Locate leaks using approved
combustible gas
non-corrosive leak detector solution.
Table 19: Specific Gravity Correction Factors
Specific
Gravity
Correction
Factor
Specific
Gravity
Correction
Factor
0.60
1.00
0.90
0.82
0.65
0.96
1.00
0.78
0.70
0.93
1.10
0.74
0.75
0.90
1.20
0.71
0.80
0.87
1.30
0.68
0.85
0.81
1.40
0.66
WARNING
Explosion Hazard. Failure to use proper
thread compounds on all gas connectors
may result in leaks of flammable gas.
Gas supply to boiler and system must be
absolutely shut off prior to installing or
servicing boiler gas piping.
1. Use methods and materials in accordance
with local plumbing codes and requirements of gas
supplier. In absence of such requirements, follow
National Fuel Gas Code
, ANSI Z223.1/NFPA 54
and/or
Natural Gas and Propane Installation Code
,
CAN/CSA B149.1.
2. Use thread (joint) compounds (pipe dope)
resistant to action of liquefied petroleum gas.
3. Phantom boilers have factory supplied
Miscellaneous Part Carton which includes gas
piping components to connect boiler gas valve to
gas supply system. Install these components prior
to connecting boiler to gas supply system piping as
follows:
a. Locate and remove either ½ in. NPT x 6 in. long
black nipple and ½ in. NPT external gas shutoff
valve (PHNTM210), or ¾ in. NPT x 6 in. long
black nipple and ¾ in. NPT external gas shutoff
valve (PHNTM285 only).
b. Feed the appropriate nipple through factory
installed jacket left side panel grommet (refer
to Figure 1A or 1B for gas supply connection
identification) and screw the nipple into boiler
gas valve inlet port.
c. Mount the appropriate external gas shutoff valve
onto the threaded nipple end outside of the jacket
left side panel.
d. Install sediment trap, ground-joint union and
manual shut-off valve upstream of mounted
factory supplied manual shut-off valve. See
Figure 25.
Figure 25: Recommended Gas Piping
VII. Gas Piping
(continued)
Boiler
Model No.
Natural/LP
Gas Max.
Pressure
(in. w.c.)
Natural Gas
Min. Pressure
Inlet to Gas
Valve
(in. w.c.)
LP Gas
Min.
Pressure
Inlet to Gas
Valve
(in. w.c.)
PHNTM210
14
4.0
11.0
PHNTM285
Table 20: Min./Max. Pressure Ratings
DANGER
Explosion Hazard. Do not use matches, candles,
open flames or other ignition source to check for
leaks.
Summary of Contents for Phantom-X PHNTM210
Page 7: ...7 Figure 1B Model PHNTM285 I Product Description Specifications and Dimensional Data continued...
Page 52: ...52 VIII Electrical continued...
Page 53: ...53 VIII Electrical continued Figure 26 Wiring Connections Diagram...
Page 54: ...54 VIII Electrical continued Figure 27 Ladder Diagram...
Page 118: ...118...
Page 119: ...119...