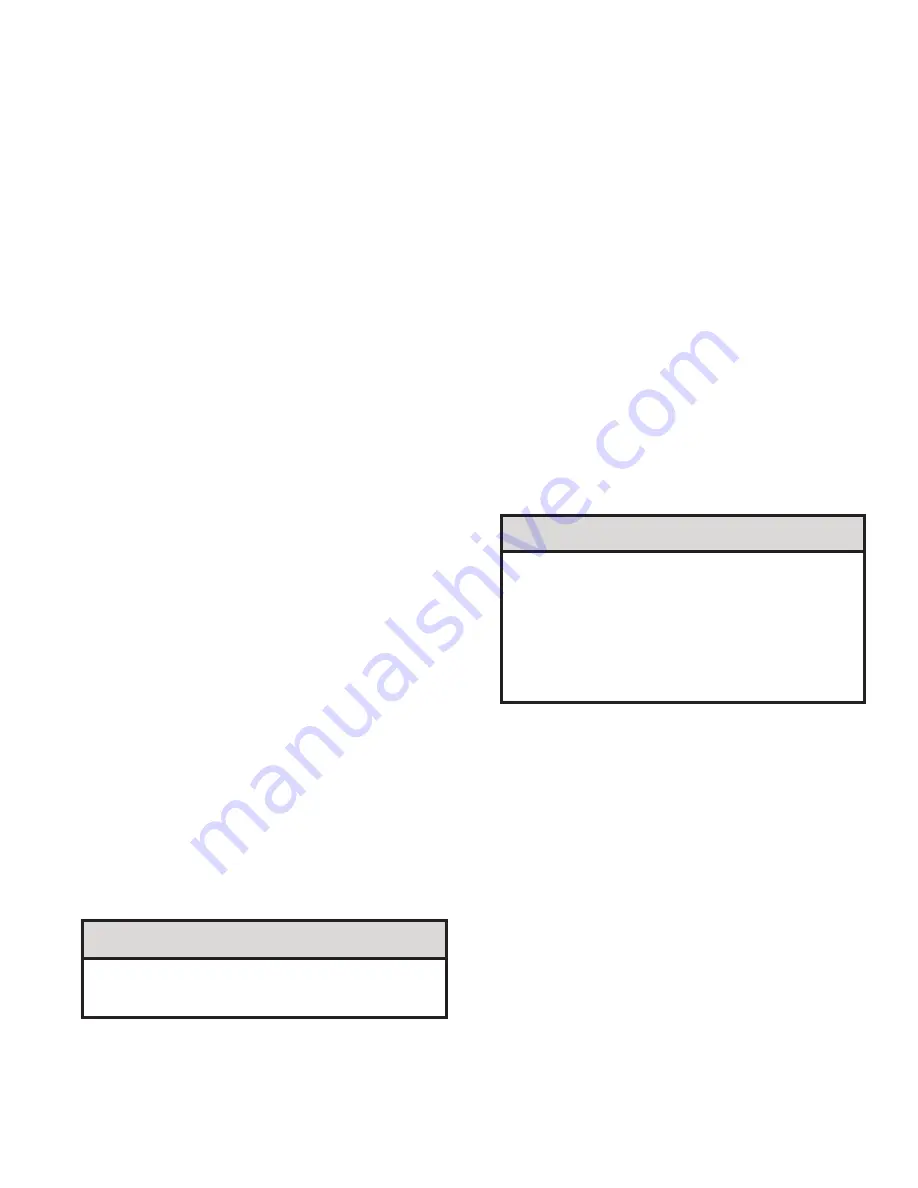
37
b. Install close nipple into tee branch, then, screw
the assembly into boiler left side front ¾ in.
tapping making sure tee run outlets are in vertical
plane and parallel to boiler side.
c. Install the ¾ in. NPT x 10 in. black nipple into
tee run top outlet.
d. Mount ¾ in. FPT x ¾ in. FPT Pressure Relief
Valve onto the 10 in. nipple.
e. Install Drain Valve into the tee bottom outlet.
