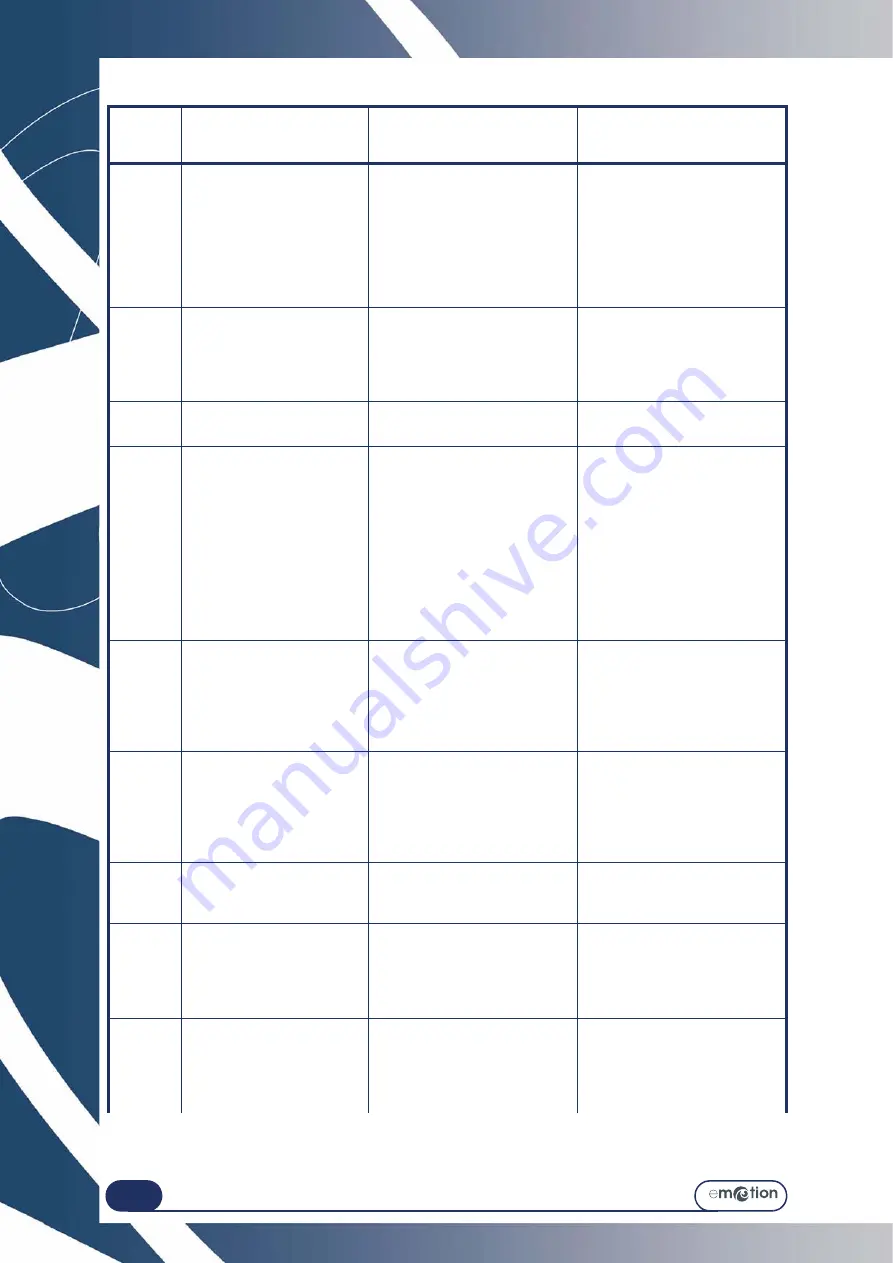
Maintenance...
Messages
5-190
0x25
Incompatible edger
configuration.
Safety-bevel to be defined
not allowed.
The job you have loaded has the
parameter Safety-bevel to be
defined.
In the personalisation menus,
you have excluded this
parameter.
Therefore the edger cannot
accept this job.
Confirm the message.
If you wish to load this job
nonetheless, change the
personalisation of the pull-down
menus.
Select the Safety-bevel to be
defined parameter.
Load the job again.
0x26
Retouch impossible on
drilled or grooved lens.
You wish to undertake a retouch
on a lens which has been drilled
or grooved. This operation is
impossible on a lens with these
finishes.
Carry out the lens size
adjustment procedure. Fit a new
lens and enter a negative
oversize value.
0x2B
Wrong job received.
Problems of communication with
the server have been detected.
Load another job number
0x30
Do you want to save the
new personalisation?
At least one of the parameters
of the menus personalisation
has changed. The machine
requests confirmation of this
modification.
Confirm: the new
personalisation is registered.
No confirmation: the new
personalisation is not registered.
The previous personalisation is
retained.
Cancel: you return to the
personalisation screen for the
menu-button concerned.
Reselect the elements you wish
to display.
0x34
Groove too near front.
The distance between the front
face of the lens and the external
edge of the groove is less than
0.2 mm.
Confirm the message.
Select Manual Groove sub-
finishing.
Visualise the position of the
groove on the control screen.
Reposition the groove.
0x35
Groove too far back.
The distance between the rear
face of the lens and the internal
edge of the groove is less than
0.2 mm.
Confirm the message.
Select Manual Groove sub-
finishing.
Visualise the position of the
groove on the control screen.
Reposition the groove.
0x100
Requested job does not
exist.
You have called up a job number
but the corresponding job is not
on the server.
Call up another number.
0x101
No response from server
within time limit.
You have tried to load a job but
the edger has not received a
signal from the server.
Check that:
- The server is switched on.
- The OMA cord is correctly
connected to both terminals.
Then load the job again.
0x102
The server is switched off.
The OMA cord is disconnected.
OR
The server is switched off.
Check that:
- The server is switched on.
- The OMA cord is correctly
connected to both terminals.
Then load the job again.
#
Message
Condition(s) for
display
Action(s)
Summary of Contents for emotion
Page 1: ...Operation manual...
Page 3: ......
Page 9: ...Table of contents...
Page 10: ...REVISION FOLLOW UP Revision 01 Page New Modified Item New document...
Page 11: ...3 10...
Page 12: ...1 INSTALLATION...
Page 15: ...Installation Unpacking the machine 1 14...
Page 17: ...Installation Removing the shipping rails 1 16...
Page 23: ...Installation Water connections 1 22...
Page 25: ...Installation Electrical connections 1 24 1 3 2...
Page 28: ...2 SAFETY PRECAUTIONS...
Page 29: ...2 28...
Page 31: ...Safety precautions Safety 2 30...
Page 33: ...2 32 Safety precautions Recommendations...
Page 34: ...3 USING YOUR EDGER...
Page 35: ...3 34...
Page 41: ...3 40...
Page 45: ...Using your Edger General principles of use 3 44 Pin 1 2 3 5 Blocker head Blocker arm 4...
Page 51: ...Using your Edger General principles of use 3 50...
Page 75: ...Using your Edger Special cases 3 74...
Page 87: ...Using your Edger Special cases 3 86...
Page 94: ...4 CONFIGURATION...
Page 95: ...4 94...
Page 102: ...Configuration Configuration of finishing parameters default values 4 101...
Page 107: ...Configuration Correction of frame and lens values 4 106...
Page 112: ...5 MAINTENANCE...
Page 113: ...5 112...
Page 117: ...Maintenance Visualising the components 5 116...
Page 119: ...Maintenance Task list 5 118...
Page 121: ...Maintenance Maintenance of the touch screen unit 5 120 Illustration 5 1 Scanform...
Page 124: ...Maintenance Maintenance of the Scanform unit 5 123...
Page 125: ...Maintenance Maintenance of the Scanform unit 5 124 Illustration 5 1 Centering blocking system...
Page 131: ...Maintenance Regular maintenance of the edger 5 130...
Page 135: ...Maintenance Regular maintenance of the edger 5 134...
Page 147: ...Maintenance Regular maintenance of the edger 5 146...
Page 149: ...Maintenance Handling the covers 5 148...
Page 151: ...Maintenance Preventive maintenance 5 150...
Page 156: ...Maintenance Adjustments 5 155...
Page 157: ...Maintenance Adjustments 5 156 Screen 5 4 Feeling adjustment...
Page 159: ...Maintenance Adjustments 5 158 Screen 5 5 Adjusting the sizes Screen 1...
Page 163: ...Maintenance Adjustments 5 162 Screen 5 6 Adjustment of the flush of the mill bit...
Page 165: ...Maintenance Adjustments 5 164 Screen 5 7 Adjustment of the touch screen...
Page 167: ...Maintenance Adjustments 5 166 Screen 5 8 Example of a setting values display screen...
Page 169: ...Maintenance Adjustments 5 168...
Page 173: ...Maintenance Consulting the statistics 5 172...
Page 196: ...6 TESTS...
Page 197: ...6 196...
Page 203: ...Tests Operating principle 6 202...
Page 204: ...7 TECHNICAL SPECIFICATIONS...
Page 205: ...7 212...
Page 209: ...Technical specifications Technical specifications 7 216...
Page 210: ...2 rue Roger Bonnet 27340 PONT DE L ARCHE FRANCE Tel 33 02 32 98 91 32 Fax 33 02 35 02 02 94...