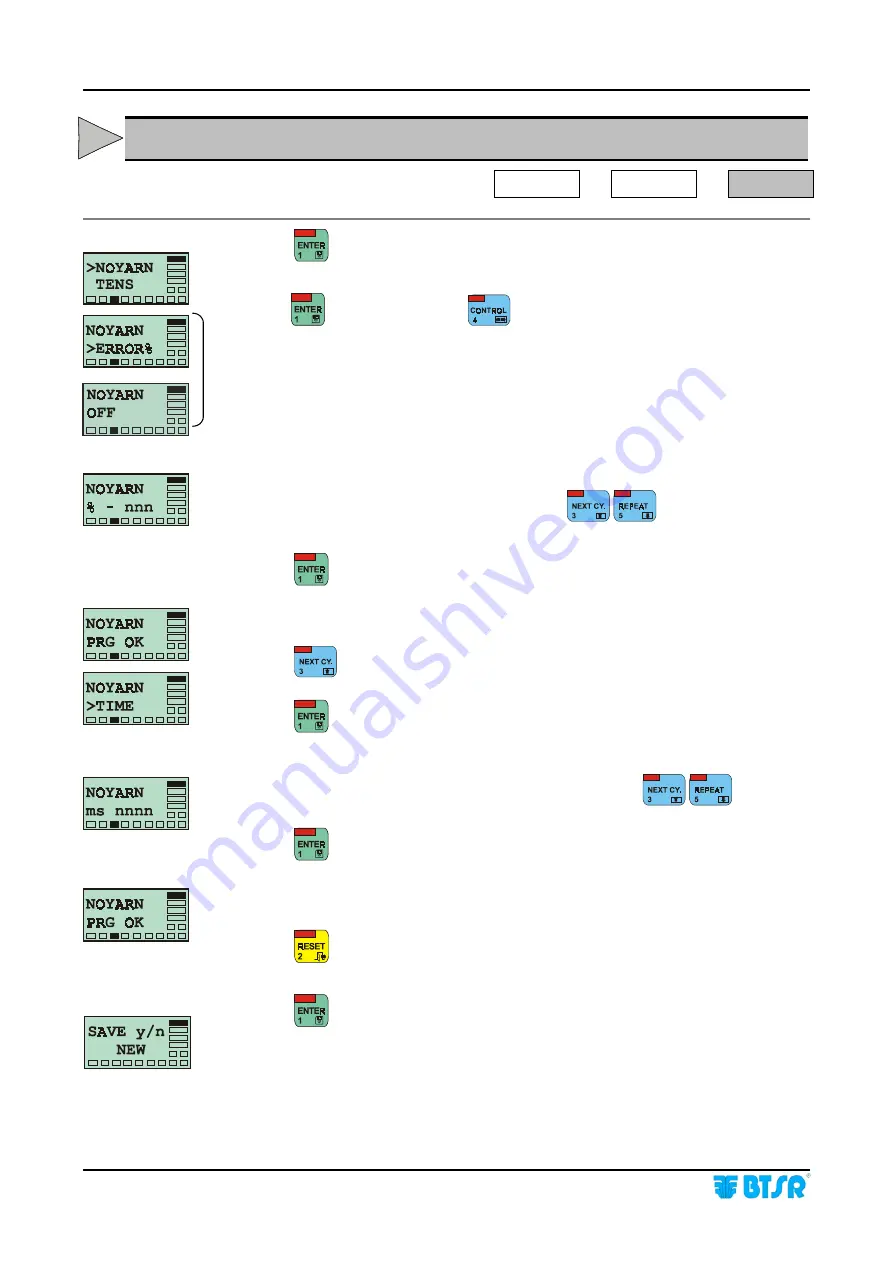
Operation
- 3.46 -
SMART 200 TSS
NOYARN - Creating a New Article
Characteristics of the Yarn Missing Failure
SETUP
#
#
#
#
NEW
#
#
#
#
NOYARN
Press
to have access to the function.
Press
to continue, or press
to disable/enable this parameter.
Set the increasing percentage with respect to the reference nominal tension
that shall be interpreted as yarn missing, using
.
[Default: -75%]
Press
to confirm the entered value.
This screen, displayed for a few seconds indicates that the previously set
parameter has been programmed correctly.
Press
to select the Minimum Duration of the Yarn Missing failure
(TIME)
.
Press
to continue.
Set the Minimum Duration of Yarn Missing failure, using
.
[Default: 10.0 ms]
Press
to continue.
This screen, displayed for a few seconds indicates that the Minimum Duration
parameter has been programmed correctly.
Press
once to return to the Article Parameters Menu, or two times to store all
parameters of the article and exit the Article Creation function.
Press
to save the Article into the data base.
B6
Summary of Contents for SMART 200 TSS
Page 1: ...SMART 200 TSS TS5 YARN CONTROL SYSTEM Operating Manual Rev 2 0 July 2003 ENGLISH ...
Page 8: ...Introduction I 4 SMART 200 TSS Page intentionally left blank ...
Page 16: ...Technical data and installation 2 6 SMART 200 TSS Page intentionally left blank ...
Page 22: ...Operation 3 6 SMART 200 TSS Technical Characteristics of TS5 sensor Sizes mm ...
Page 32: ...Operation 3 16 SMART 200 TSS Enabling the SETUP Menu Functions CONFIG ...
Page 34: ...Operation 3 18 SMART 200 TSS Enabling the GRAPH Menu Function ...
Page 74: ...Operation 3 58 SMART 200 TSS Production Report Example ...
Page 80: ...Troubleshooting and Maintenance 4 6 SMART 200 TSS Page intentionally left blank ...
Page 82: ...Appendix A Quick Reference Symbols Key A 2 SMART 200 TSS ...
Page 83: ...Appendix A Quick Reference Symbols Key SMART 200 TSS A 3 ...
Page 84: ...Appendix A Quick Reference Symbols Key A 4 SMART 200 TSS ...
Page 85: ...Appendix A Quick Reference Symbols Key SMART 200 TSS A 5 ...
Page 86: ...Appendix A Quick Reference Symbols Key A 6 SMART 200 TSS ...
Page 87: ...Appendix A Quick Reference Symbols Key SMART 200 TSS A 7 ...
Page 88: ...Appendix A Quick Reference Symbols Key A 8 SMART 200 TSS ...
Page 89: ...Appendix A Quick Reference Symbols Key SMART 200 TSS A 9 ...
Page 90: ...Appendix A Quick Reference Symbols Key A 10 SMART 200 TSS ...
Page 91: ...Appendix A Quick Reference SMART 200 TSS A 11 Note ...
Page 92: ...Appendix A Quick Reference A 12 SMART 200 TSS Page intentionally left blank ...