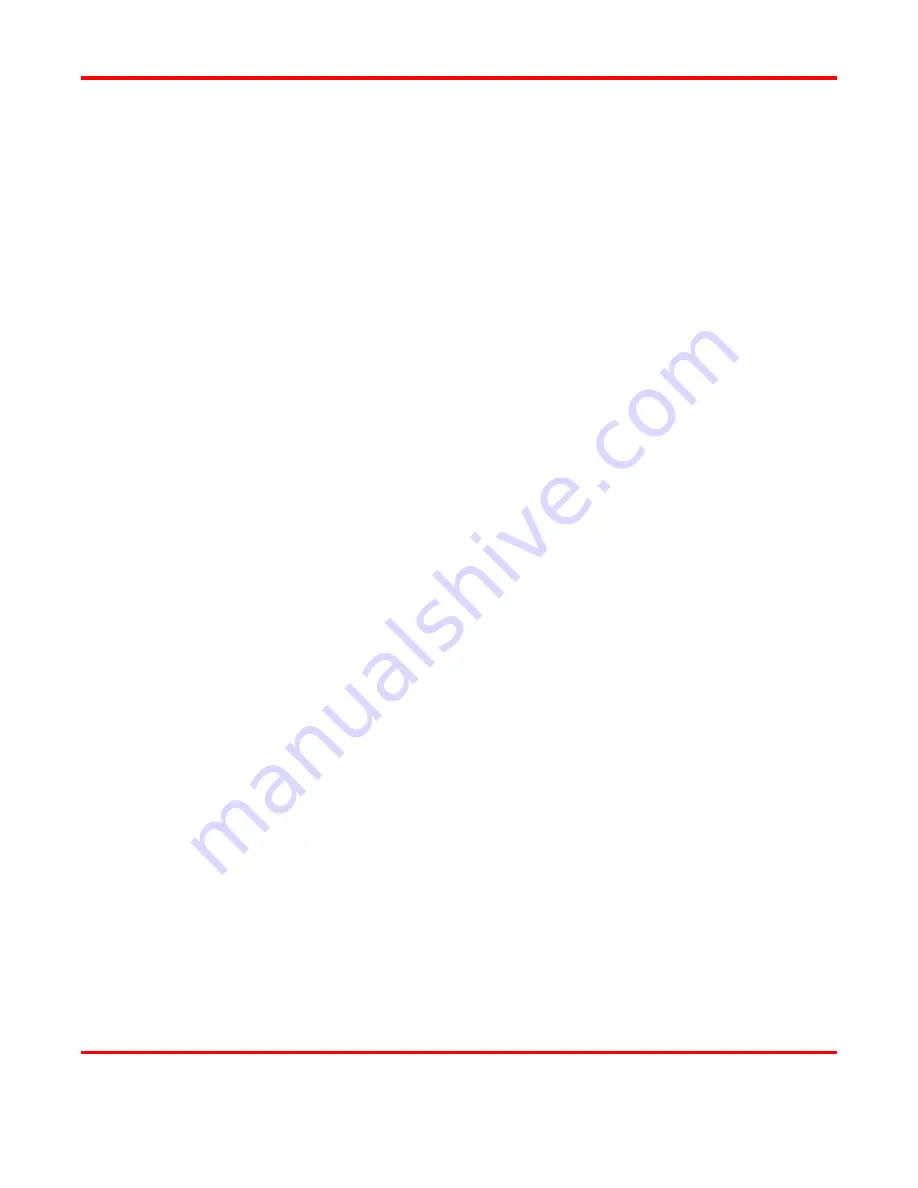
CHAPTER 3: USING UB25 WELDING FUNCTIONS
UB25 LINEAR DC RESISTANCE WELDING CONTROL
3-8
990-665
Section IV. Weld Monitor
Introduction
The Power Supplies feedback sensors not only control weld energy output, but they can also be used to
monitor each weld. The Power Supplies monitor features allow you to view graphic representations of
welds, visually compare programmed welds to actual welds, look at peak or average energy values, set
upper and lower limits for welds, and make use of these features:
•
Active Part Conditioner (APC)
•
Energy Limits
•
Pre-Weld Check
Active Part Conditioner (APC)
Application
•
Displace surface oxides and contamination
•
Reduce contact resistances before delivering the main weld energy.
Description
In the production environment, it is common to see large variations in:
•
Oxide and contamination
•
Plating thickness and consistency
•
Shape and fit up
•
Contact resistances due to varying part fit up
In order for a weld to occur, the surface oxides and contamination must be displaced to allow proper
current flow through the parts. Levels of oxide and contamination vary from part to part over time,
which can have an adverse effect on the consistency of the welding process. If production parts are
plated, there can also be a plating process variation over time resulting in inconsistent welds. These
minor material variations are a major cause of process instability, and it is best welding practice to
seek to minimize their effect.
Active Part Conditioner
is designed to cope with material contamination, variation and can be
programmed to apply the exact power to the parts required to displace oxide or contaminants. In
addition, the “Part Conditioner” pulse will terminate at a precise current flow preventing the sudden
high flow, which occurs when the oxide is displaced. This prevents weld splash and material
expulsion, which occurs as a result of an excessively fast heating rate. Part conditioning can help to
reduce variations in contact resistance from part to part caused by different fit up of parts. It will
stabilize the contact resistances before the main welding pulse, therefore reducing variation from weld
to weld.