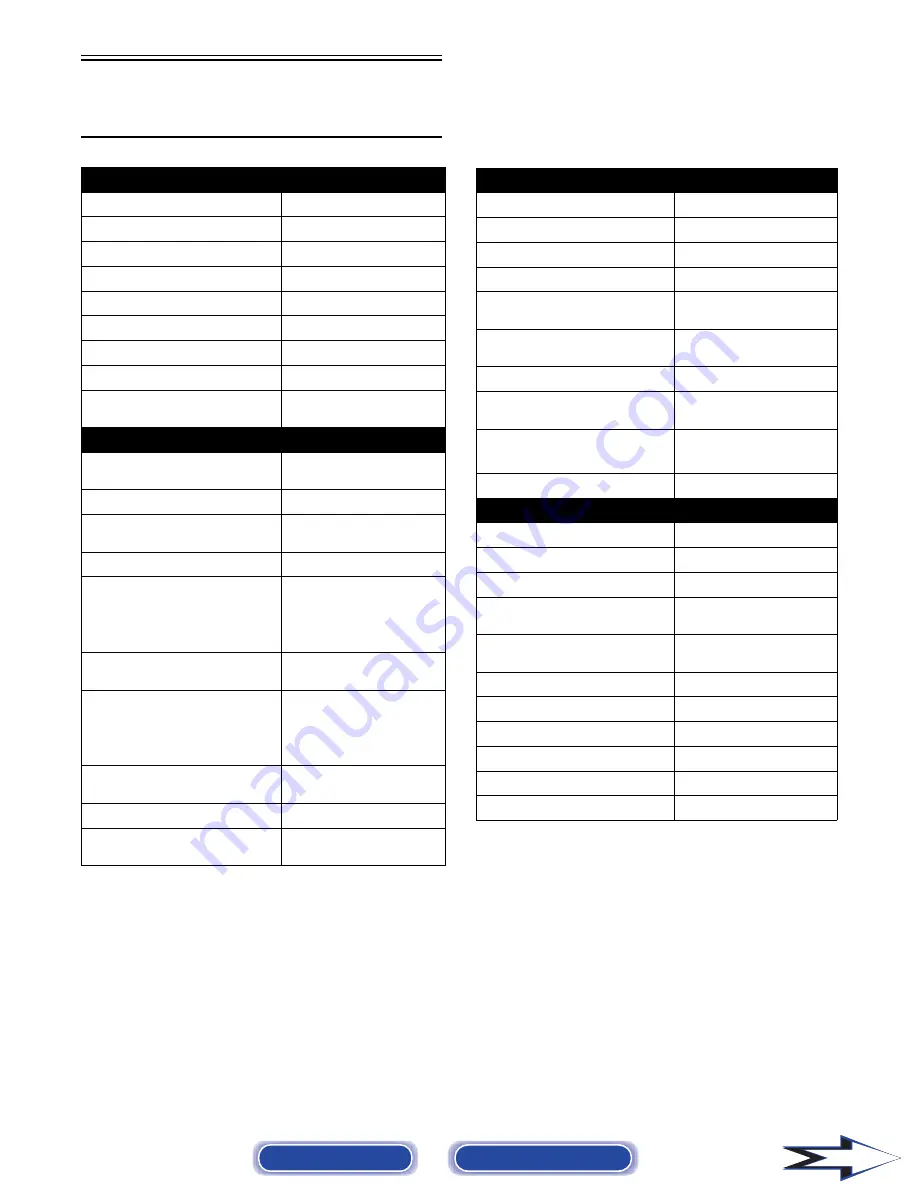
1-2
General Specifications*
(DVX Model)
* Specifications subject to change without notice.
CARBURETOR
Type
Keihin PTG-22
Main Jet
95
Slow Jet
35
Pilot Screw Setting (turns)
1 1/2
Jet Needle
NBSD-3
Needle Jet
3.6/2.5
Idle RPM
1250-1350
Float Arm Height
14.8 mm (0.58 in.)
Throttle Cable Free-Play
(at lever)
1-4 mm
(1/16-3/16 in.)
ELECTRICAL
Ignition Timing
5° BTDC (“F” mark)@1000
RPM
Spark Plug Type
NGK DPR7EA-9
Spark Plug Gap
0.6-0.7 mm
(0.024-0.028 in.)
Spark Plug Cap
4500-6150 ohms
Ignition Coil
Resistance
(primary)
(secondary)
2.4-3.0 ohms
(terminal to terminal)
12,300-16,600 ohms
(high tension - plug cap
removed - to ground)
Ignition Coil Peak
Voltage
(primary/CDI)
14.0 DC volts
(black/white to green/gray)
Magneto Coil
Resistance
(trigger)
(charging)
105-110 ohms
(black/yellow to green/
white)
Less than 1 ohm
(yellow to yellow)
Stator Coil Peak
Voltage
(trigger) 1.1-1.4 DC volts
(blue/yellow to green/white)
Magneto Output (approx)
220W @ 5000 RPM
Stator Coil
Output
(no load) 40-60 AC volts @3000
RPM (yellow to yellow)
CHASSIS
Dry Weight (approx)
186 kg (410 lb)
Length (overall)
168.3 cm (66.25 in.)
Height (overall)
114.9 cm (45.25 in.)
Width (overall)
106.0 cm (41.75 in.)
Suspension Travel
(Front)
(Rear)
15.5 cm (6.1 in.)
16.5 cm (6.5 in.)
Brake Type
Hydraulic w/Brake Lever
Lock and Auxiliary Brake
Wheelbase
117.9 cm (46.4 in.)
Tire Size
(Front)
(Rear)
AT21 x 7-10
AT20 x 11-9
Tire Inflation Pressure
2
(Front)
2
(Rear)
0.28 kg/cm
2
(4 psi)
0.25 kg/cm
2
(3.5 psi)
Turning Radius
2.95 m (9.7 ft)
MISCELLANY
Gas Tank Capacity (rated)
13 L (3.43 U.S. gal.)
Reserve Capacity
4.54 L (1.2 U.S. gal.)
Engine Oil Capacity
1.6 L (1.7 U.S. qt)
Transmission (Overhaul)
Lubricant Capacity
(Change)
400 ml (13.5 fl/oz)
300 ml (10.1 fl/oz)
Gasoline (recommended)
87 Octane Regular
Unleaded
Engine Oil (recommended)
SAE 5W-30
Cooling System Capacity
1.6 L (1.7 U.S. qt)
Brake Fluid
DOT 4
Taillight/Brakelight
12V/5W/21W
Headlight
12V/35W (2)
Starting System
Electric
Back to TOC
Back to Section TOC
Next
Summary of Contents for DVX 250 2007
Page 1: ......