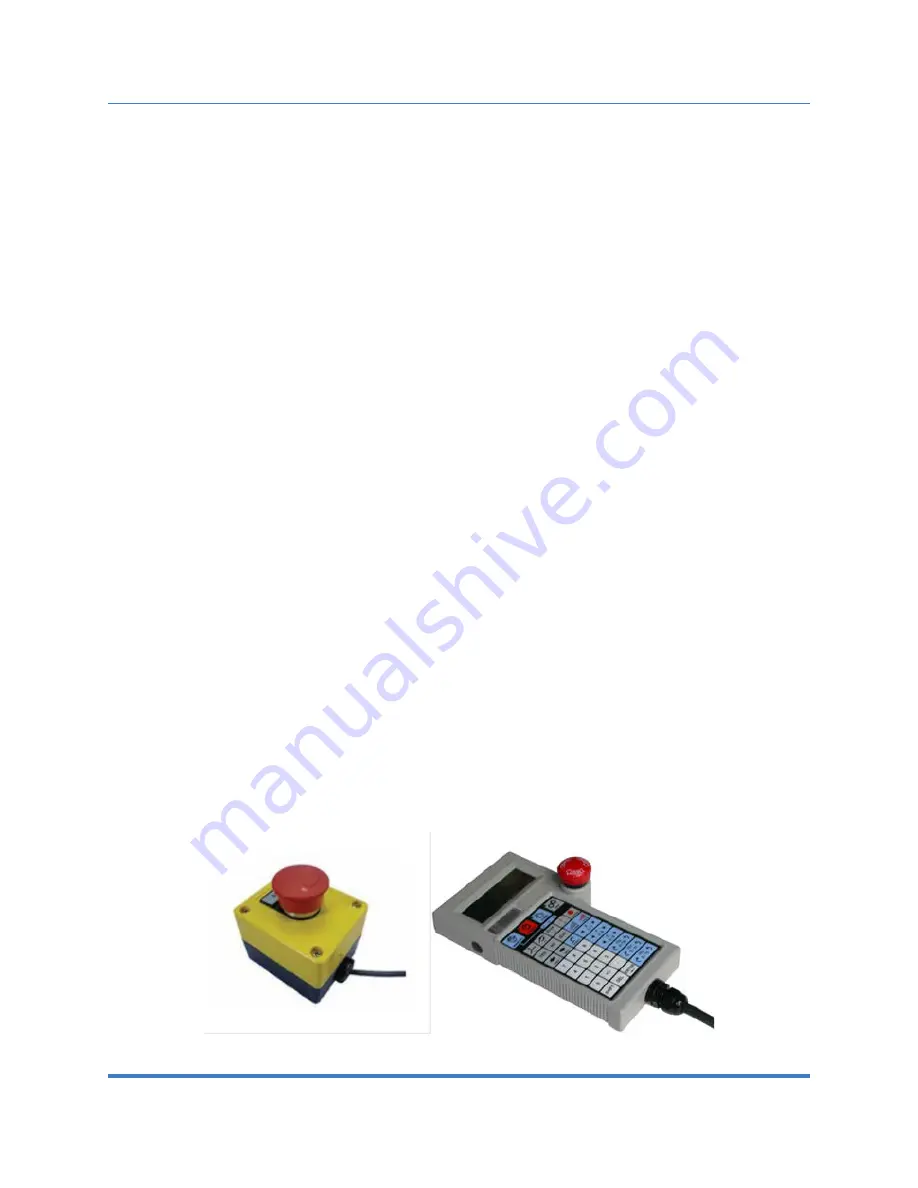
Introduction to the Hardware
PreciseFlex™ DDR Collaborative Robots
P/N: PFD0-DI-00010, Rev 5.0.0, April 9, 2022
16
Copyright © 2022, Brooks Automation, Inc.
protected against voltage surge to 2000 volts. Transient over voltage (< 50 µs) may not exceed 2000 V
phase to ground, as per EN61800-31996. The power supplies have over-current protection, and over-
voltage protection.
The robot consumes less than 500 Watts during normal operation. With the motor power turned off the
controller consumes about 20 Watts. With the motor power on and the Z brake released, the robot
consumes about 80 Watts. The PFDD6 running at 60% speed consumes about 150 Watts. These
numbers may be useful when mounting this robot on mobile platforms.
The Precise controller can monitor motor power through its datalogging function. Intermittent power
dropouts can be detected by setting a trigger in the data logger which can record and time-stamp power
fluctuations.
Energy Dump Circuit
The 48 VDC supply has a regulated output and an overvoltage protection circuit that is triggered if the
voltage reaches 60 volts. Rapid deceleration of the robot motors can generate a Back EMF voltage that
can pump up the motor voltage bus. In order to avoid bus pump up, an Energy Dump Circuit is included
in the base controller board and connected to the 48 VDC bus.
Remote Front Panel, E-Stop Box and Manual Control Pendant
For users that wish to have a hardware E-Stop button, Precise offers an E-Stop Box or a portable
Hardware Manual Control Pendant that includes an E-Stop button. The E-Stop box can be plugged into
the 9 pin D-Sub connector in the connector panel in the base casting. The E-Stop box completes a circuit
from Pin 1 (Estop 1) to Pin 6 (FE Out 1) and from Pin 2 (Estop 2) to Pin 7 (FE Out2) in this connector. If
this circuit is not completed it is not possible to enable motor power to the robot. The FE Out signals
allow each Estop circuit to be toggled during the CAT3 startup sequence to make sure both circuits are
working. If no E-Stop box or Manual Control Pendant is connected, jumpers must be connected between
these four pins to enable robot motor power. For those applications where an operator must be inside the
working volume of the robot while teaching, a second teach pendant with a 3-position run hold switch is
available. The Manual Control Pendants can be plugged directly into the 9 pin Dsub connector mounted
on the robot's Facilities Panel in the base of the robot.