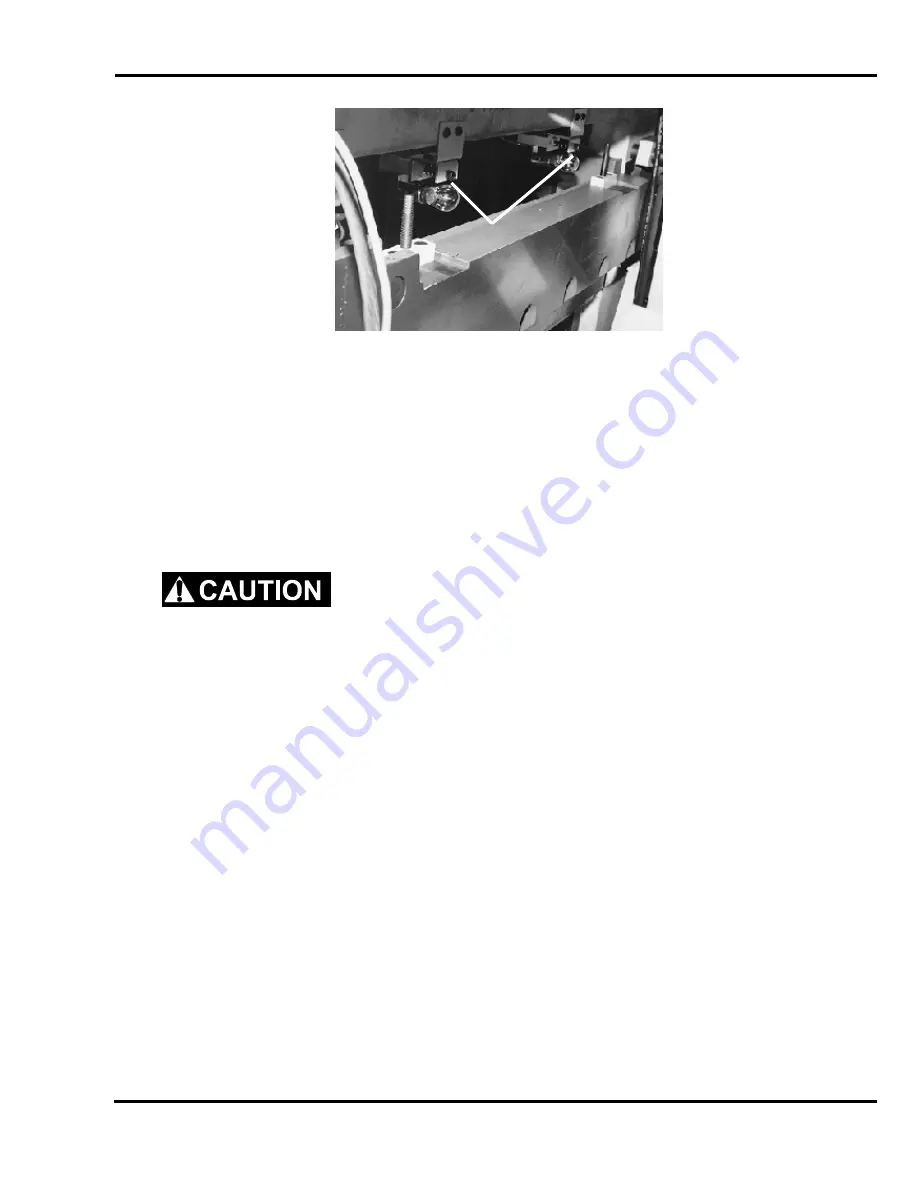
5.0 Installation & Setup
21
Figure 16
To Adjust:
1. Place a wide sheet of paper on the cut stick to view the line light.
2. Using a 3/16” hex allen wrench, turn one of the cap screws until you see a 1/16-1/8” beam.
NOTE: it is best to start by turning the screw clockwise. If the screw turns all the way in
before a line appears, begin turning the screw counterclockwise.
3. Similarly, turn the adjustment screw of the other bulb, until one continuous beam is seen
across the cut stick.
SHOCK HAZARD! Always disconnect power at main power panel
before working on the cutter. Lock it out to prevent accidental power up. See Power Lockout
Procedure, page 5.
Bulb replacement:
1. Make sure power is off (see Power Lockout Procedure, page 5).
2. Remove the old bulb by lightly pushing the bulb into the socket and turning it 1/4 turn
counterclockwise. CAUTION! If the bulb is still hot, allow a few minutes for it to cool.
3. Insert the new bulb into the socket, push it in and twist it clockwise until the bulb locks into
place.
4. Reconnect power and turn the main power switch on. Readjust the line if necessary.
Line Light
Adj. Screws
Summary of Contents for TITAN 265 XG
Page 47: ...7 0 Knife Installation Changing 47 NOTES...
Page 52: ...F 265XG EO January 2014...