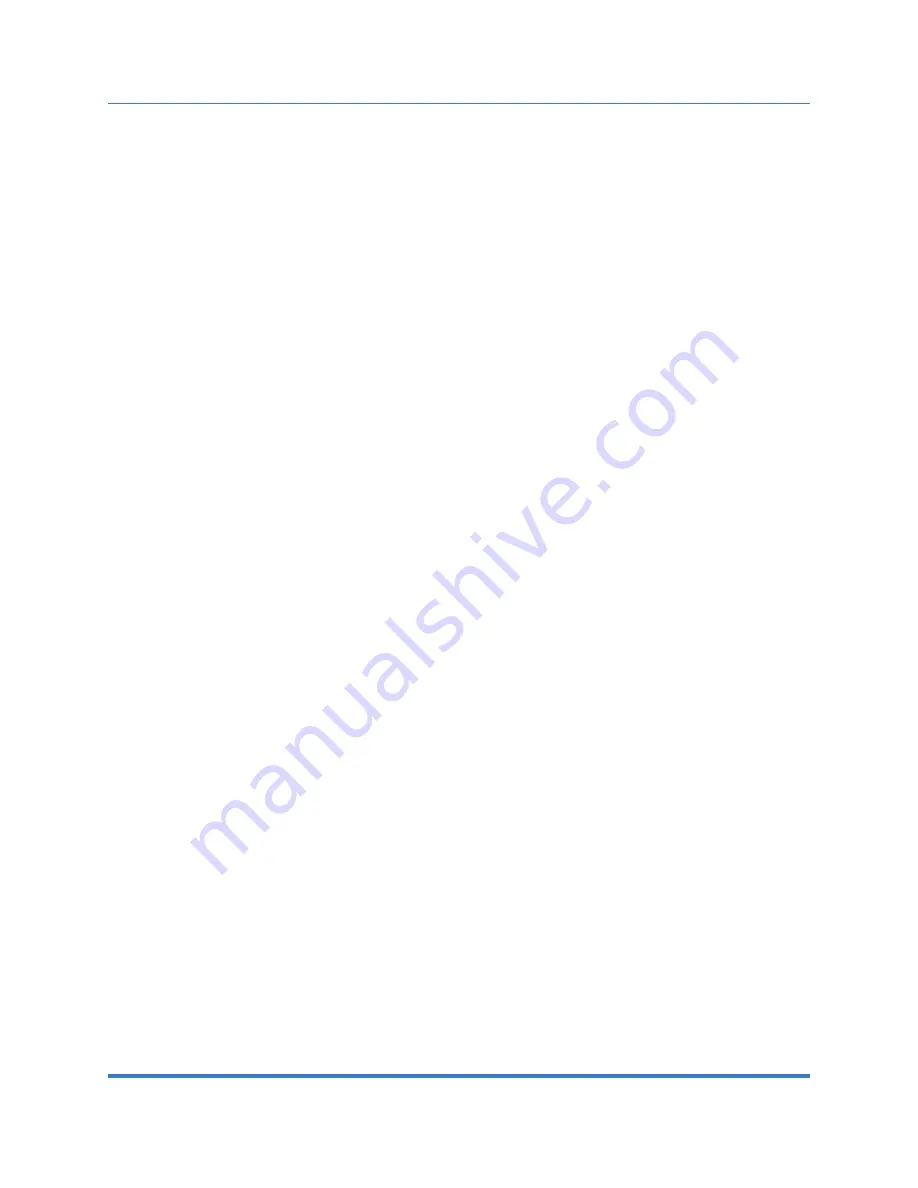
Installation Information
PreciseFlex™ DDR Collaborative Robots
P/N: PFD0-DI-00010, Rev 5.0.0, April 9, 2022
44
Copyright © 2022, Brooks Automation, Inc.
Mounting Instructions
PFDD robots must be attached to a rigid surface that can withstand lateral forces of 400 Newtons without
moving or vibrating. The robot base has an integrated bolting pattern to accommodate 4 M8 SHCS
mounting screws located as shown above.
Tool Mounting
PFDD Robots can be supplied with a light payload gripper with 23N of squeeze force for large workcells
in life sciences. Or a third-party electric gripper or pneumatic gripper may be attached by the end
user. The standard robot includes 2 1/8in OD pneumatic lines, however if pneumatic tooling is desired,
the robot must be ordered with one or two pneumatic valves installed. The outer link has a flange for
users to attach grippers or tooling.
To facilitate electrical interfacing to user tooling, digital I/O signals are available in the outer link. For
robots with an electric gripper, the electric gripper controller in the outer link has three extra inputs and
two extra outputs available for users. For 4-axis robots a slip ring is installed which routes 18 signals thru
the J4 pulley, or optionally pneumatic lines and hi-flex signal wires can be routed thru the
pulley. However, it should be noted that all the wires in the 18-conductor slip ring are consumed by the
electric gripper, although some of these wires can be configured to route serial or Ethernet signals,
depending on the slip ring model. For the 6-axis version wiring must be routed outside the robot
wrist. For robots without the electric gripper, one or two solenoid valves can be driven from either the J4
or J6 motor controller, which also provides 3 24V digital inputs.
Accessing the Robot Controller
Although most of the controller interface signals are exposed on the Facilities Panel at the base, there are
times when it may be necessary to access either the robot’s controller or its power supplies. To access
the robot main controller, the cover on the base must be removed by removing 6 M3 X 6 FHCS from the
base casting.
Other joint axis controllers are located in the following locations. Z axis and power supplies are located
on the Z column under the Z column rear cover. The J3 controller is located on the elbow under the light
tower cover. For the PFDD4 the J4 controller and servo gripper controller or solenoids are located in the
top of the outer link, under the foam cover and sheet metal cover. For the PFDD6 the J4 controller is
located inside the bottom of the J4 housing, which is covered by the J4 foam cover. The J5 and J6
controllers are located inside the J5 housing. Details on accessing these controllers can be found in the
service section.