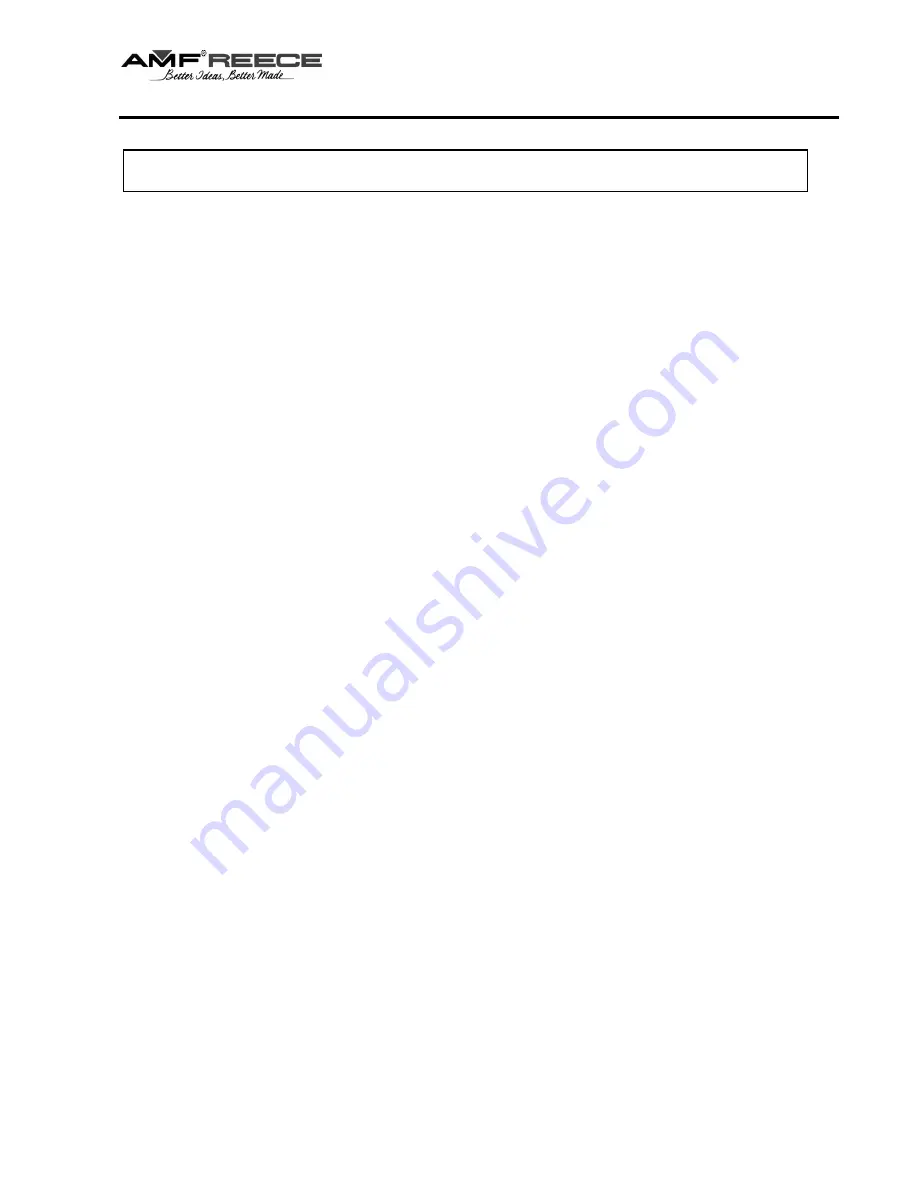
2-3
S-104-100
Revised 09/2004
e-mail: [email protected]; [email protected]; website: www.amfreece.com
Phones: +420 582 309 146 (Service), +420 582 309 286 (Spare Parts) ; Fax: +420 582 360 606
TROUBLESHOOTING
SYMPTOM
POSSIBLE CAUSE
POSSIBLE SOLUTION
Motor fails to start.
Motor started and ran for a
short period of time, then
stopped.
The machine fails to cycle
No power to the motor
Incorrect voltage
Transformer
Faculty motor starter
Left wheel dog will not engage
drive hub.
Spring on shifting lever weak
or broken.
Drive hub broken
Clamp screw on shifter spool
loose
Excessive cutting pressure
Belt tension is not correct
Rocker arm out of adjustment
Spring on clutch is broken
Dirt in sector teeth
Incorrect motor rotation
Belts has fallen off
Check electrical plug and wiring
Check with a voltage meter
Check transformer output
Replace starter
Recheck stop motion
Check and replace
Replace the drive hub
Adjust and tighten the timing on the
left hand wheel in relation to rocker
shaft and lever.
Re-adjust cutting pressure
Re-adjust tension
Adjust roll pressure on length gauge
Adjust rocker arm and stop motion
Adjust timing of left hand wheel in
relation to stop wheel release
Replace spring
Clean sector teeth and test by rotating
complete assembly back and forth
Check power supply and wiring
Re-install belt
.