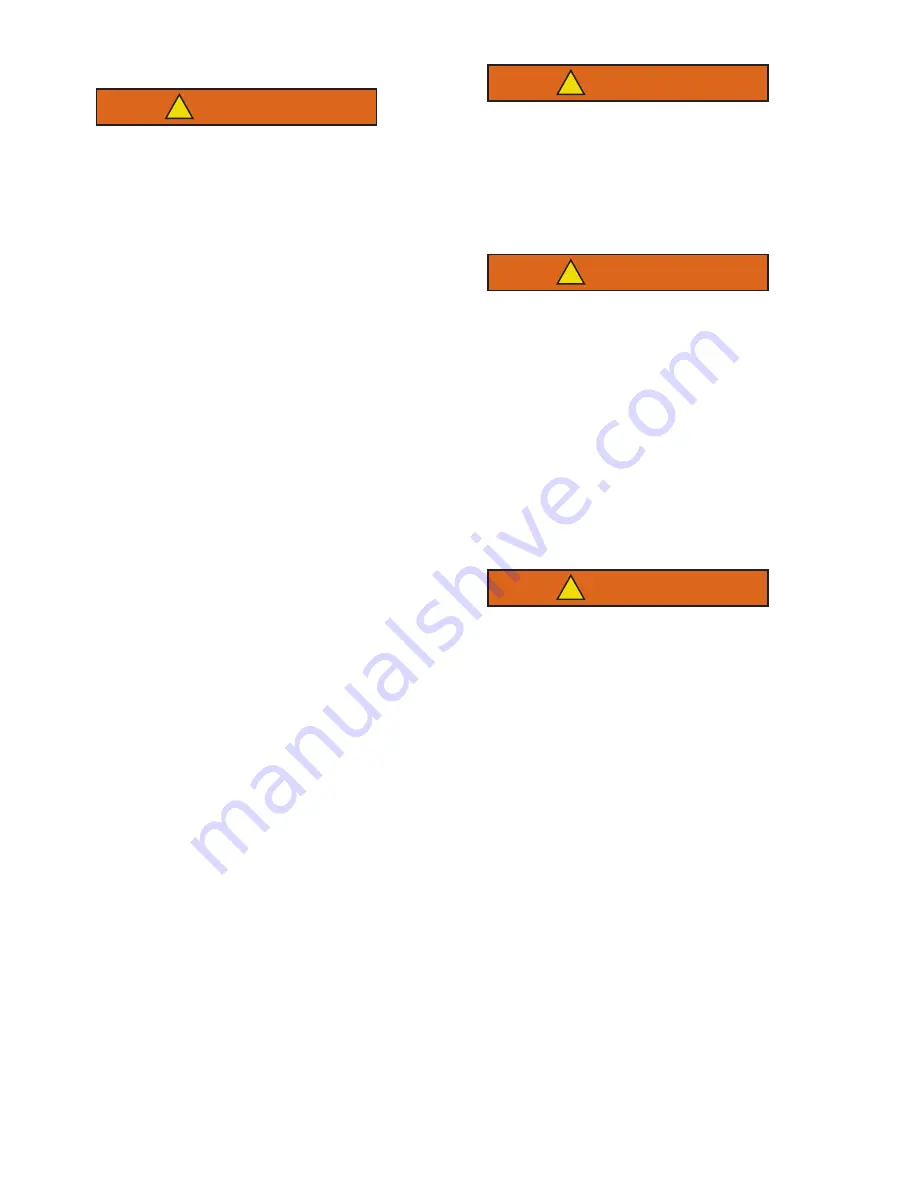
62-11640
8–18
8.6.3
Leak Checking
WARNING
!
Never use air or gases containing oxygen
for leak testing or operating refrigerant
compressors. Pressurized mixtures of air
or gases containing oxygen can lead to
explosion.
The condition that the system may be in when leak
checking is required include; when the system is
charged, when the system is without charge, when the
low side has been pumped down and when only the
compressor is to be leak checked. Procedures for each
condition are provided in the following subsections.
a. Leak Checking a Charged System
1. Ensure the unit will not start automatically by
disabling any two way communication and plac-
ing the STOP/RUN-OFF switch in the OFF posi-
tion. Disconnect the high voltage source and
lockout/tagout the receptacle.
NOTE
Service Mode is not required for this proce-
dure.
2. Verify that the suspected leak area (high side or
low side) has sufficient pressure (minimum 20
psig = 1.4 bar) to detect the leak. The larger the
leak the less pressure is required. The smaller
the leak, the greater the pressure required.
3. The recommended procedure for finding leaks
from a system is with an electronic leak detector.
Checking joints with soapsuds is satisfactory
only for locating large leaks, or pinpointing small
leaks once a general area has been located.
4. Some leaks may be repaired by simply tighten-
ing a connection. Others may require removal of
the charge, refer to
5. Start unit and run Pretrip to check operation.
b. Leak Checking a System Without Charge
The refrigeration system must be leak checked once it
is closed and all repairs complete.
1. Ensure the unit will not start automatically by
disabling any two way communication and plac-
ing the STOP/RUN-OFF switch in the OFF posi-
tion. Disconnect the high voltage source and
lockout/tagout the receptacle.
2. Connect refrigerant system equipment if not
already connected. Refer to
WARNING
!
Only a refrigerant cylinder containing
R404A should be connected to this refrig-
eration unit in order to pressurize the sys-
tem. However, dry nitrogen may be used to
increase pressure. Any other gas or vapor
will contaminate the system and require
additional removal and evacuation.
WARNING
!
Do not vapor charge R404A. Only liquid
charging through the liquid line service
valve is acceptable.
3. Ensure that the operator message panel dis-
plays “RECOVER/LEAK CHK/EVAC MODE”
during the pressurizing and leak checking pro-
cedures. (Refer to
.) If the control
system switches to Charge Mode during the
process, switch it back to the “RECOVER/LEAK
CHK/EVAC MODE”.
4. Pressurize the system 5 to 10 psig (0.3 to 0.7
bar) with refrigerant at the liquid line service
valve.
WARNING
!
Do not use a nitrogen cylinder without a
pressure regulator. Cylinder pressure is
approximately 2350 psig (159.9 bar). Do
not use oxygen in or near a refrigerant
system as an explosion may occur. (See
5. Connect a cylinder of dry nitrogen. Use the dry
nitrogen to increase the pressure as necessary
20 to 150 psig (1.4 to 10.2 bar) to detect the
leak. The larger the leak the less pressure is
required. The smaller the leak, the greater pres-
sure is required.
6. The recommended procedure for finding leaks
from a system is with an electronic leak detector.
Checking joints with soapsuds is satisfactory
only for locating large leaks, or pinpointing small
leaks once a general area has been located.
7. Once leak checking is complete, remove the
refrigerant/ nitrogen vapor out of the system.
8. If no leaks are found the system is ready for
evacuation. (Skip to Step 11)
9. If any leaks are found they must be repaired
before proceeding.
10. Repeat steps 4 thru 9 as necessary.
11. Evacuate the system after all leaks are repaired.
Refer to
Summary of Contents for Vector 8500
Page 23: ...62 11640 1 6 1 3 SAFETY DECALS ...
Page 24: ...1 7 62 11640 62 03958 ...
Page 25: ...62 11640 1 8 ...
Page 26: ...1 9 62 11640 ...
Page 27: ...62 11640 1 10 ...
Page 125: ...62 11640 SECTION 6 MESSAGECENTER PARAGRAPH NUMBER Page 6 1 MESSAGECENTER MESSAGES 6 1 ...
Page 321: ......
Page 322: ......