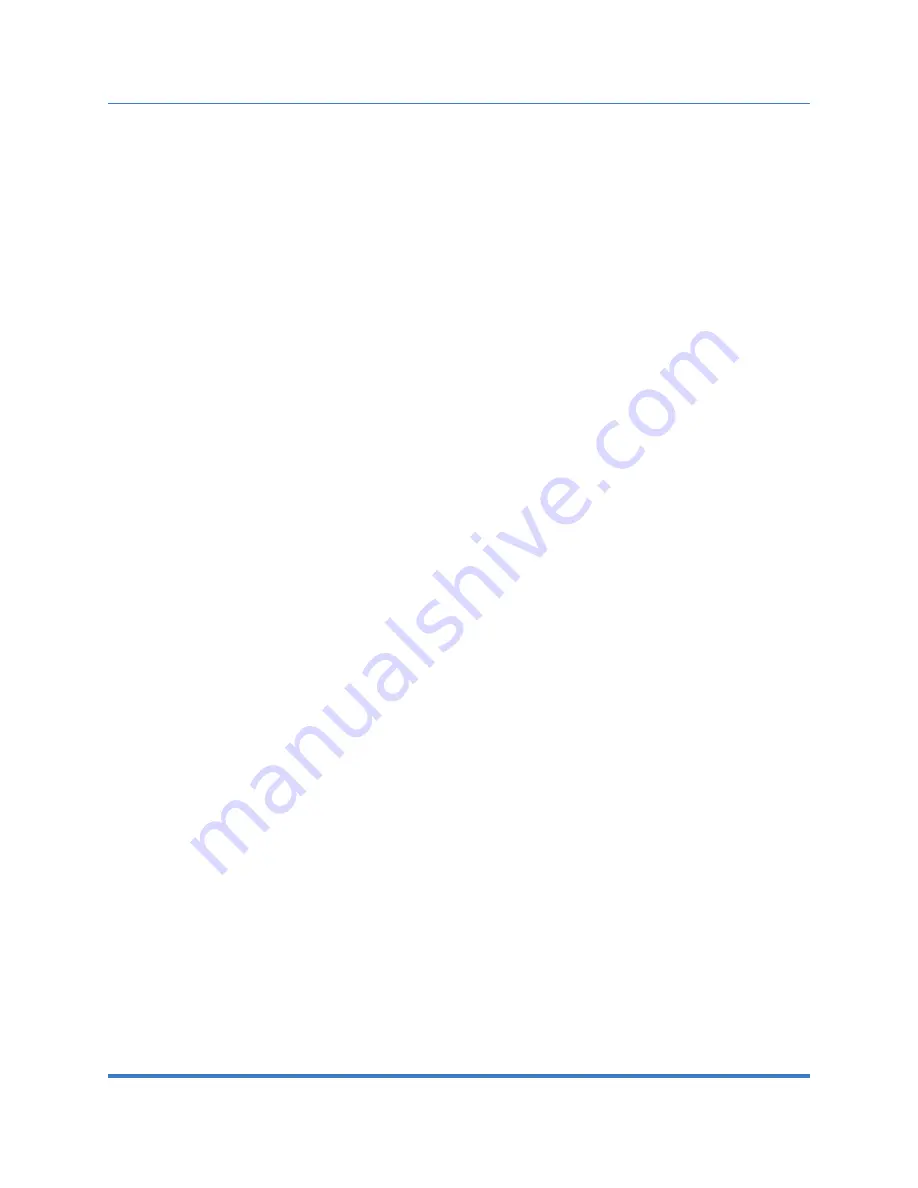
Brooks Automation
P/N: PFD0-DI-00010, Rev 5.0.0, April 9, 2022
Hardware Reference
Copyright © 2022, Brooks Automation, Inc.
46
Hardware Reference
System Schematics
System Diagram and Power Supplies
The robot has a 24VDC and 48VDC power supply located in the Z column. The power supplies have
both over-current and over-voltage protection and are CSA, UL, and CE certified. The robot controller
and electric gripper are powered by the 24VDC supply. The main robot motors are powered by the
48VDC supply. The 48VDC supply is protected against over voltage bus pump up by an energy dump
circuit, which connects a 75-Watt dump resistor located in the base housing across the 48VDC supply
output when the voltage reaches 56 volts, and disconnects the dump resistor when the voltage drops to
52 volts. This protects the power supply during high speed motor deceleration when the motor generates
Back EMF voltage that adds to the power supply voltage.
DC power is routed from the power supplies to the controllers through a ribbon cable which also contains
3 twisted pairs for RS485 (1 pair) and 100 BaseT Ethernet (2 pairs).
Twelve digital input and eight digital output signals from the main robot controller are available in the
25pin Dsub on the connector panel in the base. The 12 digital output signals can be individually
configured as either sourcing or sinking by software settings in the Web Interface. The 8 digital input
signals can be configured as either sourcing or sinking individually and the 12 digital inputs can be
configured as sourcing or sinking in blocks of 4 by software settings in the Web Interface. See section on
IO.
It is necessary to wire an Emergency Stop Button to the controller. This button may be wired in series with
other emergency stop contacts. The E-stop signals are available in the Manual Control Pendant 9-pin
DSub connector that is mounted on the Facilities Panel. Please see the Hardware Reference section of
this manual for detailed information on the E-Stop signals. The robot is shipped with a jumper that
completes the dual ESTOP circuits.
The cable from the brake release button under the Shoulder plugs into the amplifier board for the Z axis
motor on the back of the Z column. This button provides a ground return from the Z column brake to
ground bypassing the transistor that performs this function under computer power so that the brake can
be released manually without motor power being enabled, as long as 24VDC is turned on. Care should
be taken to support the links of the robot when this button is pushed as the links weigh 14kg and will drop
under gravity when this button is pushed.