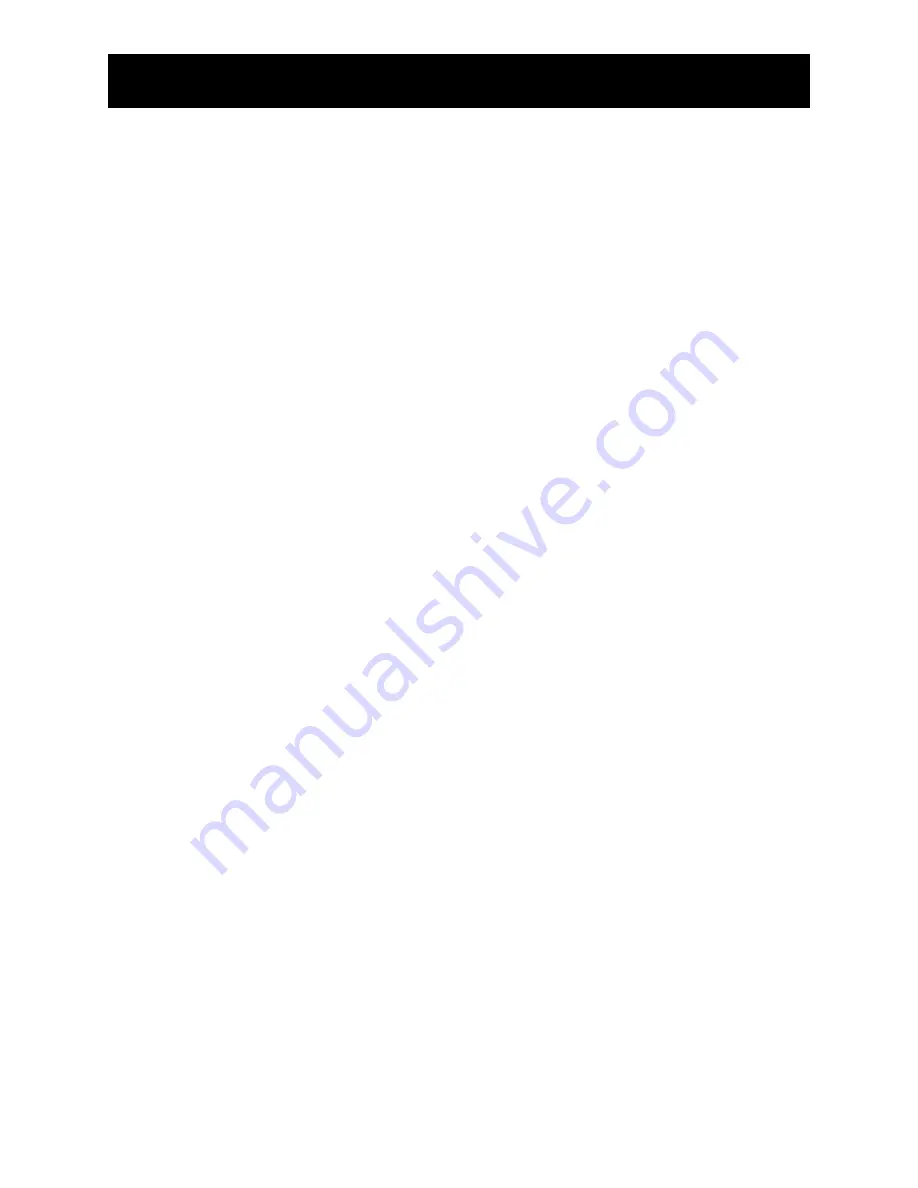
44
APPENDIX G: FAQ
’
S
Q: ANGLE MEASUREMENT SEEMS TOO HIGH.
The controller starts to measure angle of rotation during the rundown when THOLD
(threshold torque) is reached. If the threshold torque setting is below the prevailing
torque of the joint, the tool will start measuring angle before the fastener is seated,
resulting in a higher angle reading than anticipated. Ensure that the threshold torque val-
ue is above any anticipated prevailing torque of the joint.
Q: HOW CAN I RESET TO ALL THE FACTORY SETTINGS?
There are three groups of settings that can be reset
-
parameter sets, logic inputs/
outputs, and calibration value. Within the ADMIN menu of the KDM, select RESET DE-
FAULTS. Resetting the parameter sets will erase all existing parameter set values. Re-
setting logic inputs/outputs will revert to the factory installed settings. Resetting the cali-
bration value will revert the tool
’
s calibration value to the factory setting burned into the
tool
’
s identification board. Resetting defaults is easily done using Toolware as well.
Refer to the Toolware users guide for details.
Q: WHAT IS ADAPTIVE CONTROL?
Upon reaching target torque, the controller signals the tool to shut off and the tool stops.
Depending on the speed of the tool and the joint rate, the final torque output may be
higher than the target torque. This difference in torque is called
“
overshoot
”.
Adaptive
Control averages and centers the final torque readings around the target torque value.
It averages the overshoot torque on 10 consecutive rundowns. After that, it pre
-
targets
the tool to shut off before reaching the target so that the final reading is closer to your
target torque setting. For example, if the target torque is 10 Nm, and the average of 10
readings is 10.2 Nm, using adaptive control will calculate the average overshoot torque
of 0.2 Nm (10.2
-
10.0) and the tool will shut off at 9.8 Nm, so that the final torque
reading is 10.0 Nm. Because of the way Cpk is measured, having more readings above
the target torque decreases the Cpk value. Using Adaptive Control will result in a higher
Cpk value since the range of the final torque readings is more centered on your target
torque setting.
Q: WHAT IS THE CAL VALUE?
The cal value of an AcraDyne tool is based on a scale of 0
-
256 points. By adjusting this
value, the torque values generated by the tool
’
s transducer can be correlated with a
torque value as determined by a master calibration transducer. Using the Calibrate
Torque or Calibrate Angle features in Toolware with a Master Transducer can insure that
your AcraDyne tool is operating in specification against the Master Transducer in your
facility. Refer to the Toolware user
’
s guide for details
Q: WHAT OTHER METHODS EXIST FOR PROGRAMMING THE iEC CONTROLLER?
By connecting the controller to a computer through the CAN connection or an existing
Ethernet system, ToolWare can be used to conduct a wide range of programming, diag-
nostic and analytical procedures. For more information on ToolWare, refer to the Tool-
Ware Users Guide section of this manual or contact your AIMCO sales representative.
Summary of Contents for iEC
Page 1: ...AcraDyne iEC DC Tool Controllers User Guide...
Page 35: ...35 Appendix B KDM Menu Structures Main Menu Structure Parameter Set up Menu...
Page 36: ...36 APPENDIX B KDM Menu Structures Administration Menu...
Page 45: ...45 Notes...
Page 46: ...46 Notes...
Page 47: ...47 Notes...