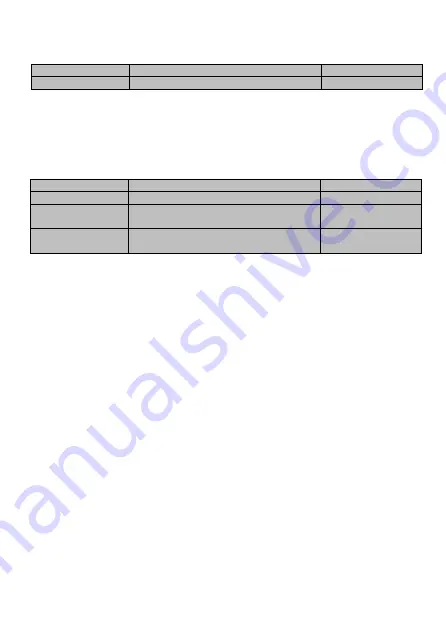
110
Code
Name
Setting Range
F9.03
PID output characteristic
0
~
1
【
0
】
0:Positive.When the feedback value is greater than the preset value,output frequency
will be decreased, such as tension control in winding application.
1:Negative.When the feedback value is greater than the preset value,output
frequency will be increased,such as tension control in unwinding application.
Code
Name
Setting Range
F9.04
Proportional gain
(
Kp
)
0.01
~
10.00
【
0.10
】
F9.05
Integral time
(
Ti
)
0.00
~
100.00S
【
1.00S
】
F9.06
Differential time
(
Td
)
0.00
~
10.00S
【
0.00S
】
Optimize the responsiveness by adjusting these parameters while driving an actual
load.
Adjusting PID control:
Use the following procedure to activate PID control and then adjust it while
monitoring the response.
1.Enabled PID control (F0.02=6).
2.Increase the proportional gain (Kp) as far as possible without creating oscillation.
3.Reduce the integral time (Ti) as far as possible without creating oscillation.
4.Increase the differential time (Td) as far as possible without creating oscillation.
Making fine adjustments:
First set the individual PID control constants, and then make fine adjustments.
●
Reducing overshooting
If overshooting occurs, shorten the differential time and lengthen the integral time.
●
Rapidly stabilizing control status