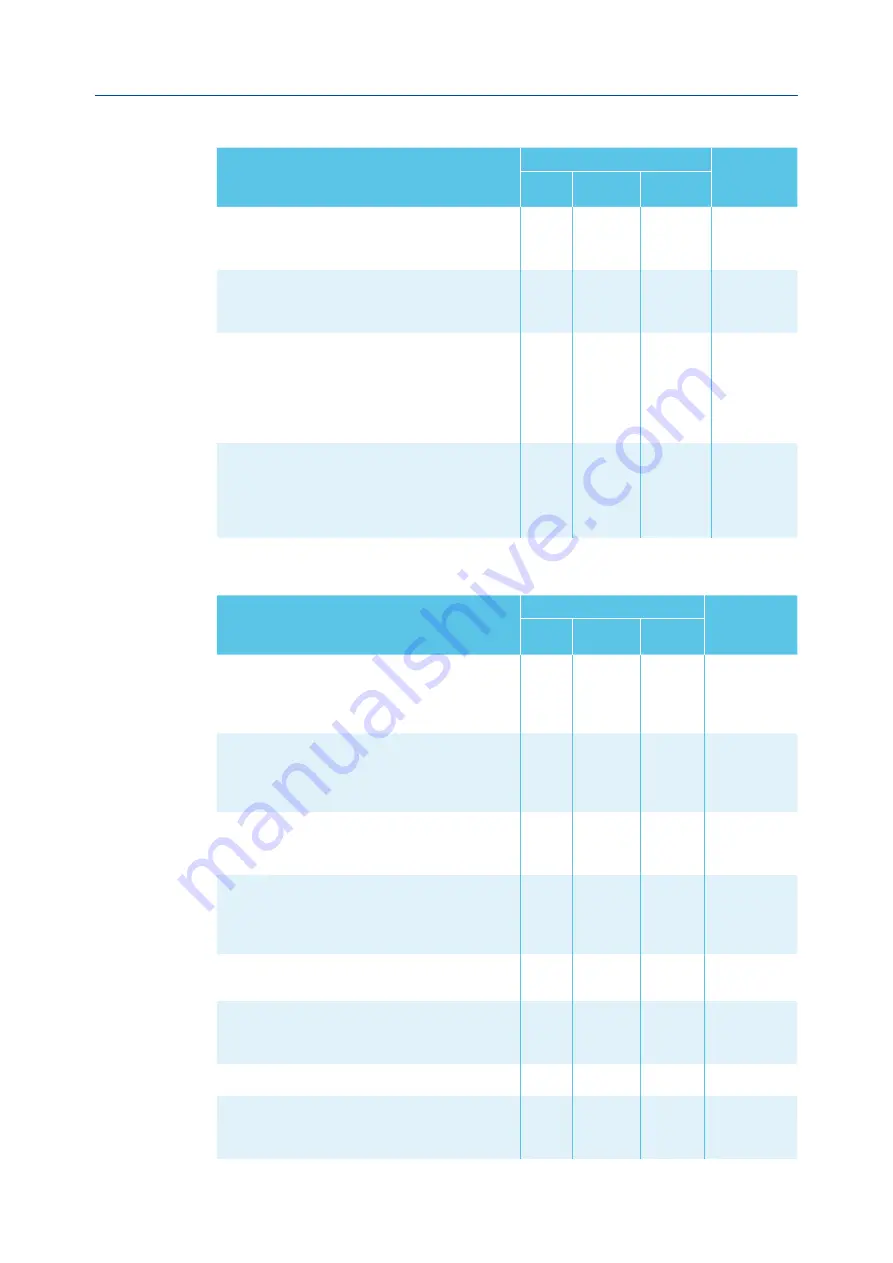
September 2021
Installation, Operation and Maintenance Manual
VCIOM-01249-EN Rev. 0
104
Troubleshooting
Section 12: Troubleshooting
Available controls
Display
message
Condition for alarm
Action
Local
Remote
ESD
Alarm reset
Configuration
error
The checksum of the
EEPROM memory that
contains the configuration
data is wrong
Reconfigure all
parameters
Not
available
Not available
Not available Memory OK
HW error
The diagnostic program
detects some malfunction
in the electronics
controlling the actuator
The circuit
is damaged.
Change control card.
Not
available
Not available
Not available HW OK
Low lithium
battery
The voltage of the lithium
battery is too low (only
detected if the lithium
battery is present and the
relevant parameter of the
miscellaneous routine is set
to “present”)
Change lithium
battery
Available
with main
voltage
Available
with main
voltage
Available with
main voltage
Lithium battery
OK
Lost phase
The alarm appears only
with 3-phase main supply.
The alarm is generated in
case of fault of one of the
phases that supply the
actuator transformer
Check main power
supply on terminals
L1, L2, L3
Not
available
Not available
Not available Phase OK
Table 18.
Warning Table
Available controls
Display
message
Condition for
warning
Action
Local
Remote
ESD
Alarm reset
High torque
in OP
(near max.)
Measured torque 10%
lower than the relevant
value configured in torque
set-up or stroke limits
routines
Check the torque
necessary to move
the valve
Available
Available
Available
Close control
High torque
in CL (near
max.)
Measured torque 10%
lower than the relevant
value configured in torque
set-up or stroke limits
routines
Check the torque
necessary to move
the valve
Available
Available
Available
Open control
Internal temp.
(near limits)
Temperature inside the
actuator enclosure higher
than 80°C or lower than
-35 °C
Find the heat source
and insulate the
actuator
Available
Available
Available
Control
temperature
>-35 °C and <80 °C
Main voltage
(near limits)
Value of the main voltage
out of the correct range
(-15% or +10% of the value
stated in the nameplate
menu) or wrong frequency
Check section of
wires and values
of voltage and
frequency
Available
Available
Available
Main voltage
correct
Contactor
cycles (max.)
Max. number of contactor
cycles reached
Change contactor
and reset operation
log
Available
Available
Available
Clear recent data
log
Maintenance
request
Date of the next
maintenance reached
Perform
maintenance
and set next
maintenance date
Available
Available
Available
Change date
Motor current Motor current greater or
lower than limits
Check electrical
motor
Available
Available
Available
Current OK
Wrong stroke
limits
The routine that monitors
the stroke limits detects
a wrong end of travel
condition
Recalibrate both
stroke limits
Available
Available
Available
Recalibrate both
stroke limits