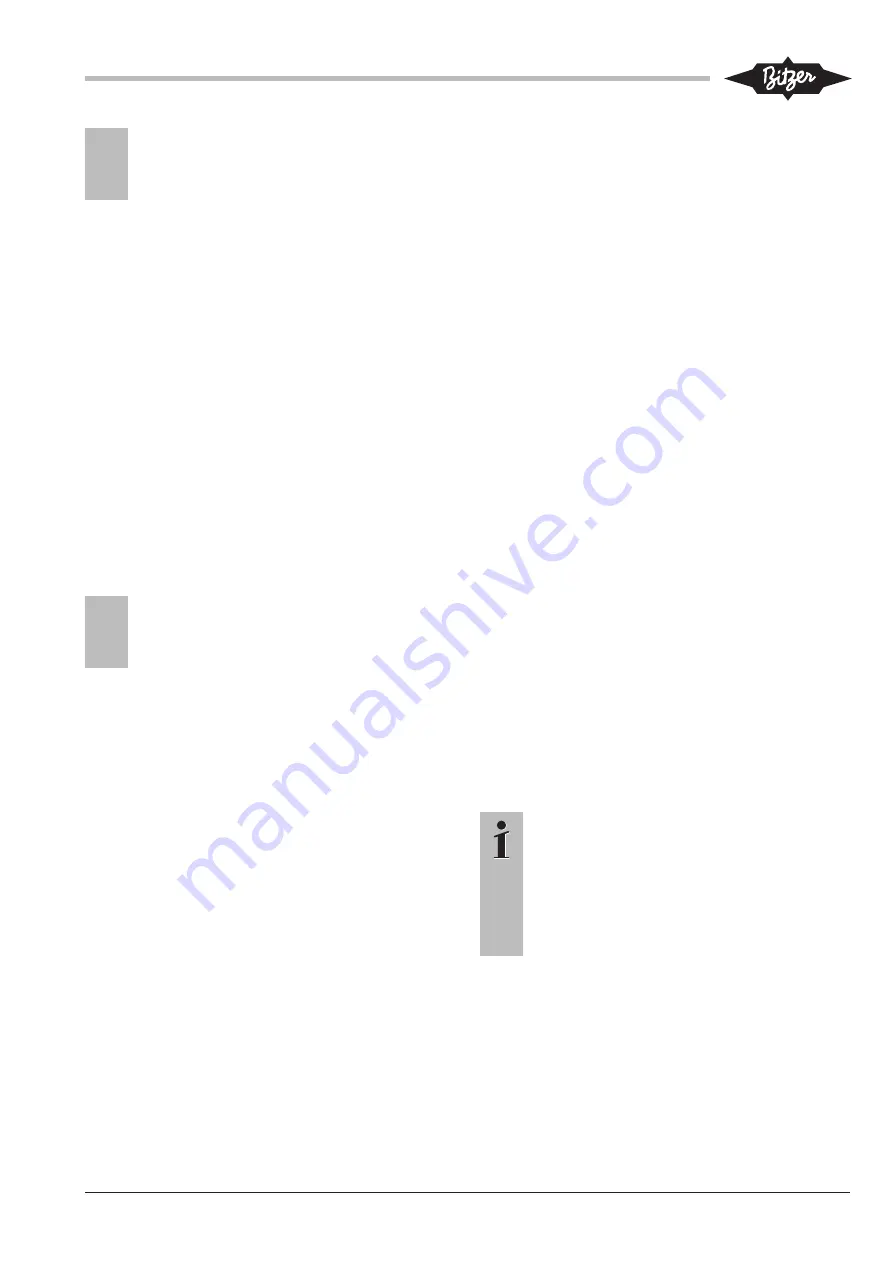
SB-160-3
21
!
!
NOTICE
Risk of motor failure!
The specified requirements must be ensured by
the control logic!
• Desirable minimum running time: 5 minutes!
• Reduce the cycling rate after commissioning as
much as possible. See ST-160.
6.6.6
Vibrations and frequencies
Check the system over the complete speed range to
detect any abnormal vibrations
The pulse frequency of the gas column in the discharge
gas line and the excitation frequency on the com-
pressor feet and on the pipes vary depending on the
compressor speed. This may lead to resonance effects
in the pipes and in other system components.
Check the complete system very carefully to detect any
abnormal vibration; check particularly pipelines and ca-
pillary tubes. If strong vibrations occur, take mechanical
measures: For example, mount pipe clips or insert vi-
bration dampers.
!
!
NOTICE
Risk of burst pipes and leakages on the com-
pressor and system components!
Avoid strong vibrations!
During operation as well, repeatedly check for any ab-
normal vibration.
Skip speeds that still lead to resonances in the pro-
gramming of the frequency inverter. See ST-160.
6.6.7
Particular notes on safe compressor and
system operation
Analysis show that compressor failures are most often
due to an inadmissible operating mode. This applies
especially to damage resulting from lack of lubrication:
• Function of the expansion valve – observe the manu-
facturer’s notes!
– Position the temperature sensor correctly at the
suction gas line and fasten it.
– When using a liquid suction line heat exchanger:
Position the sensor as usual after the evaporator
– in no case after the heat exchanger.
– Ensure sufficiently high suction gas superheat,
while also taking into account the minimum dis-
charge gas temperatures.
– Stable operating mode under all operating and
load conditions (also part-load, summer/winter op-
eration).
– Solid liquid at the expansion valve inlet, during
ECO operation already before entering the liquid
subcooler.
• Avoid refrigerant migration from the high pressure
side to the low pressure side or into the compressor
during long shut-off periods!
– The compressor must always be supplied with
voltage even during a standstill so that the oil
heater remains in operation. This is valid for all
applications.
When installing the system in zones where the
temperatures are low, it may be necessary to in-
sulate the oil separator. At compressor start, the
oil temperature, measured under the oil sight
glass, should be 15 .. 20 K above the ambient
temperature.
– Automatic sequence change for systems with sev-
eral refrigerating circuits (approximately every 2
hours).
– Mount an additional check valve in the discharge
gas line if no temperature and pressure compens-
ation is reached even after long standstill times.
– If needed, mount a time and pressure-dependant
controlled pump down system or liquid separators
on the suction side – particularly for high refriger-
ant charges and/or when the evaporator may be-
come hotter than the suction gas line or the com-
pressor.
• For further information about pipe layout, see
manual SH-170.
Information
In the case of refrigerants with low isentropic ex-
ponent (e.g. R134a), a heat exchanger between
the suction gas line and the liquid line may have
a positive effect on the system's operating mode
and coefficient of performance.
Arrange the temperature sensor of the expan-
sion valve as described above.