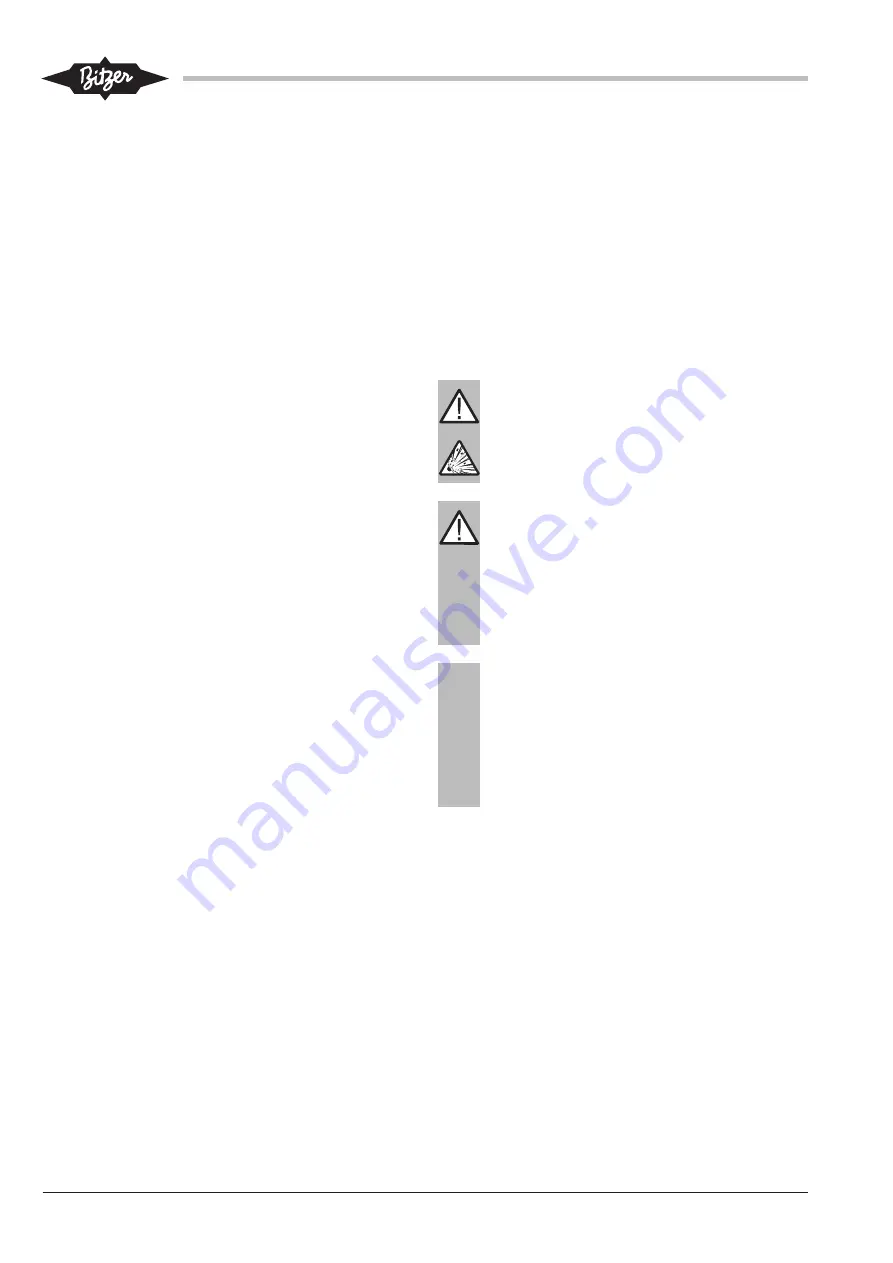
SB-160-3
18
5.2
Safety and protection devices
5.2.1
Pressure switch (HP + LP)
A high pressure limiter at the connection position 1
(HP) is necessary in order to secure the compressor on
top of monitoring the application limits of the FI control
so that any unacceptable operating conditions can be
avoided, see Technical Information ST-160, chapter
Pressure switch (F5 and F6).
A low pressure limiter at the connection position 3 (LP)
is not necessary, depending on local regulations.
Connection positions on the compressor see chapter
Connections and dimensional drawings, page 13.
Never connect the pressure switch to the lockable
maintenance connection of the shut-off valve! Observe
the local regulations.
5.2.2
Integrated sensors
The following sensors are integrated into the FI control:
• Low pressure transmitter
• High pressure transmitter
• Motor temperature (NTC)
• Oil temperature sensor (NTC)
• Opto-electronic oil level switch for the minimum oil
level (OLC-D1-S)
• Multiple temperature sensors for FI monitoring
The FI control also monitors:
• Cycling rate of the compressor
• FI voltage supply
The control logic analyses the signals from the sensors
and reports critical operating conditions to the system
controller. It automatically adapts the V
i
control to the
particular operating condition and activates the oil
heater. However, if a critical operating condition is
reached, the FI control switches the compressor auto-
matically off. For further information, see Technical In-
formation ST-160, chapter Protective functions.
5.2.3
Oil heater
The oil heater is placed in the bottom left edge of the FI
housing. It is mounted, wired and integrated ex-factory
into the FI control. If needed, the control activates or
deactivates the oil heater. No further compressor heat-
ing is needed.
5.2.4
Insulting the oil separator
Operating at low ambient temperatures or with high
temperatures on the high-pressure side during stand-
still (e.g. for heat pumps) requires additional insulation
of the oil separator.
6
Commissioning
The compressor has been carefully dried, checked for
tightness and filled with a holding charge (N
2
) before
leaving the factory.
DANGER
Risk of explosion!
Never pressurize the compressor with oxygen
(O
2
) or other industrial gases!
WARNING
Risk of bursting!
A critical shift of the refrigerant ignition limit is
possible in case of excess pressure.
Do not add a refrigerant (e.g. as a leak indic-
ator) to the test gas (N
2
or air).
Environmental pollution in case of leakage and
when deflating!
!
!
NOTICE
Risk of oil oxidation!
Check the entire system for strength pressure
and tightness, preferably using dried nitrogen
(N
2
).
When using dried air: Remove the compressor
from the circuit – make sure to keep the shut-off
valves closed.
6.1
Checking the strength pressure
Check the refrigerant circuit (assembly) according to
EN378-2 (or other applicable equivalent safety stand-
ards). The compressor had been already tested in the
factory for strength pressure. A tightness test is there-
fore sufficient, see chapter Checking tightness, page
19. If you still wish to perform a strength pressure test
for the entire assembly: