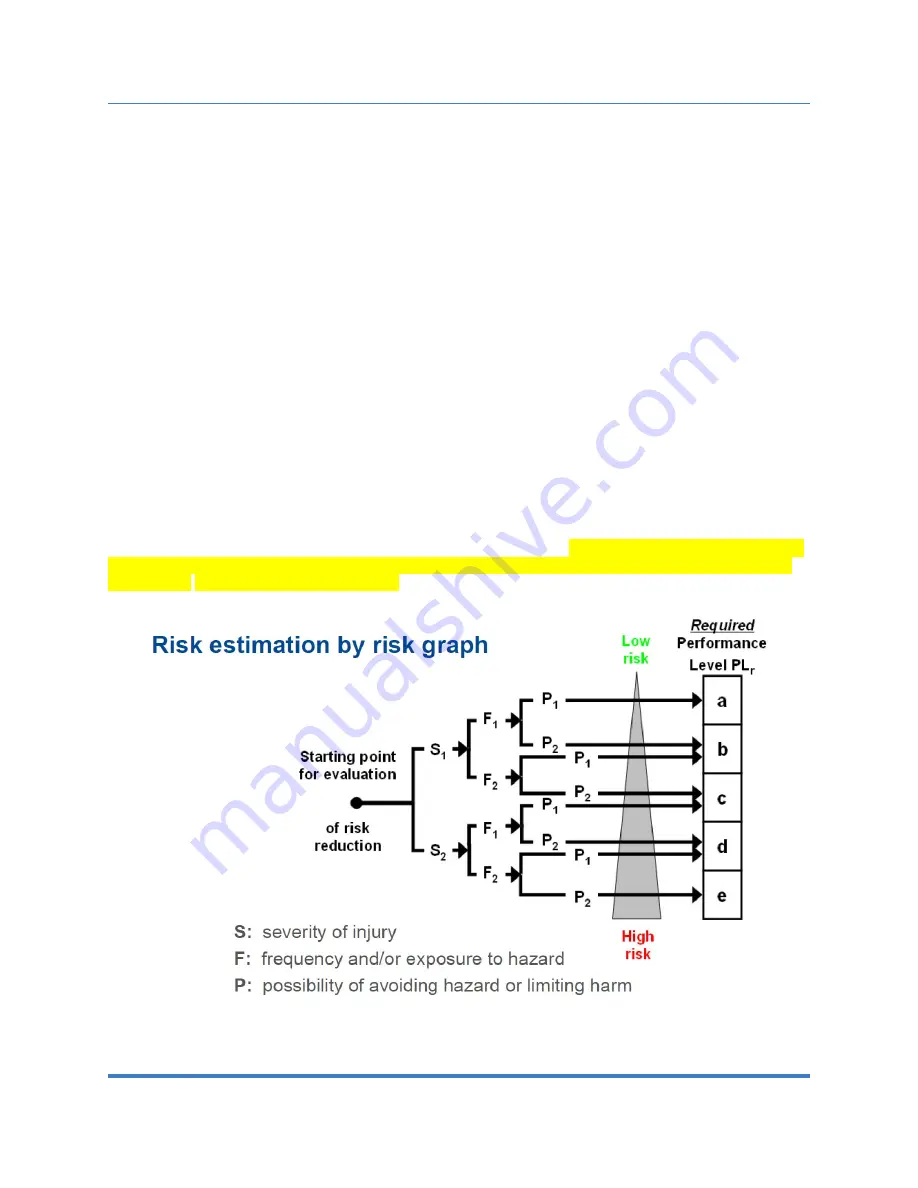
Collaborative Robot Safety
PreciseFlex™ DDR Collaborative Robots
P/N: PFD0-DI-00010, Rev 5.0.0, April 9, 2022
22
Copyright © 2022, Brooks Automation, Inc.
One of the requirements listed as sufficient to meet the 10218:1:2011 standard is:
5.10.5 Power and force limiting by inherent design or control
“The power or force limiting function of the robot shall be in compliance with 5.4. If any parameter limit is
exceeded, a protective stop shall be issued.”
Section 5.4 requires the system designer to perform a Performance Level (PL) or Safety Integrity Level
requirement
(SIL) check based on the robot AND the application tooling and workcell. For example, a
safe robot may still need safety interlock screening if it is moving a dangerous tool. This requires the
application designer to review the requirements of 10218-2:2011 which addresses robots in workcells.
Determining a Machine’s Required Performance Level (PLr).
ISO 13849-1:2006 Annex A
provides tables and a worksheet to identify a machine’s Required
Performance Level requirements. Figure 1 below shows a flow chart for determining Performance
Levels. Briefly these are: Select S1 for slight injuries (normally reversible) and S2 for serious injuries or
death. Select F1 for infrequent exposure to a hazard (for example only from time to time) and F2 for
frequent exposure (for example continuously entering workcell). Select P1 for easily recognizing and
avoiding a hazard (for example a repetitive motion) and P2 for a hazard that may be difficult to avoid (for
example a sudden, non-repetitive motion that may trap an operator). An example of determining PL for a
PFDDR workcell is given in Appendix A of this section, where it is shown that a PL of “b” is sufficient for
the workcell. UPPDATE with DDR example.
Figure 1