3. Temperature /Pressure Gauge Piping,
PHNTM210 Boiler Models
a. Locate and remove 1 in. NPT x 4 in. long black
nipple, 1 in. x 1 in. x 1 in. NPT black tee, 1
in. x ¼ in. NPT black reducing bushing and
Temperature & Pressure Gauge.
b. Mount the nipple into 1 in. boiler supply tapping
(see Figure 1A), then, install the tee onto the
nipple, making sure 1 in. branch outlet is in
horizontal plane and facing the boiler front.
c. Install 1 in. x ¼ in. NPT black reducing bushing
into the tee branch, then, put in Temperature &
Pressure Gauge.
4. Temperature /Pressure Gauge Piping,
PHNTM285 Boiler Model
a. Locate and remove 1¼ in. NPT x 2 in. long black
nipple, 1¼ in. x 1¼ in. x ¾ in. NPT black tee,
¾ in. x ¼ in. NPT black reducing bushing and
Temperature & Pressure Gauge.
b. Mount the nipple into 1¼ in. boiler supply
tapping (see Figure 1B), then, install the tee onto
the nipple, making sure ¾ in. branch outlet is in
horizontal plane and facing the boiler front.
c. Install ¾ in. x ¼ in. NPT black reducing bushing
into the tee branch, then, put in Temperature &
Pressure Gauge.
B. Piping System To Be Employed.
Phantom boilers are designed to operate in a closed
loop pressurized system. Minimum pressure in the
boiler must be 14.5 PSI. Proper operation of the
Phantom boiler requires that the water flow through the
boiler remain within the limits shown in Table 14, any
time the boiler is firing.
NOTICE
Failure to maintain the flow through boiler within
specified limits could result in erratic operation
or premature boiler failure.
1. Near boiler piping must isolate boiler from
system piping via closely spaced tees
to insure
specified flow range through boiler any time the
boiler is firing:
a. The flow rate through the boiler loop is
maintained by factory supplied boiler circulator.
b. The flow rate through the boiler loop
is
completely independent
of the flow rate through
the heating system loop(s).
c. The flow rate through the heating system loop(s)
is controlled by installer sized/provided system
loop circulator(s).
d. This piping arrangement can be used either for
space heating-only applications or space heating
with indirect water heater(s) applications.
i.
Space heating only
- refer to Table 13 and
Figure 21 “Near Boiler Piping - Heating
Only” as applicable.
ii.
Space heating plus indirect water
heater(s)
- refer to Table 13 and Figure 22
“Near Boiler Piping - Heating Plus Indirect
Water Heater” as applicable.
NOTICE
Where it is not possible to install a separate
boiler loop, the system circulator must be
sized to ensure that the flow through boiler
stays within the defined parameters to prevent
overheating when the boiler is fired at it’s full
rated input. Install a flow meter to measure the
flow, or fire the boiler at full rate and ensure the
boiler DT does not exceed 35°F (19°C).
2. Direct connection of Phantom boiler to
heating system
, similar to a conventional boiler, is
NOT RECOMMENDED because:
a. The flow rate through system must be the same
as through boiler and fall within limits specified
in Table 12.
b. Pressure drop through entire system must be
known, added to pressure drop through boiler,
and, a circulator selected to provide required
flow at total calculated pressure drop.
c. It is often very difficult to accurately calculate
the pressure drop through the system.
d. In replacement installations, it may be nearly
impossible to get an accurate measurement of
piping amount and number of fittings in the
system. If system is zoned, the system flow rate
may drop well below recommended minimum
flow when only a single zone is calling for heat.
VI. Water Piping and Trim
B. Piping System To Be Employed (continued)
Summary of Contents for Phantom-X PHNTM210
Page 7: ...7 Figure 1B Model PHNTM285 I Product Description Specifications and Dimensional Data continued...
Page 52: ...52 VIII Electrical continued...
Page 53: ...53 VIII Electrical continued Figure 26 Wiring Connections Diagram...
Page 54: ...54 VIII Electrical continued Figure 27 Ladder Diagram...
Page 118: ...118...
Page 119: ...119...