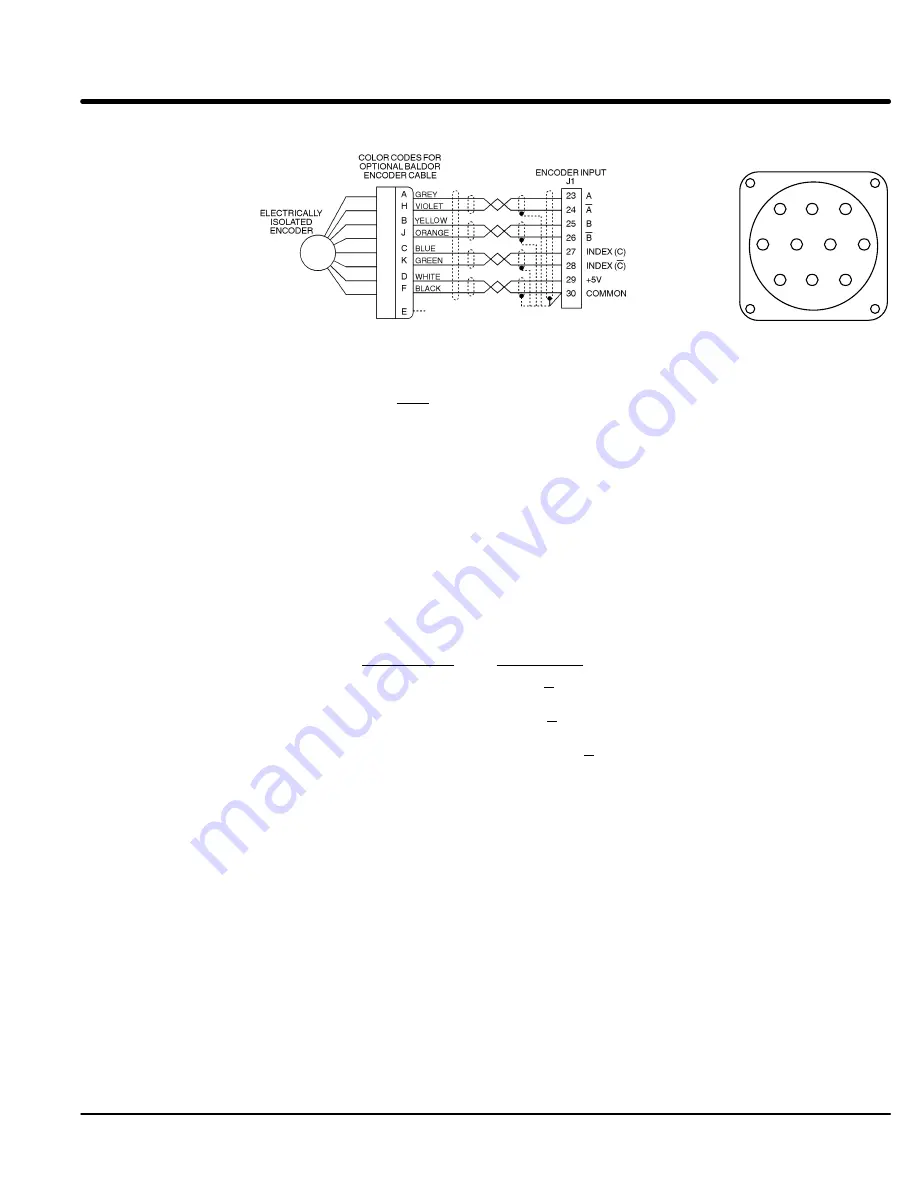
Section 1
General Information
Receiving & Installation 3-21
MN722
Figure 3-7 Encoder Connections
Terminal Tightening Torque = 7 Lb-in (0.8 Nm).
No Connection
A
B
K
H
G
J
C
F
E
D
Encoder Cable Connection
Encoder cable must be separated by at least 3” (76mm) from parallel runs of power
wires. Encoder cables that cross power wires must cross at a 90
°
angle only. Encoder
wires must be #22 AWG (0.34mm
2
) minimum, 200 feet (60m) maximum length and must
have an overall shield.
Note: Be careful not to pinch the wires’ insulation in J1 terminals as proper electrical
connection may not be made.
1.
Feed the control end of the cable through one of the “Knock-out” holes in the
control case so connections can be made inside the control.
2.
Differential Connections
Connect the cable braided shield to J1-30 at control end only.
For Baldor standard vector encoder, connect the cable ends as follows:
(See Figure 3-7.)
Encoder End
Control End
A
J1-23 (A)
H
J1-24 (A)
B
J1-25 (B)
J
J1–26 (B)
C
J1–27 Index(C)
K
J1–28 Index(C)
D
J1–29 (+5VDC)
F
J1–30 (Common)
E
No Connection
Note: Encoders other than a Baldor Standard Vector Encoder may require different
connections. Refer to information provided by the manufacturer and connect
the proper signals to the “Control End” J1 connections.
3.
Single Ended Connections
Differential inputs are recommended for best noise immunity. If only single
ended encoder signals are available, connect them to A, B, and INDEX (C)
(J1-23, J1-25 and J1-27 respectively).
Summary of Contents for 22H series
Page 5: ...Section 1 General Information iv Table of Contents MN722...
Page 105: ...Section 1 General Information 5 22 Troubleshooting MN722...
Page 109: ...Section 1 General Information 6 4 Manual Tuning the Series 22H Control MN722...
Page 137: ...Section 1 General Information A 8 Appendix A MN722...
Page 138: ...Appendix B Appendix B 1 MN722...