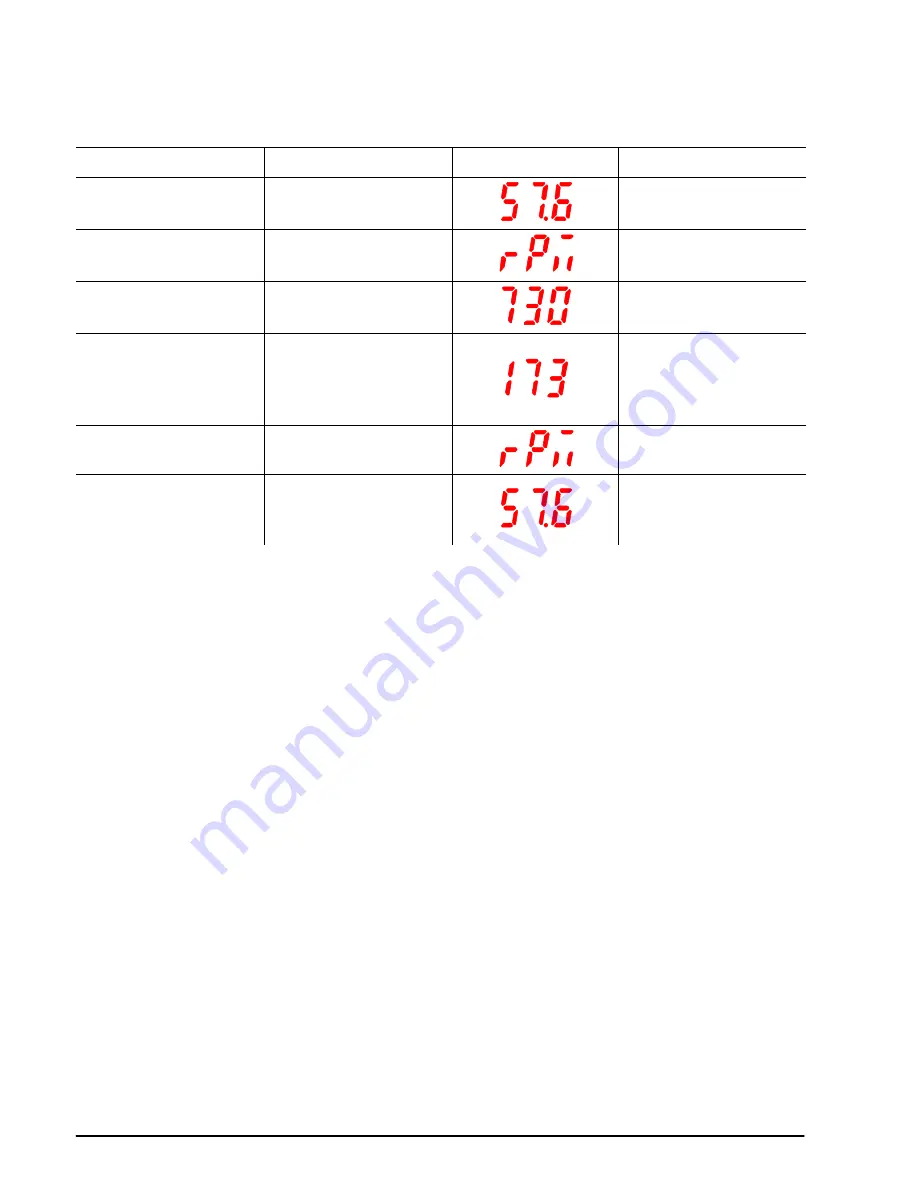
6-6 Using the Keypad
MN761
View the motor RPM on a 3 digit display
: Motor RPM in this example is 1730RPM
Action
Description
Display
Comments
Apply Power
Speed reference is
displayed 57.6Hz
Press the
Y
key until the
RPM is displayed
The next parameter is
displayed.
Press enter to view or
change setting.
Press Enter to view the
value (motor RPM)
The right most 3 digits are
displayed.
Press the
A
key to view
digits to the left
Now the left most 3 digits
are displayed. The value
is 1730 RPM.
Press Enter to exit.
Press Enter to exit.
Press the
A
key to return
to Speed Reference
display.
Motor current and other parameter values are viewed in a similar manner.
Summary of Contents for VS1SM
Page 1: ...Installation Operating Manual VS1SM Single Phase AC Drive 10 07 MN761...
Page 10: ...2 2 General Information and Ratings MN761...
Page 28: ...6 8 Using the Keypad MN761...
Page 57: ...MN761 Customizing for Your Application 8 1 Chapter 8 Customizing for Your Application...
Page 58: ...8 2 Customizing for Your Application MN761...
Page 63: ...MN761 Parameter Tables B 1 Appendix B Parameter Tables Refer to Chapter 7...
Page 64: ...B 2 Parameter Tables MN761 B 1 1 Basic Parameters Continued...
Page 69: ...Baldor District Offices...