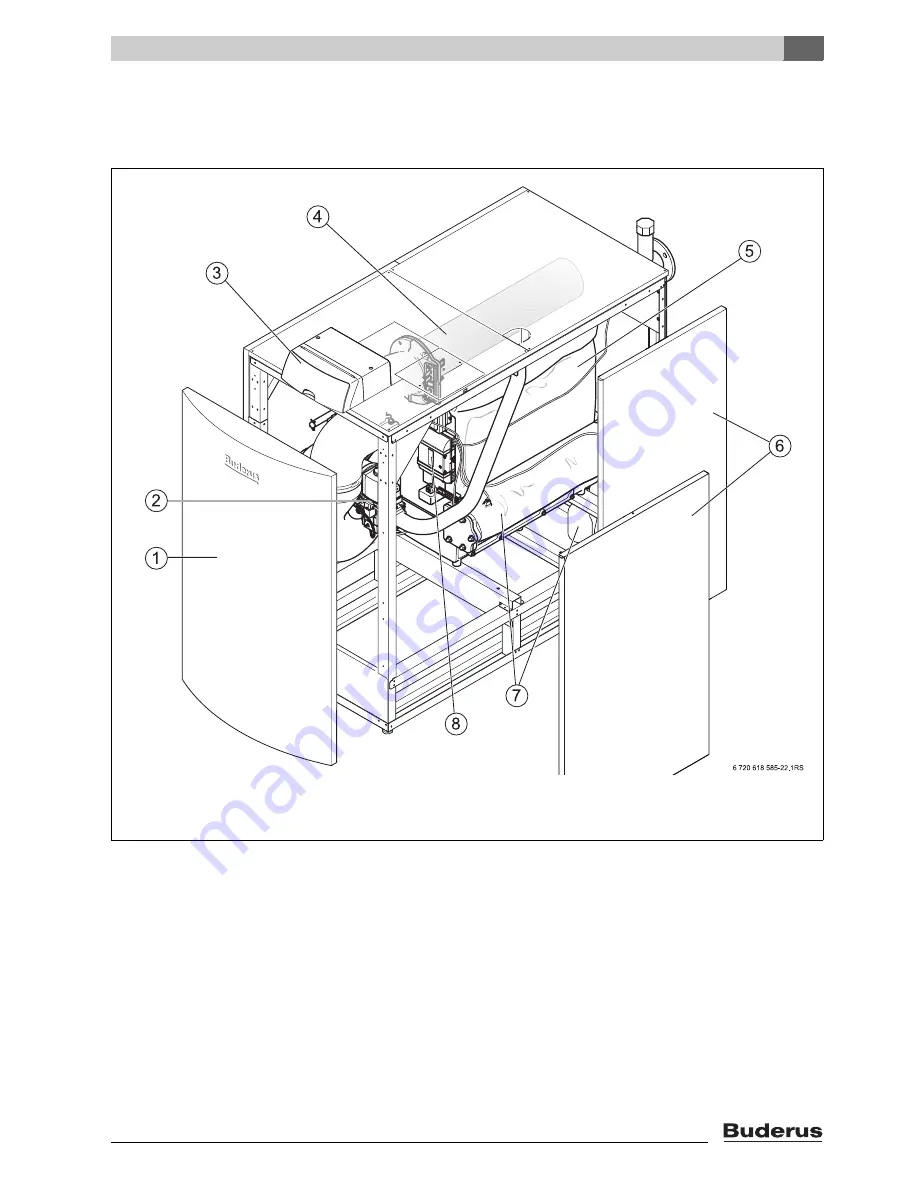
2
Information about the appliance
Logano plus GB402 - Subject to technical modifications!
7
2.5
Product description
The Logano plus GB402 is a gas condensing boiler with
an aluminium heat exchanger.
Fig. 1
Logano plus GB402 - main components
1
Boiler front panel
2
Gas valve
3
Control unit (MC10 and BC10)
4
Gas burner (burner rod)
5
Boiler block with thermal insulation
6
Boiler casing
7
Condensate tray and siphon
8
Burner control unit
The main components of the Logano plus GB402
(
Æ
Fig. 1) are:
• Control unit
• Appliance frame and casing
• Boiler block with thermal insulation
• Gas burner
The control unit monitors and controls all electrical boiler
components.
The boiler block transfers the heat generated by the
burner to the heating water. The thermal insulation
reduces the radiation and standby losses.