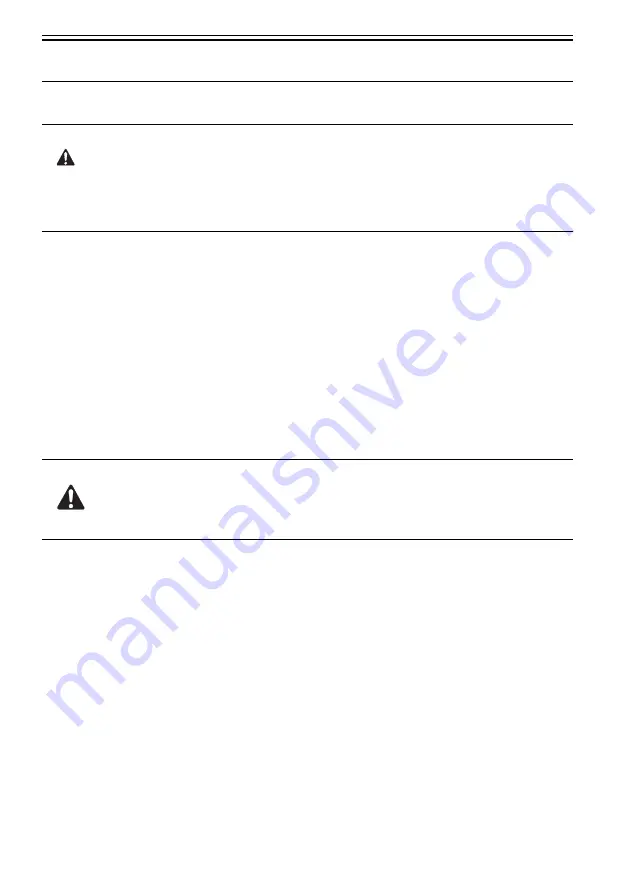
Chapter 15
15-4
15.3 Scheduled Servicing Basic Procedure
15.3.1 Scheduled Servicing Basic Procedure
- As a rule, provide scheduled servicing every 40,000 prints.
- Before paying a scheduled visit, check the Service Record, and take any parts likely to need replacement.
- If the machine's power plug remains connected to a wall outlet for a long time in a site where there is much
dust, moisture, or oil smoke, it can collect these elements and trigger insulation failure or fires. Be sure to
disconnect the power plug periodically and clean the plug and the area around it with a dry cloth.
Steps
1) Report to the person in charge.
Check the general condition.
2) Record the counter reading.
Check the faulty prints.
3) Make test prints.
(1) check the image density against standards
(2) check for soiling in the white background;
(3) check the clarity of characters;
(4) check the margin;
(5) check the fixing; check for poor registration and soiling on the back.
Standards on margin (single-sided)
leading edge: 2.5 mm +/-1.5 mm,
trailing edge: 2.5 mm +/-1.5 mm, left: 2.0 mm +/-1.5 mm
4) Waste Toner Colleting Container
If the waste toner collecting container is more than half full, dispose of the toner in a plastic bag; or, replace
the toner collecting container itself.
- Be sure to observe all rules and regulations of the governing community when disposing of waste toner.
- Do not dispose of waste toner into fire. (It may explode, causing a significant hazard.)
5) Clean the copyboard glass and the reader glass.
6) Make test copies.
7) Make sample copies.
Summary of Contents for Color imageRUNNER C5180 Series
Page 22: ...Chapter 1 INTRODUCTION...
Page 64: ...Chapter 2 INSTALLATION...
Page 110: ...Chapter 3 BASIC OPERATION...
Page 119: ...Chapter 4 BASIC OPERATIONS AS A PRINTER...
Page 129: ...Chapter 5 MAIN CONTROLLER...
Page 138: ...Chapter 5 5 8 F 5 8 CPU HDD ROM access to the program at time of execution...
Page 165: ...Chapter 6 ORIGINAL EXPOSURE SYSTEM...
Page 209: ...Chapter 7 IMAGE PROCESSING SYSTEM...
Page 212: ...Chapter LASER EXPOSURE 8...
Page 239: ...Chapter 9 IMAGE FORMATION...
Page 324: ...Chapter 10 PICKUP FEEDING SYSTEM...
Page 435: ...Chapter 11 FIXING SYSTEM...
Page 460: ...Chapter 11 11 23 F 11 13 SEN3 SEN2 SEN1 SEN2 SEN3 SEN1 SEN2 SEN3 SEN1...
Page 491: ...Chapter 12 EXTERNALS CONTROLS...
Page 498: ...Chapter 12 12 5 F 12 2 FM1 FM7 FM9 FM2 FM13 FM14 FM12 FM11 FM10 FM5 FM3 FM4 FM8 FM6...
Page 512: ...Chapter 12 12 19 2 Remove the check mark from SNMP Status Enabled F 12 10...
Page 553: ...Chapter 13 MEAP...
Page 557: ...Chapter 14 RDS...
Page 569: ...Chapter 15 MAINTENANCE INSPECTION...
Page 578: ...Chapter 16 STANDARDS ADJUSTMENTS...
Page 597: ...Chapter 17 CORRECTING FAULTY IMAGES...
Page 612: ...Chapter 17 17 14 F 17 7 PLG1 ELCB1 SP1 H4 H3 H2 H1 H1 H2 LA1...
Page 617: ...Chapter 18 SELF DIAGNOSIS...
Page 644: ...Chapter 19 SERVICE MODE...
Page 778: ...Chapter 20 UPGRADING...
Page 823: ...Chapter 21 SERVICE TOOLS...
Page 828: ...APPENDIX...
Page 851: ......