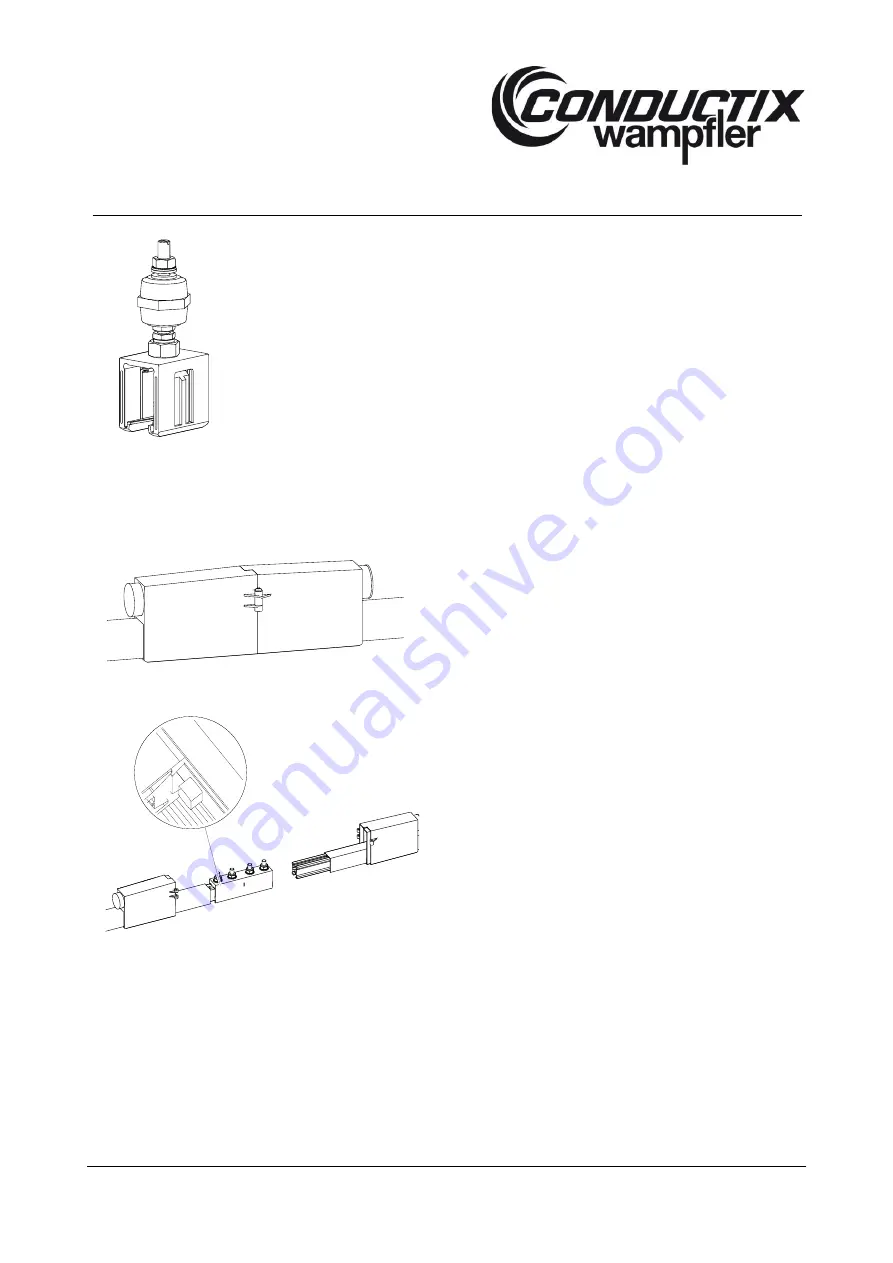
Operating Instructions
Insulated Conductor Rail System
SinglePowerLine Program 0813
BAL0813-0007-EN
www.conductix.com
translated document
page 28 of 108
Fig. 12: Hanger clamp 0813 with insulator
Fig. 13: Connector 0813
Fig. 14: Conductor rail at the connector stopper (aluminum-
stainless steel/CopperECO)
◼
Connector 081321-***
The conductor rail connections are made with compact screw
connectors.
Depending on the conductor material of the conductor bar, the
connectors have either a stopper (aluminum with stainless steel
strip and CopperECO) or an inspection window (copper) to be able
to check the functionally necessary gap of 2 to max. 3 mm at the
rail ends.
There are two insulating cap halves that are screwed together with
two screws for protection against contact.
Note/Tip:
Aluminum-stainless steel and CopperECO conductor
rails use the identical connector. A mixed installation of these two
types of conductor rail is permitted.