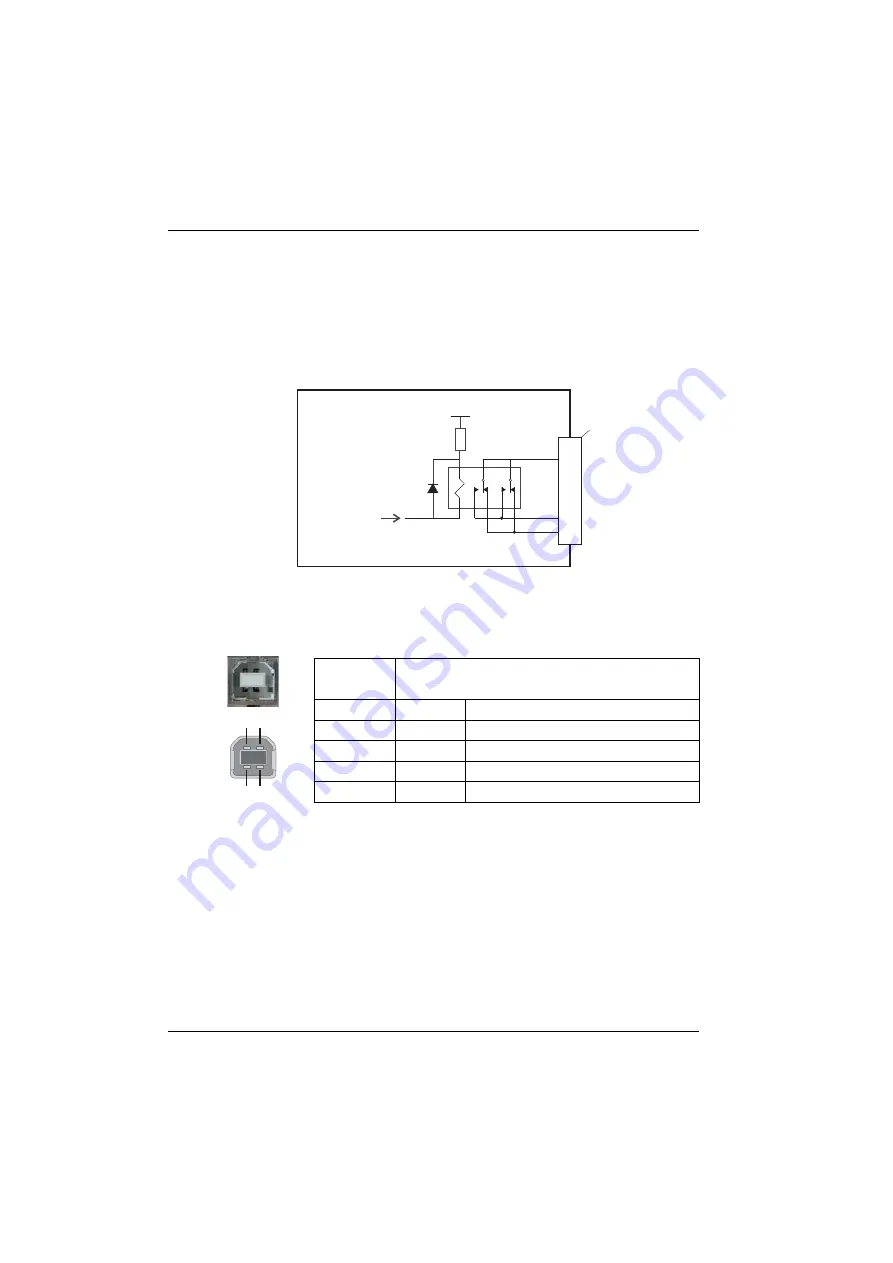
4-18 Input / Output
MN1957
www.baldormotion.com
4.4.4 Relay connections
The relay connections are available on connector X12, as shown in section 4.1.1. The relay
outputs are isolated from any internal circuits in the NextMove ESB-2. In normal operation,
while there is no error, the relay is energized and REL COM is connected to REL NO. In the
event of an error or power loss, the relay is de-energized, and REL COM is connected to
REL NC. The relay can be controlled by the
RELAY
keyword, and can be configured as the
global error output by setting
GLOBALERROROUTPUT
to 1000 (
_RELAY0
). See the Mint help
file.
Figure 22: Relay connections
4.4.5 USB port
The USB connector can be used as an alternative method for connecting the
NextMove ESB-2 to a PC running Mint WorkBench. The NextMove ESB-2 is a self-powered,
USB 1.1 (12 Mbps) compatible device. If it is connected to a slower USB1.0 host PC or hub,
communication speed will be limited to the USB1.0 specification (1.5 Mbps). If it is
connected to a faster USB2.0 (480 Mbps) host PC or hub, communication speed will remain
at the USB1.1 specification of the NextMove ESB-2.
Ideally, the NextMove ESB-2 should be connected directly to a USB port on the host PC. If it
is connected to a hub shared by other USB devices, communication could be affected by the
activity of the other devices. A 2 m (6.5 ft) standard USB cable is supplied. The maximum
recommended cable length is 5 m (16.4 ft).
Location
USB
Mating connector: USB Type B (downstream) plug
Pin Name
Description
1 VBUS
USB +5 V
2 D-
Data-
3 D+
Data+
4 GND
Ground
NextMove E
S
B-2
R
E
L COM
R
e
l
ay
R
E
L NC
R
E
L NO
X12
7
8
9
Mint
or
GLOBALERROROUTPUT
DRIVEENABLEOUTPUT
+
5
V
1
4
2
3
Servo Systems Co. • 115 Main Road • P.O. Box 97 • Montville, NJ,
07045-0097 • (973) 335-1007 • Toll Free: (800) 922-1103
Fax: (973) 335-1661 • www.servosystems.com