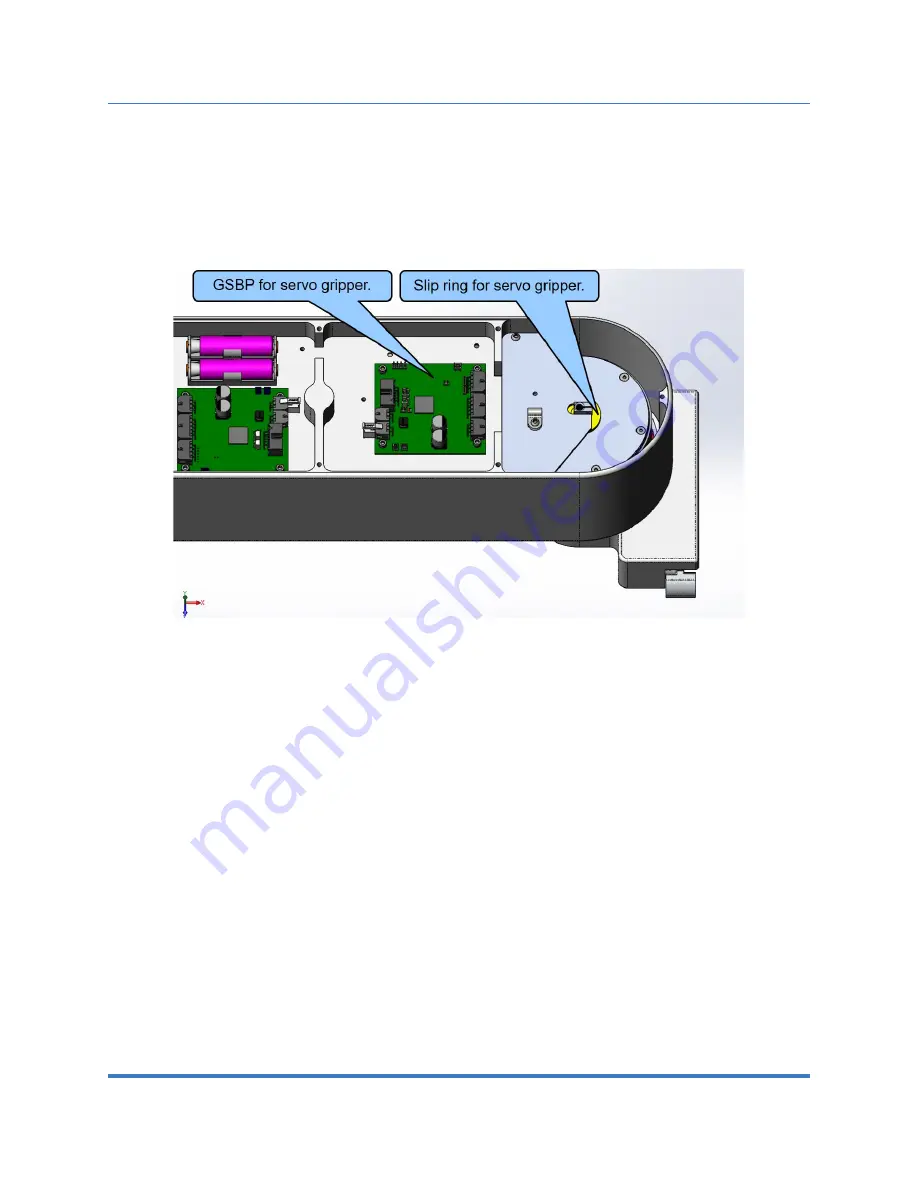
Gripper Support
PreciseFlex™ DDR Collaborative Robots
P/N: PFD0-DI-00010, Rev 5.0.0, April 9, 2022
88
Copyright © 2022, Brooks Automation, Inc.
For the PFDD4 with the 23N servo gripper option, the solenoid(s) are replaced by an additional GSBP
controller for the servo gripper, which is connected through a slip ring.
For applications with heavier payloads where an electric gripper is preferred to a pneumatic gripper, there
are third-party electric grippers available which can be attached to the ISO flange with a bracket. Some
of these are similar in performance to a pneumatic gripper; they have a limited travel of 6-12mm, are
powered by 24VDC, and toggled open or closed by a digital signal. For example, the Schunk Co-act
EGP 64 has 4 grip force settings, 65N, 110N, 170N, and 230N, runs on 24V, max 2A, and can
accommodate fingers up to 50mm in length. This gripper can be interfaced to the J4 GSBP controller by
using the IO connector on the J4 or J6 GSBP for 24VDC, Gnd, Digital Output 1 and Digital Output 2 to
open and close the gripper. The EMI MPPM3210 gripper is similar but only requires a single digital
output. The IO connector can supply a maximum of 2.5A for 24VDC. Contact Precise applications for
application notes on interfacing these grippers.
For the PFDD6, the access to the solenoids and J6 GSBP controller is under the foam side cover, which
is attached with Velcro. The side cover can be easily removed, and pneumatic lines attached to one or
both solenoid valves, then routed out through the harness bracket and hole in the foam side cover. In this
case the address to toggle the valve is 600013, as the valve is controlled from the J6 controller.
In a similar manner to the 4-axis robot, simple electric grippers can be attached to the output flange of the
6-axis robot, by plugging into the DIO connector.