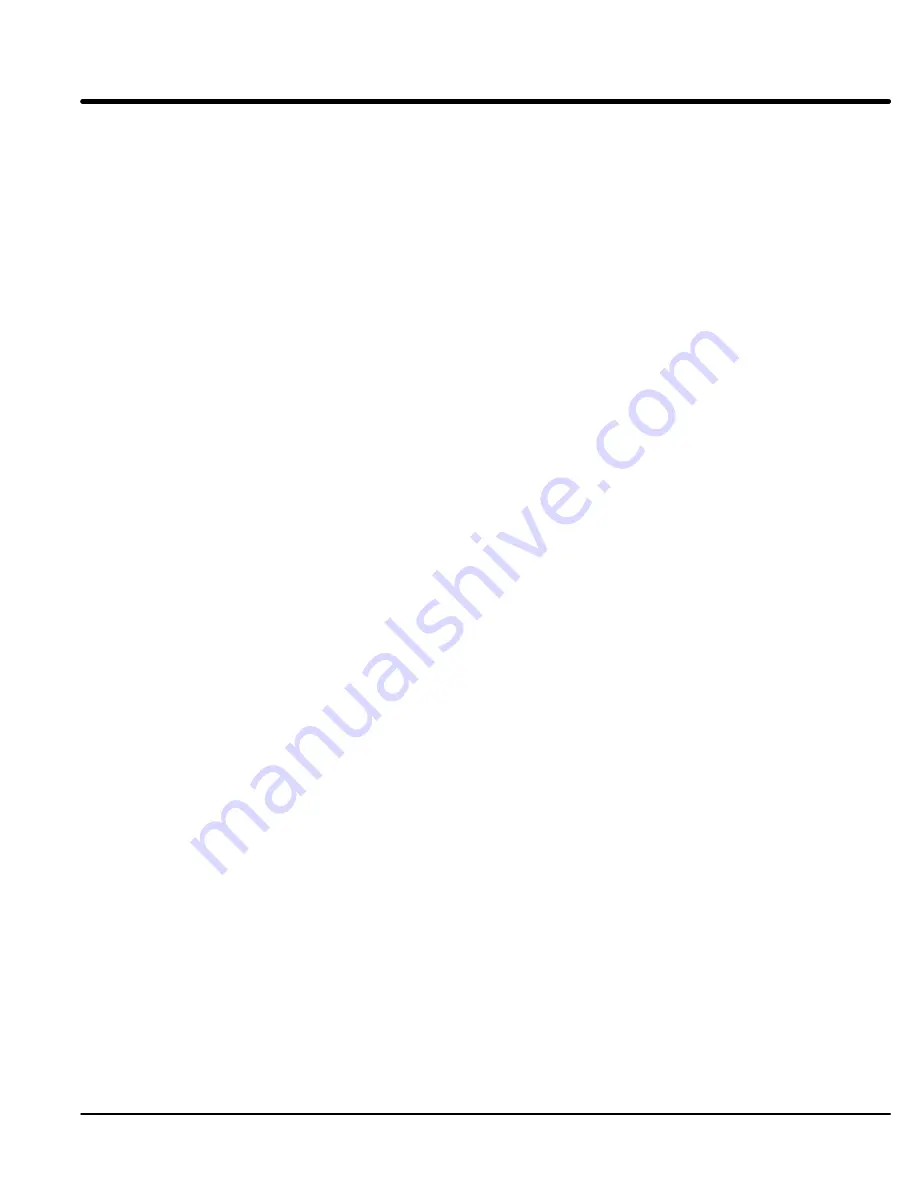
Section 1
General Information
Manual Tuning the Series 22H Control 6-3
MN722
PI Controller
Both the current and rate control loops are of the Proportional plus Integral type. If “E” is
defined to be the error signal,
E = Command – Feedback
then the PI controller operated on “E” as
Output = (K
p
* E) + (K
i
s
E dt)
where K
p
is the proportional gain of the system and K
i
is the integral gain of the system.
The transfer function (output /E) of the controller using 1/s (Laplace Operator) to denote
the integral,
Output/E = K
p
+ K
I
/ s = K
p
(s + K
i
/K
p
) /s.
The second equation shows that the ratio of K
i
/K
p
is a frequency in radians/sec. In the
Baldor Series 22H AC Vector Control, the integral gain has been redefined to be,
K
I
= (K
i
/ K
p
) / (2
p
) Hz,
and the transfer function is,
Output/E = K
p
(s + 2
p
K
I
) / s.
This sets the integral gain as a frequency in Hz. As a rule of thumb, set this frequency
about 1/10 of the bandwidth of the control loop.
The proportional gain sets the open loop gain of the system, the bandwidth (speed of
response) of the system. If the system is excessively noisy, it is most likely due to the
proportional gain being set too high.
Summary of Contents for 22H series
Page 5: ...Section 1 General Information iv Table of Contents MN722...
Page 105: ...Section 1 General Information 5 22 Troubleshooting MN722...
Page 109: ...Section 1 General Information 6 4 Manual Tuning the Series 22H Control MN722...
Page 137: ...Section 1 General Information A 8 Appendix A MN722...
Page 138: ...Appendix B Appendix B 1 MN722...